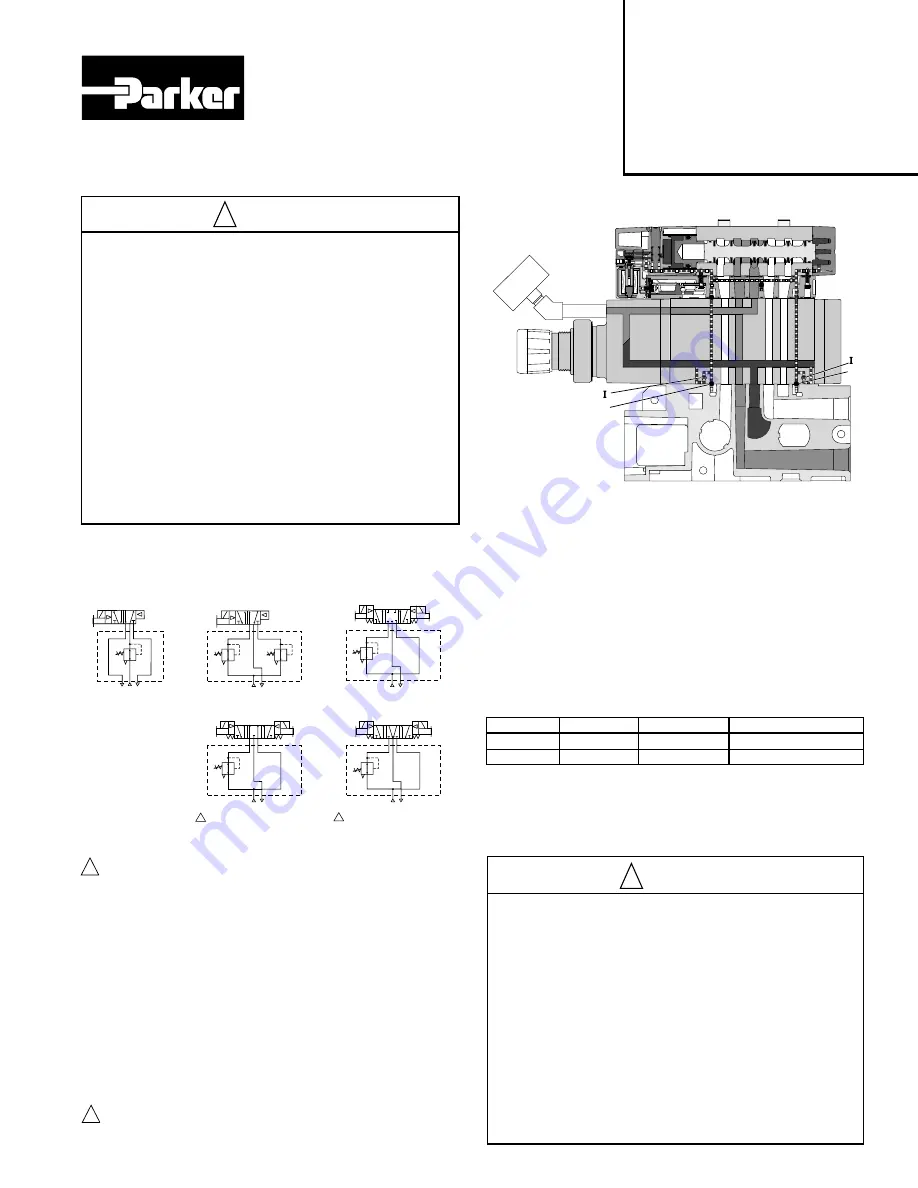
Pneumatic Division
Richland, Michigan 49083
Pneumatic
!
!
WARNING
To avoid unpredictable system behavior that can cause personal
injury and property damage:
• Disconnect electrical supply (when necessary) before installation,
servicing, or conversion.
• Disconnect air supply and depressurize all air lines connected to
this product before installation, servicing, or conversion.
• Operate within the manufacturer’s specified pressure, temperature,
and other conditions listed in these instructions.
• Medium must be moisture-free if ambient temperature is below
freezing.
• Service according to procedures listed in these instructions.
• Installation, service, and conversion of these products must be
performed by knowledgeable personnel who understand how
pneumatic products are to be applied.
• After installation, servicing, or conversion, air and electrical
supplies (when necessary) should be connected and the product
tested for proper function and leakage. If audible leakage is present,
or the product does not operate properly, do not put into use.
