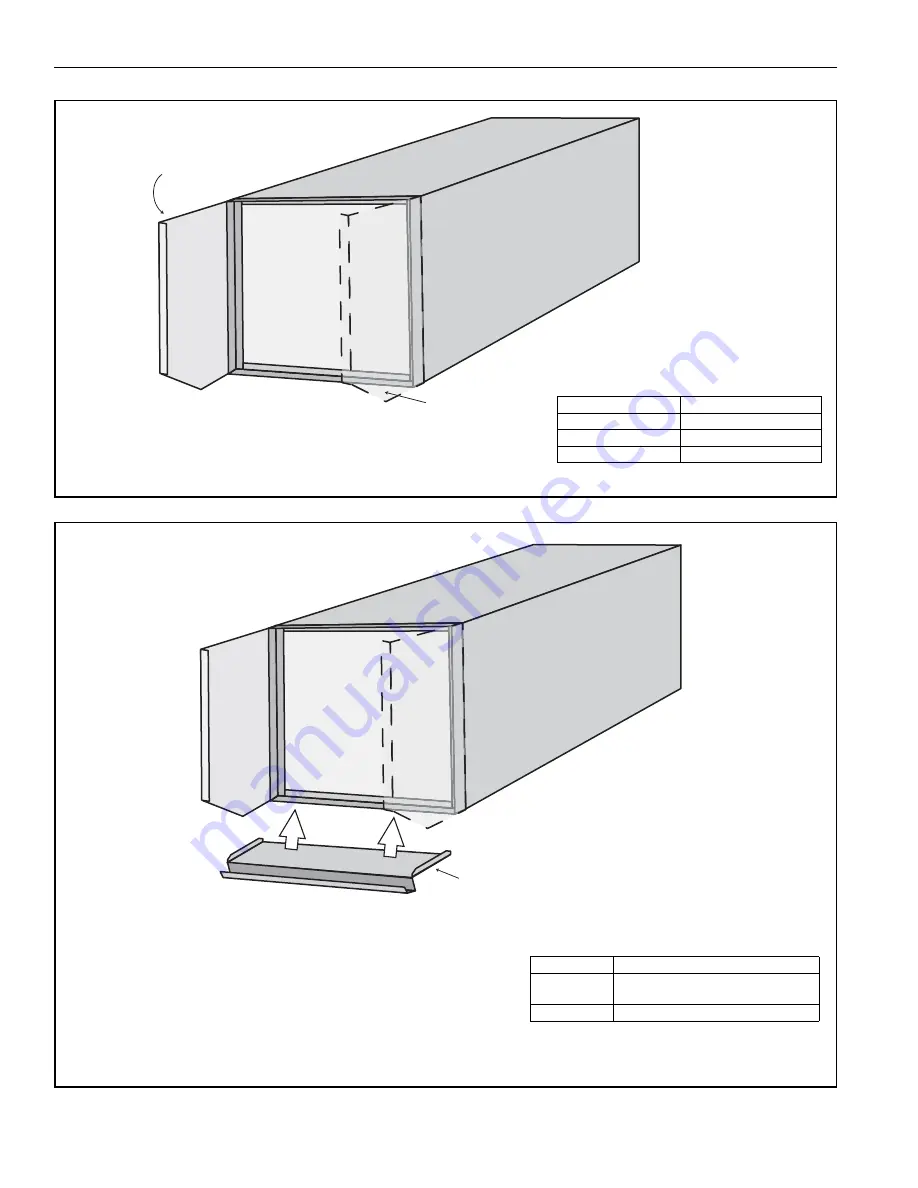
B-S
ERIES
I
NSTALLATION
, O
PERATION
AND
S
ERVICE
M
ANUAL
56 of 147
Step 12.3.2
Step 12.3.3
Panel 1 Left
Panel 1 Right
Attach an innermost side
w
all panel 1 to each side
attaching flange
u
sing se
v
en TEK self-tapping scre
w
s.
NOTE:
Flanges face in
w
ard.
Description
Part Number
Left Side Panel #1
13205080 / 13305080
Right Side Panel #1
13205081 / 13305081
TEK Scre
w
s
13404
Bottom Rail
For Model 2020:
Attach the bottom panel to the bottom
mo
u
nting flange
w
ith se
v
en TEK self-tapping scre
w
s. Attach
to each side panel
w
ith t
w
o TEK self-tapping scre
w
s.
For Model 2030:
Attach bottom panel to the bottom mo
u
nting
flange
w
ith nine TEK self-tapping scre
w
s. Attach to each side
panel
w
ith t
w
o TEK self-tapping scre
w
s.
NOTE:
Ens
u
re that the side tabs of the bottom panel are to
the inside of the side panels.
Description
Part Number
Bottom Rail
13205072 / 13305072 /
13205095 / 13305100
TEK Scre
w
s
13404
Summary of Contents for 2005
Page 2: ......
Page 4: ......
Page 8: ......
Page 10: ......
Page 31: ...SECTION 7 ROOF CURB 21 of 147 FIGURE 12 Curb Mounting Air Handler Roof Curb Fastening Detail...
Page 154: ...B SERIES INSTALLATION OPERATION AND SERVICE MANUAL 144 of 147...
Page 158: ......
Page 160: ......
Page 161: ......
Page 162: ......