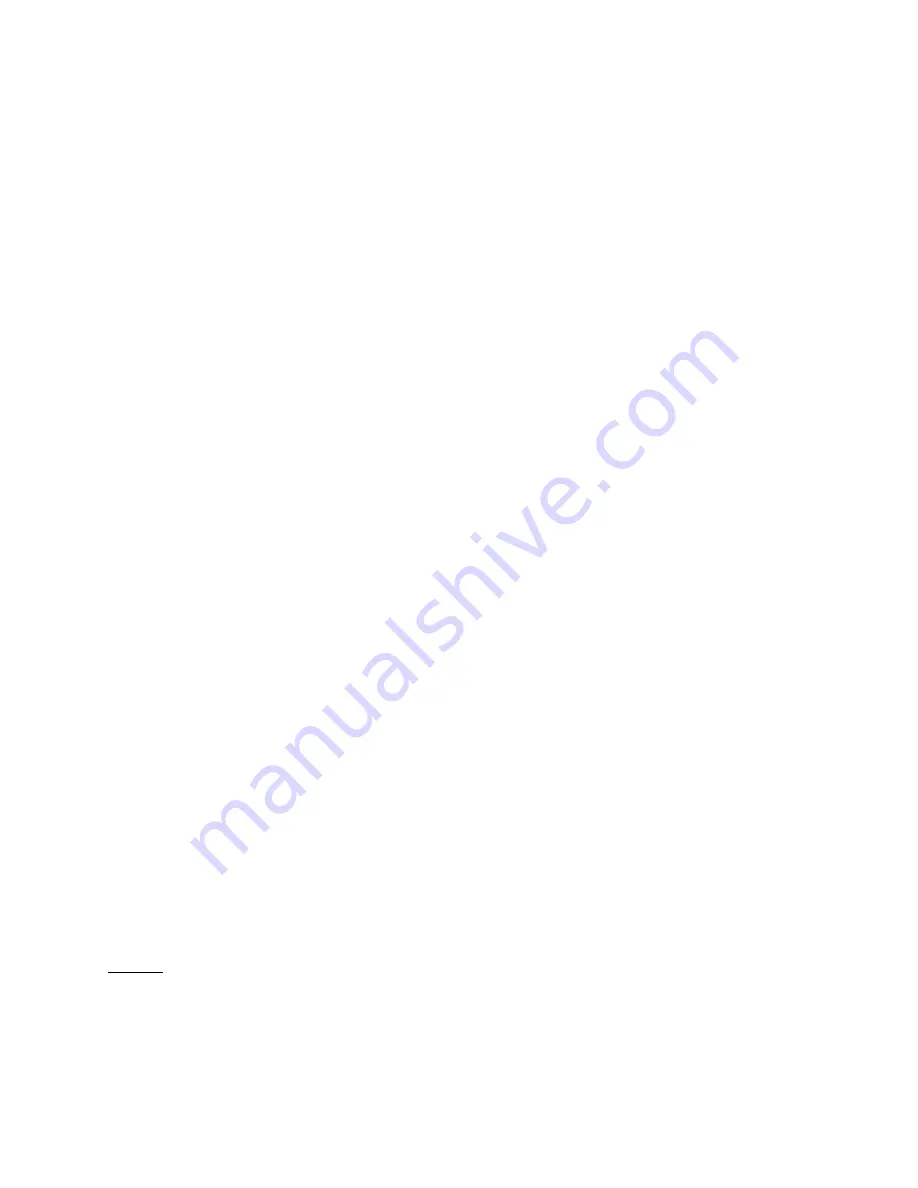
11-5
2.
Stop engine and remove all spark plugs. Spray a liberal amount of Storage Fogging Oil into the spark
plug holes.
3.
Pull starter to distribute the fogging oil throughout the cylinders. Install and torque the spark plugs.
! Leave
Leave
Leave
Leave spark plug leads disconnected to prevent accidental starting during storage.
spark plug leads disconnected to prevent accidental starting during storage.
spark plug leads disconnected to prevent accidental starting during storage.
spark plug leads disconnected to prevent accidental starting during storage.
!
3. Examine all hardware you loosened or removed. Replace damaged or missing parts with genuine RaCE
parts or equivalent. These fasteners are made of special materials to resist weakening and rusting. Do not
Do not
Do not
Do not
substitute these fasteners with nuts and bolts, which look the same. Using the wrong nuts and bolts may
substitute these fasteners with nuts and bolts, which look the same. Using the wrong nuts and bolts may
substitute these fasteners with nuts and bolts, which look the same. Using the wrong nuts and bolts may
substitute these fasteners with nuts and bolts, which look the same. Using the wrong nuts and bolts may
result in sudden, unexpected loss of engine control.
result in sudden, unexpected loss of engine control.
result in sudden, unexpected loss of engine control.
result in sudden, unexpected loss of engine control.
!
4. Inspect the engine's steering, t
Inspect the engine's steering, t
Inspect the engine's steering, t
Inspect the engine's steering, throttle, and shift systems for damage due to corrosion, aging, lack of
hrottle, and shift systems for damage due to corrosion, aging, lack of
hrottle, and shift systems for damage due to corrosion, aging, lack of
hrottle, and shift systems for damage due to corrosion, aging, lack of
maintenance, or abuse. Follow the maintenance and lubrication recommendations when servicing these
maintenance, or abuse. Follow the maintenance and lubrication recommendations when servicing these
maintenance, or abuse. Follow the maintenance and lubrication recommendations when servicing these
maintenance, or abuse. Follow the maintenance and lubrication recommendations when servicing these
systems.
systems.
systems.
systems.
