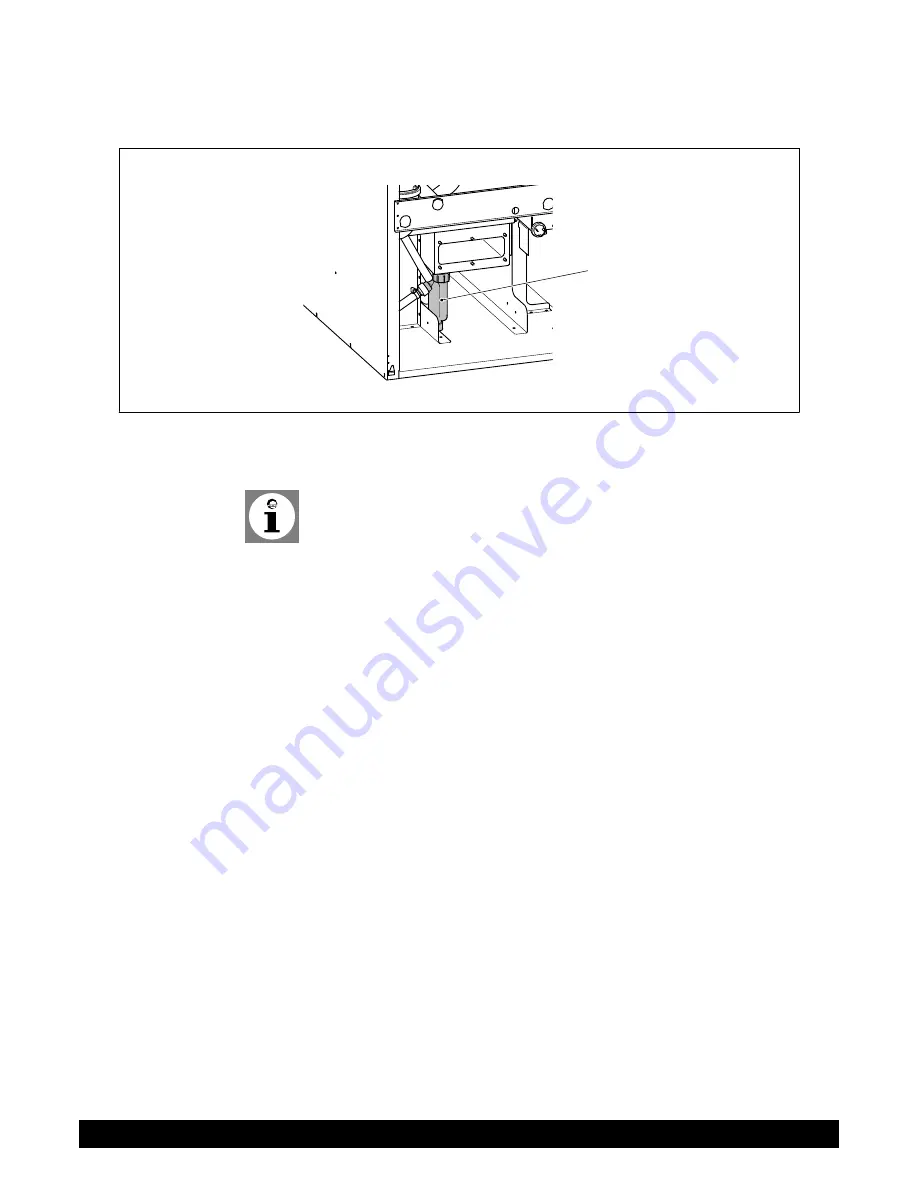
Fig. 42: Siphon
4
C0004620
5. Remove siphon (4) and clean
6. Clean siphon
7. Reinstall siphon
8. Replace the cover of the exhaust collection pan
Note: Use a new seal when installing the cover.
9. Reinstall burner (see section
Installing and removing burner
)
Maintenance
138
Condensing gas boiler Eurocondense three125-300 kW
7308536-02 06.13