• Warnings and specifications on the product should not be covered
by paint, etc. If masking is not possible, contact your local
representative for replacement labels.
WARNING
FAILURE OR IMPROPER SELECTION OR IMPROPER USE OF
THE PRODUCTS AND/OR SYSTEMS DESCRIBED HEREIN OR
RELATED ITEMS CAN CAUSE DEATH, PERSONAL INJURY AND
PROPERTY DAMAGE.
This document and other information from Parker Hannifin Corporation,
its subsidiaries and authorized distributors provide product and/or
system options for further investigation by users having technical
expertise. It is important that you analyze all aspects of your application,
including consequences of any failure and review the information
concerning the product or systems in the current product catalog. Due
to the variety of operating conditions and applications for these products
or systems, the user, through its own analysis and testing, is solely
responsible for making the final selection of the products and systems
and assuring that all performance, safety and warning requirements
of the application are met.
The products described herein, including without limitation, product
features, specifications, designs, availability and pricing, are subject
to change by Parker Hannifin Corporation and its subsidiaries at any
time without notice.
Introduction
Follow these instructions when installing, operating, or servicing the product.
NOTE:
The Independent Regulators shown are with regulators on the 14 end.
Regulators may also be on the 12 end, or both the 12 and 14 end.
CAUTION: The reverse valve porting utilized with Independent Port
will reverse the function of 4-Way, 3-Position cylinder to exhaust
and 4-Way, 3-Position inlet to cylinder to valves. Utilize opposite
function valve for normal operation.
Application Limits
These products are intended for use in general purpose compressed air
systems only.
Operating Pressure Range:
Maximum 145 PSIG (1000 kPa)
Ambient Temperature Range:
-15°C to 49°C (5°F to 120°F)
Installation & Service Instructions
V-447P
F6 / H2B, F7 / H3B
Sandwich Regulators
ISSUED: December, 2001
Supersedes: None
ECN# P28681 Rev. 1
Common Port Regulator with
4-Way, 2-Position Valve
4
2
3
1
5
14
4
2
14
Independent Dual Port Regulator with
4-Way, 2-Position Valve
3
1
5
3
1
5
Independent Port Regulator with
4-Way, 3-Position All Ports Blocked Valve
14
12
4 2
3
1
5
14
12
4
2
Independent Port Regulator with 4-Way,
3-Position, Inlet to Cylinder Function
! CAUTION: Requires 4-Way, 3-Position,
Cylinder to Exhaust Valve
3
1
5
14
12
4
2
Independent Port Regulator with 4-Way,
3-Position, Cylinder to Exhaust Function
! CAUTION: Requires 4-Way, 3-Position,
Inlet to Cylinder Valve
F6 / H2B, F7 / H3B Sandwich Regulator
!
Lubrication
Factory pre-lubed. If lubricating in service, use Parker F442 oil or equivalent
paraffin based mineral oil with 150 to 200 SSU viscosity @100°F.
CAUTION: Do not use oils that are synthetic, reconstituted, have
an alcohol content or a detergent additive.
Installation
Remove pressure and electrical connections before installation.
1.
After removing Valve from Base, install three (F6, F7) or four
(H2B, H3B) Mounting Studs (26) from Regulator Kit to the Base, torque
finger tight.
2.
F6 / H2B Common & Independent Port Versions
– Place Interface
Block Track Seal (29) into Interface Block Assembly (22).
F7 / H3B All Versions & F6 / H2B Selector Regulator Version
- Place
the Gasket (29) over the Studs and on the Base.
3.
Install Regulator over Studs. Carefully engage the Electrical Plug
(F6 / H2B 5599-2, F7 / H3B 5599-2).
4.
Install Valve onto Regulator. Carefully engage the Electrical Plug
(F6 / H2B 5599-2, F7 / H3B 5599-2).
5.
Tighten Valve Bolts (20) as follows:
Valve Type
No. of Bolts
Wrench Size
Torque Nm (In.-Lb.)
F6 / H2B
3 / 4
M5
13 to 15 (115 to 130)
F7 / H3B
3 / 4
M6
14 to 16 (120 to 140)
6.
Apply main pressure and check for leaks – repeat assembly if leaks are
present.
NOTE:
If both a sandwich flow control and sandwich regulator are to be
installed, the flow control should be installed between the regulator
and the base. Both sets of studs should be installed to base before
installing the flow control.
BP
BP
1
14
12
5
1
3
2
4
14
12
E
E
!