5
Replace the engine's fuel filter.
6
Clean and inspect oil reservoir. Fill the oil tank with recommended oil to reduce or prevent condensation
from forming in the tank during storage.
7
Remove propeller and check for damage. A slightly bent propeller blade can hardly be noticed but will
affect the performance of the engine. Clean the propeller shaft and lubricate with grease.
8
Drain and refill the gear case. Lubricate the engine. See Gear case Lubrication
Gear case Lubrication
Gear case Lubrication
Gear case Lubrication in this section.
9
Check the engine carefully. Make sure screws and nuts are tight. Replace damaged or worn parts.
10
Make sure electrical and fuel system fasteners and clamps are tight and in good condition. Failure to do
. Failure to do
. Failure to do
. Failure to do
so may cause electrical sparks and fuel leakage under the engine cover. Fire and explosion could occur
so may cause electrical sparks and fuel leakage under the engine cover. Fire and explosion could occur
so may cause electrical sparks and fuel leakage under the engine cover. Fire and explosion could occur
so may cause electrical sparks and fuel leakage under the engine cover. Fire and explosion could occur.
11
Replace engine cover. Use touch-up paint where needed.
12
Coat all outside painted surfaces of engine with automotive wax.
13
The engine should be stored in a normal (vertical) position on an adequate engine stand.
Tune
Tune
Tune
Tune----Up Procedure
Up Procedure
Up Procedure
Up Procedure for Raider Outboard
for Raider Outboard
for Raider Outboard
for Raider Outboard
The following is described in the outboard does not meet specifications. It is a first step to decide if a tune-up is all that is
required verses a major overhaul of the Raider.
1. Visually inspect engine for leaks, missing or loose parts, or other obvious defects.
2. Compression check
Compression check
Compression check
Compression check - Proper compression is essential for good engine performance. An engine with uneven
compression cannot be properly tuned.
•
Operate the engine until it reaches its normal operating temperature. Stop engine.
•
Remove and inspect all spark plugs. Check their condition.
•
Install thread-type compression tester in spark plug hole.
•
With throttle in wide-open position, pull engine through at least four compression strokes.
Variation between cylinders should not exceed 15 PSI (103 kPa).
Results:
Results:
Results:
Results:
IF
IF
IF
IF the engine has equal compression, is hard to start, and
and
and
and operates poorly, check for:
•
scored cylinder walls
•
damaged pistons
•
stuck piston rings
•
worn piston rings
IF
IF
IF
IF the engine shows a variation greater than 15 PSI (103 kPa), check for :
Summary of Contents for 50 HP TLDI
Page 3: ......
Page 9: ...1 2 2 O 2 O 2 O 2 Outline Dimensions utline Dimensions utline Dimensions utline Dimensions...
Page 17: ...1 10...
Page 19: ...2 2...
Page 20: ...2 1...
Page 35: ...2 16 5 Special Tools 5 Special Tools 5 Special Tools 5 Special Tools...
Page 43: ...2 24...
Page 48: ...3 5...
Page 50: ...3 7...
Page 54: ...3 11...
Page 57: ...4 2 1 1 1 1 Power Uni Power Uni Power Uni Power Unit t t t...
Page 60: ...4 5...
Page 66: ...4 11...
Page 68: ...4 13...
Page 72: ...4 17...
Page 75: ...4 20...
Page 86: ...4 31...
Page 97: ...4 42 Piston and Crankshaft Piston and Crankshaft Piston and Crankshaft Piston and Crankshaft...
Page 106: ...4 51...
Page 111: ...5 2 1 1 1 1 Wire Routing Wire Routing Wire Routing Wire Routing...
Page 112: ...5 3...
Page 113: ...5 4...
Page 114: ...5 5...
Page 115: ...5 6...
Page 116: ...5 7 Wiring Diagram 40B 50B EPTO...
Page 117: ...5 8...
Page 118: ...5 9...
Page 119: ...5 10...
Page 120: ...5 11...
Page 121: ...5 12...
Page 126: ...5 17 Note Slash shows stripe color of cable 2 2 2 2 Assembly Assembly Assembly Assembly...
Page 127: ...5 18 Wiring around solenoid Bracket...
Page 128: ...5 19...
Page 129: ...5 20...
Page 130: ...5 21...
Page 136: ...5 27 Kill Switch Crank Sensor Oil Level Sensor Grounds Air Injector 1...
Page 137: ...5 28 Air Injector 2 Air Injector 3 Coil 1 Coil 2 Coil 3...
Page 138: ...5 29 Fuel Pump Fuse Box Regulator Stator Complete Wiring harness...
Page 140: ...6 2 1 1 1 1 Configuration Configuration Configuration Configuration GEARCASE DRIVESHAFT...
Page 141: ...6 3 GEARCASE PROPELLERSHAFT...
Page 152: ...6 14...
Page 153: ...6 15...
Page 185: ...10 20...
Page 193: ...11 8...