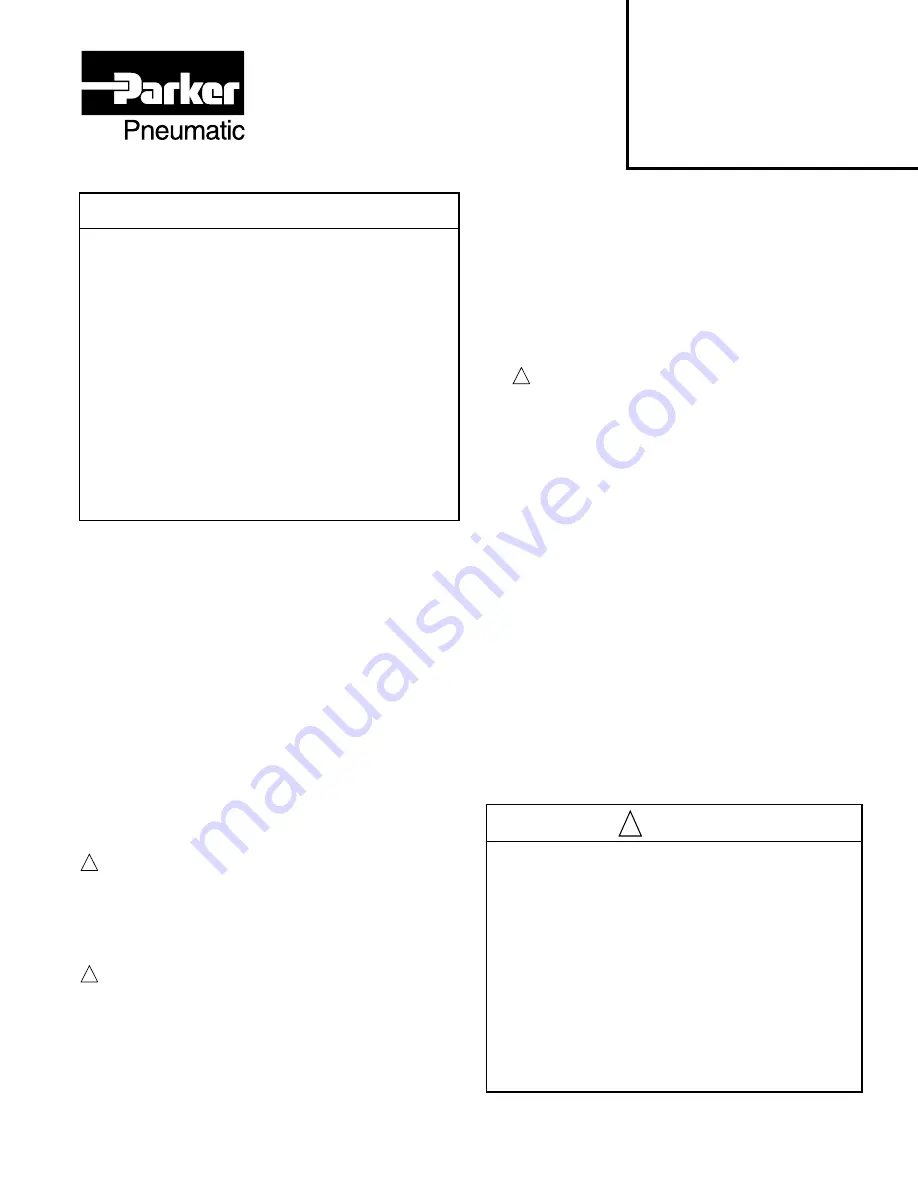
Pneumatic Division North America
Richland, Michigan 49083
Installation & Service Instructions:
V-486BP
H3 & F7 Sandwich Regulator
ISSUED: December, 2000
Supersedes: July, 1999
Rev. 4, ECN# 9319
Introduction
Follow these instructions when installing, operating, or servicing the product.
Application Limits:
These products are intended for use in general purpose compressed
air systems only.
Operating Inlet Pressure:
kPa
psig
bar
Maximum 1034 150 10.4
Ambient Temperature Range: 0°C to 52°C (32°F to 125°F)
Voltage Range: +10% to -15% of rating
(Applicable only for solenoid operated valves)
NOTE: Some of the above ratings are those of the associated valve.
Lubrication
Factory Pre-lubed. If lubricating in service, use Parker F442 oil or equivalent
paraffin based mineral oil with 150 to 200 SSU viscosity @100°F.
!
CAUTION: Do not use oils that are synthetic, reconstituted,
have an alcohol content or a detergent additive.
Wiring Instructions
Sandwich Regulators for electrically operated valves include a bridge
plug which directly connects the valve electrical plug with the subbase
or manifold plug.
!
