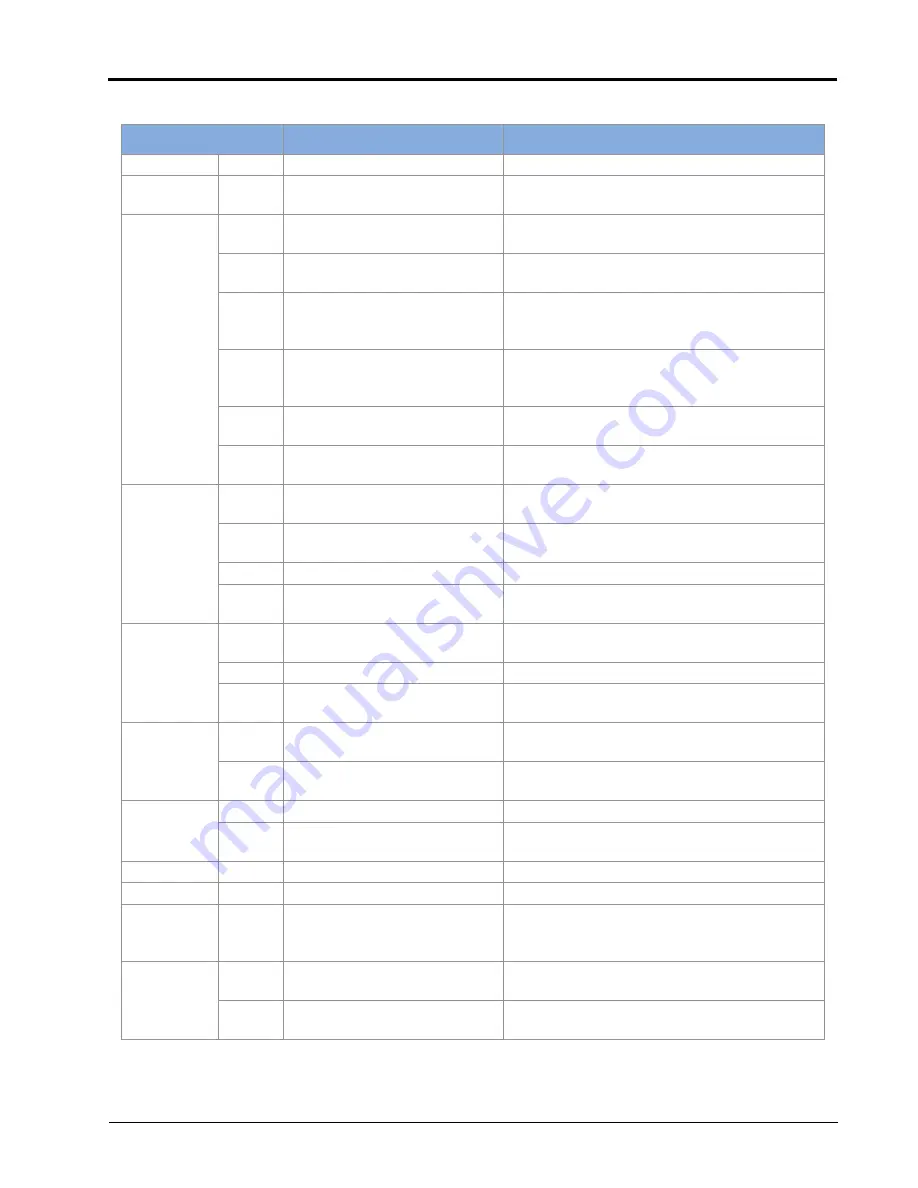
Diagnostics and Troubleshooting: Diagnostic Trouble Codes (DTC)
59
DIAGNOSTICS AND TROUBLESHOOTING
TABLE 2.
HDU/MDU/IDU DTC Codes
Code ID
Display Name
Description
630
.13
SCU Not Calibrated
SCU is not on a calibrated profile
2901
.2
Incompatible HW SCU
The current software is incompatible with
this hardware.
3509
.3
WAS Supply High
Wheel angle sensor power out is above its
expected tolerance.
.4
WAS Supply Low
Wheel angle sensor power out is below its
expected tolerance.
.31
WAS Alignment Fault
Machine heading and wheel direction does
not match. Check wheel angle sensor and/or
reset system.
.7
Curvature Mismatch
The wheel angle sensor measurement is not
aligned with the yaw rate sensor
measurement.
.5
SID 1 Signal High
The disengage sensor signal (#1) is above
the upper limit.
.6
SID 1 Signal Low
The disengage sensor signal (#1) is below
the low limit.
523899
.7
Small WAS Range
Their isn’t sufficient range between the
wheel angle sensor setpoints.
.3
WAS 1 Sig High
The wheel angle sensor signal (#1) is above
the upper limit.
.4
WAS 1 Sig Low
The wheel angle sensor signal (#1)
.10
WAS 1 Sig Rate
Wheel angle sensor measurement out of
spec. Check sensor mounting and harness.
523900
.3
WAS 2 Sig High
The wheel angle sensor signal (#2) is above
the upper limit.
.4
WAS 2 Sig Low
The wheel angle sensor signal (#2).
.10
WAS 2 Sig Rate
Wheel angle sensor measurement out of
spec. Check sensor mounting and harness.
523902
.5
SID 2 Signal High
The disengage sensor signal (#2) is above
the upper limit.
.6
SID 2 Signal Low
The disengage sensor signal (#2) is below
the low limit.
1504
.14
OP Active
Operator out of seat.
.31
Oprator Presence Wrn
The operator is out of the seat and the
system is about to disengage
702
.1
Master Off
The master switch sensor is currently off.
701
.2
Auto Resume Error
The resume switch is stuck on.
523907
.5
EH Vlve Not Cnnected
No current draw detected when
commanding the valve (HDU) or motor
(MDU).
168
.4
HC Low Voltage SCU
The input voltage to the system is below the
low limit.
.3
HC High Voltage SCU
The input voltage to the system is above the
upper limit.
Summary of Contents for SC1
Page 28: ...CHAPTER 3 24 Raven SC1 TC1 Calibration Operation Manual for Towed Implements...
Page 36: ...CHAPTER 4 32 Raven SC1 TC1 Calibration Operation Manual for Towed Implements...
Page 48: ...CHAPTER 5 44 Raven SC1 TC1 Calibration Operation Manual for Towed Implements...
Page 54: ...CHAPTER 6 50 Raven SC1 TC1 Calibration Operation Manual for Towed Implements...
Page 74: ...CHAPTER 8 70 Raven SC1 TC1 Calibration Operation Manual for Towed Implements...
Page 76: ...Index 72 Raven SC1 TC1 Plough Steering Calibration and Operation Manual...