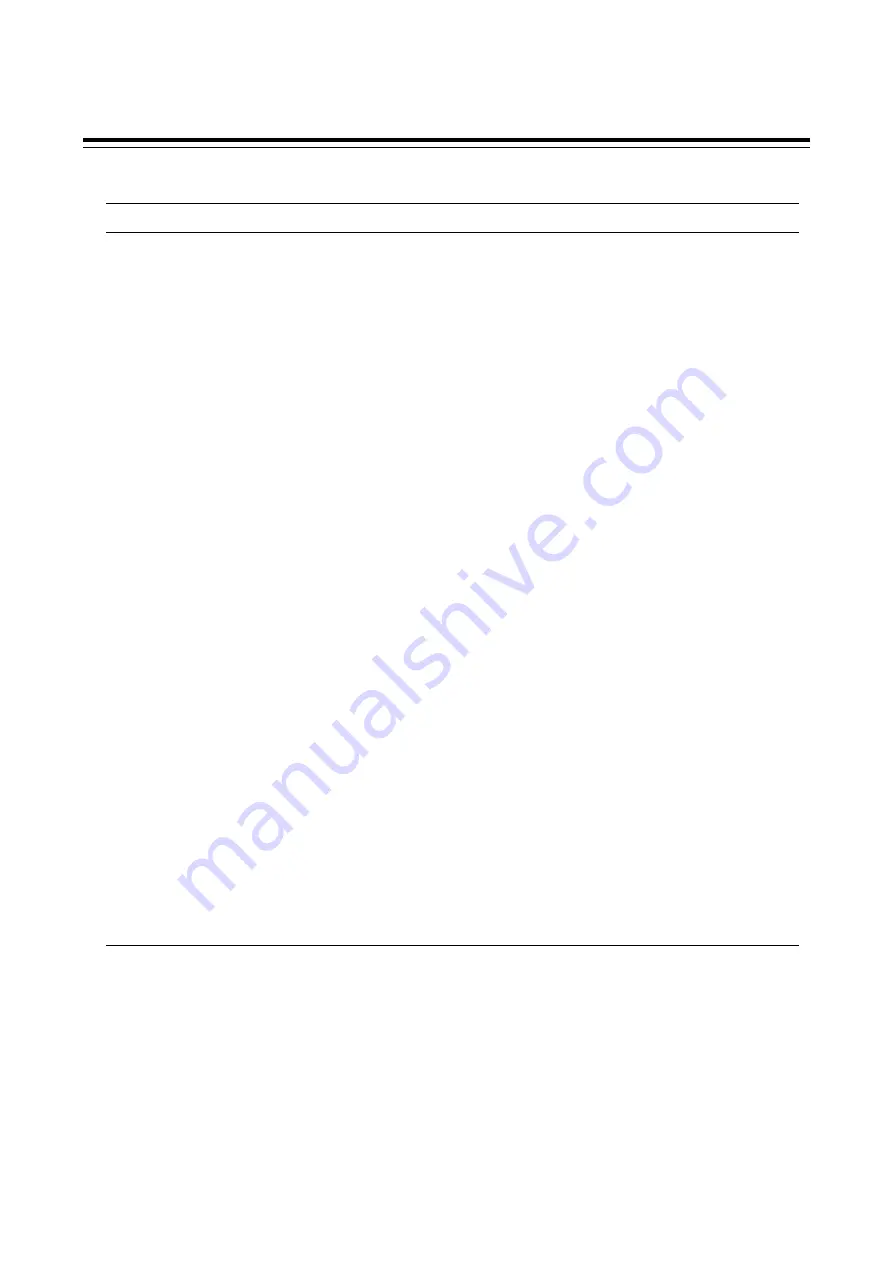
APPENDIX
IMR01Y36-E2
110
Continued from the previous page.
ID
Description
Get
Set
Type
Value
Attributes
31
Unused
No
No
UINT
0 to 65535
32
Unused
No
No
UINT
0 to 65535
33
PID/AT
transfer
1, 2
Yes
Yes
INT
Refer to P. 51
34
Auto/Manual transfer
Yes
Yes
INT
Refer to P. 52
35
Remote/Local transfer
Yes
Yes
INT
Refer to P. 52
36
RUN/STOP
transfer
3
Yes
Yes
INT
Refer to P. 52
37
Memory area transfer
Yes
Yes
INT
Refer to P. 52
38
Interlock release
Yes
Yes
INT
Refer to P. 52
39
Event 1 set value (EV1)
Yes
Yes
INT
Refer to P. 52
40
Event 2 set value (EV2)
Yes
Yes
INT
Refer to P. 52
41
Event 3 set value (EV3)
Yes
Yes
INT
Refer to P. 52
42
Event 4 set value (EV4)
Yes
Yes
INT
Refer to P. 52
43
Control loop break alarm (LBA) time
Yes
Yes
INT
Refer to P. 52
44
LBA deadband
Yes
Yes
INT
Refer to P. 52
45
Set value (SV)
Yes
Yes
INT
Refer to P. 52
46
Proportional band [heat-side]
Yes
Yes
INT
Refer to P. 53
47
Integral time [heat-side]
Yes
Yes
INT
Refer to P. 53
48
Derivative time [heat-side]
Yes
Yes
INT
Refer to P. 53
49
Control response parameter
Yes
Yes
INT
Refer to P. 53
50
Proportional band [cool-side]
Yes
Yes
INT
Refer to P. 53
51
Integral time [cool-side]
Yes
Yes
INT
Refer to P. 54
52
Derivative time [cool-side]
Yes
Yes
INT
Refer to P. 54
53
Overlap/Deadband
Yes
Yes
INT
Refer to P. 54
54
Manual reset
Yes
Yes
INT
Refer to P. 54
55
Setting change rate limiter (up)
Yes
Yes
INT
Refer to P. 54
56
Setting change rate limiter (down)
Yes
Yes
INT
Refer to P. 54
57
Area soak time
Yes
Yes
INT
Refer to P. 54
58
Link area number
Yes
Yes
INT
Refer to P. 54
59
Heater break alarm (HBA) set value
Yes
Yes
INT
Refer to P. 55
60
Heater break determination point
Yes
Yes
INT
Refer to P. 55
61
Heater melting determination point
Yes
Yes
INT
Refer to P. 55
62
Unused
No
No
UINT
⎯
63
Unused
No
No
UINT
⎯
64
Unused
No
No
UINT
⎯
65
PV bias
Yes
Yes
INT
Refer to P. 55
66
PV digital filter
Yes
Yes
INT
Refer to P. 55
67
PV ratio
Yes
Yes
INT
Refer to P. 55
68
PV low input cut-off
Yes
Yes
INT
Refer to P. 55
1
It is validated only via Explicit message communication. If “PID/AT transfer” is set as the setting
data item (OUT) by the “Controller communication item setting object (0xC7: C7Hex)” which sets
communication data items via Polling I/O communication, it becomes the same as that when set at
“0.” If set as the measured data item (IN), it can be used as is.
2
When using PID/AT transfer by Polling I/O communication, it is necessary to set Action mode
selection (Attributes ID: 246) to “PID/AT transfer by Polling I/O communication is validated.”
3
If “RUN/STOP transfer” is set as the setting data item (OUT) by the “Controller communication
item setting object (0xC7: C7Hex)” which sets communication data items via Polling I/O
communication, it becomes the same as that when set at “0.” If set as the measured data item (IN), it
can be used as is.
Continued on the next page.