CAUTION: An interruption of 10 milliseconds or greater to
the power supplied to the solenoid of a solenoid operated
valve may cause the valve to shift. Provision must be made
to prevent power interruption of this duration to avoid
unintended, potentially hazardous, consequences.
NOTE: Follow all requirements for local and national electrical codes.
Installation & Operating Instructions:
A sandwich regulator is used to provide regulated pressure to individual
valves in a manifolded valve arrangement. Three basic modes of
regulation are available as follows:
Common Port Regulation - Provides adjustable regulated air
pressure to the valve inlet.
Independent Port Regulation - Provides (2) separately adjustable
regulated air pressures to the outlet ports, one through each of
the valves exhaust passages. The valves exhaust (coming out of
its inlet passage) is directed to manifold or subbase exhaust port
“3”.
Single Port Regulation - Provides adjustable regulated air
pressure to one outlet port through the corresponding valve
exhaust passage and full inlet pressure to the other. The valves
exhaust (coming out of its inlet passage) is directed to manifold
or subbase exhaust port “3”.
!
CAUTION: With Independent Port and Single Port
Regulation the valves’ flow functions are reversed as
indicated by the diagrams on page 2 of these
instructions. Wiring and plumbing must be adjusted
accordingly. Common Port Regulation does not affect
the valves function.
Sandwich regulator should be installed with reasonable accessibility
for service whenever possible – repair service kits are available. Keep
pipe or tubing lengths to a minimum with inside clean and free of dirt
and chips. Pipe joint compound should be used sparingly and applied
only to the male pipe — never into the female port. Do not use PTFE
tape to seal pipe joints – pieces have a tendency to break off and
lodge inside the unit, possibly causing malfunction.
Air applied to the sandwich regulator must be filtered to realize
maximum component life.
If used in conjunction with an H3 or F7 Sandwich Flow Control,
assemble between the valve and the Sandwich Flow Control.
H3 or F7 Valves: H3 or F7 Flow Control “Sandwiches” are only
recommended for use with Common Port versions of Sandwich
Regulators. If used with Single Port or Independent Port versions of
Sandwich Regulators, functionality is limited as follows:
Flow Control “Sandwich” used in conjunction with Single or Independent
Port versions of Sandwich Regulator - Adjust speed with the adjusting
screw labeled “3”. It adjusts the speed of exhaust flow from cylinder
ports “2” and “4”. Independent speed adjustment is not possible. This
could result in different exhaust speeds for cylinder ports “2” and “4”
since line pressure is supplied to one cylinder port and a regulated
pressure is supplied to the other. The other adjusting screw is non-
functional.
!
WARNING
FAILURE OR IMPROPER SELECTION OR IMPROPER USE OF
THE PRODUCTS AND/OR SYSTEMS DESCRIBED HEREIN OR
RELATED ITEMS CAN CAUSE DEATH, PERSONAL INJURY AND
PROPERTY DAMAGE.
This document and other information from Parker Hannifin Corporation,
its subsidiaries and authorized distributors provide product and/or
system options for further investigation by users having technical
expertise. It is important that you analyze all aspects of your application,
including consequences of any failure and review the information
concerning the product or systems in the current product catalog. Due
to the variety of operating conditions and applications for these products
or systems, the user, through its own analysis and testing, is solely
responsible for making the final selection of the products and systems
and assuring that all performance, safety and warning requirements
of the application are met.
The products described herein, including without limitation, product
features, specifications, designs, availability and pricing, are subject
to change by Parker Hannifin Corporation and its subsidiaries at any
time without notice.
EXTRA COPIES OF THESE INSTRUCTIONS ARE AVAILABLE FOR
INCLUSION IN EQUIPMENT / MAINTENANCE MANUALS THAT UTILIZE
THESE PRODUCTS. CONTACT YOUR LOCAL REPRESENTATIVE.
WARNING
To avoid unpredictable system behavior that can cause personal injury
and property damage:
•
Disconnect electrical supply (when necessary) before installation,
servicing, or conversion.
•
Disconnect air supply and depressurize all air lines connected to
this product before installation, servicing, or conversion.
•
Operate within the manufacturer’s specified pressure, temperature,
and other conditions listed in these instructions.
•
Medium must be moisture-free if ambient temperature is below
freezing.
•
Service according to procedures listed in these instructions.
•
Installation, service, and conversion of these products must be
performed by knowledgeable personnel who understand how
pneumatic products are to be applied.
•
After installation, servicing, or conversion, air and electrical
supplies (when necessary) should be connected and the product
tested for proper function and leakage. If audible leakage is present,
or the product does not operate properly, do not put into use.
•
Warnings and specifications on the product should not be covered
by paint, etc. If masking is not possible, contact your local
representative for replacement labels.