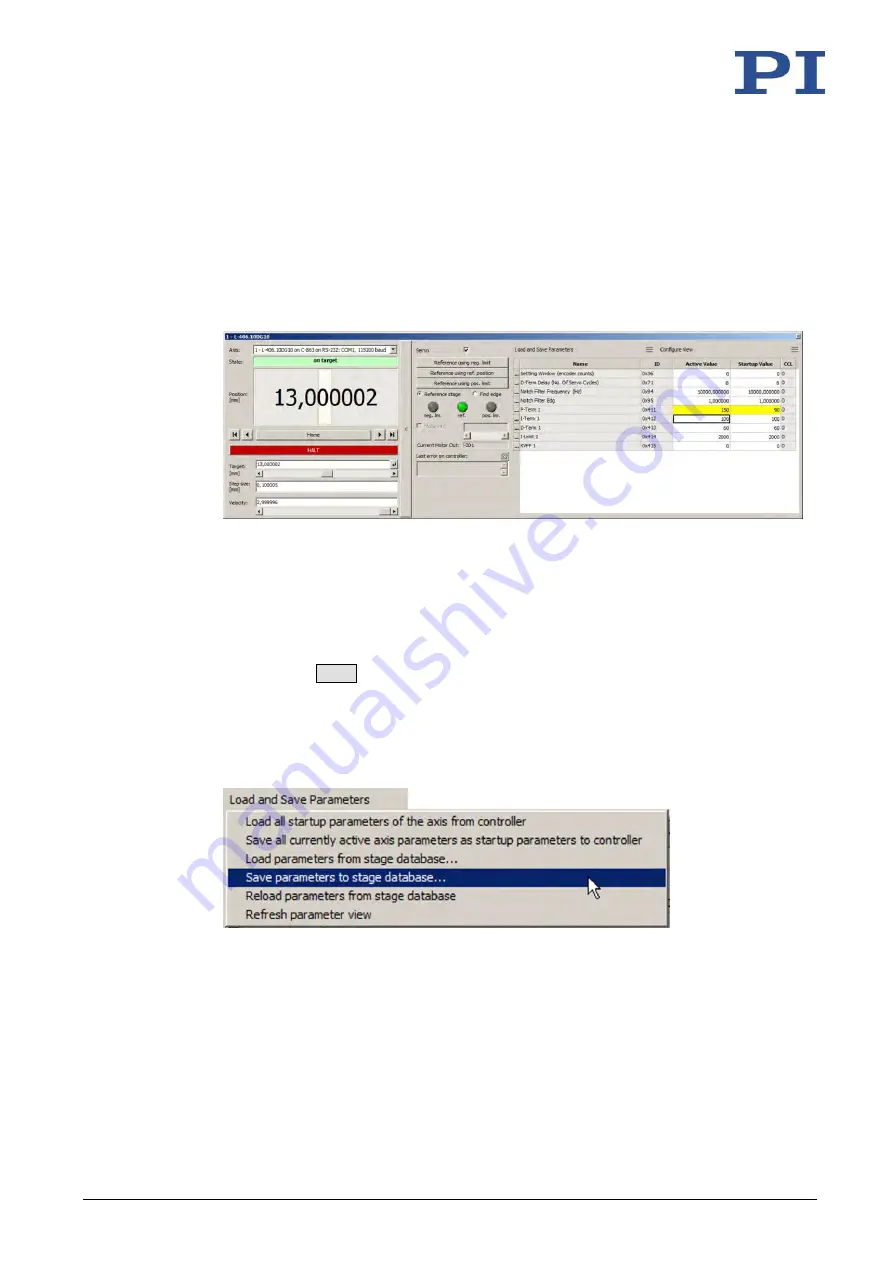
9 Adapting Settings
238
Version: 1.2.1
MS249E
C-863.12 Mercury Controller
3.
Click
Keep the changes temporarily
in the
Save all changes permanently
dialog to load
the parameter settings into the volatile memory of the C-863.12.
The
Start up stages/axes
window changes to the
Start up axes
step.
4.
Click
Close
in the
Start up axes
step to close the
Start up stages/axes
window.
5.
Open the expanded single axis window for the selected positioner in the main window
of PIMikroMove by clicking the right mouse button on the corresponding line of the
Axes
tab and selecting
Show Expanded Single Axis Window
in the context menu.
6.
Enter new values for the parameters to be changed:
a)
If the parameter to be modified is not included in the list on the right-hand side of
the window, click
Configure view > Select parameters...
and add it to the list. You
can also display certain groups of parameters or all axes-related parameters.
b)
Type the new parameter value into the corresponding input field in the
Active
Value
column of the list.
c)
Press the
Enter
key on the PC keyboard or click outside the input field with the
mouse to transfer the parameter value to the volatile memory of the controller.
Note: If a parameter value in the volatile memory (
Active Value
column) is different
to the parameter value in the nonvolatile memory (
Startup Value
column), the line
in the list is highlighted in color.
7.
Click
Load and Save Parameters -> Save parameters to stage database...
.
The
Save Parameters as User Stage Type
dialog opens.
8.
Save the changed parameter values as new positioner type in the
Save Parameters as
User Stage Type
dialog:
a)
Leave the entry in the
Parameters of axis
field unchanged.
b)
Enter the name for the new positioner type into the
Save as
field.
c)
Click
OK
.