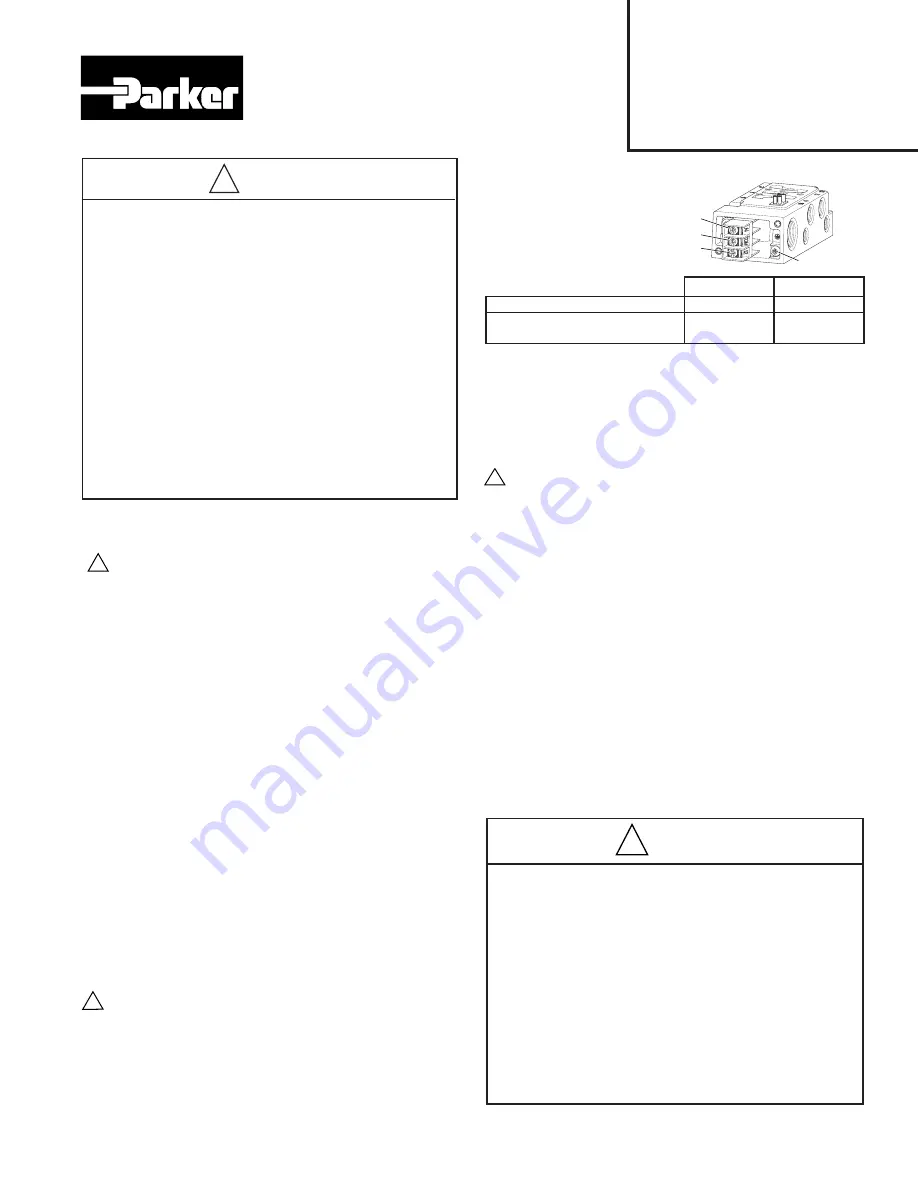
12 TERMINAL
GROUND
COM TERMINAL
14 TERMINAL
3. An external ground connection must be attached to the green
ground screw.
4. Disregard unused wires or terminals.
Connections
14 Solenoid
12 Solenoid
Valves with Wires
Black Wires
Red Wires
Valves with Terminal Block
14 and Com
12 and Com
(Will accept 18 to 24 Gauge Wires)
Terminals
Terminals
Servicing Valve Body
R
efer to figures to aid with disassembly and reassembly. Servicing a
3-position valve is very similar to servicing a 2-position valve.
1. Using a clean, lint free cloth, clean the valve unit prior to servicing.
2. Using a 2mm hex wrench for button head or 3mm hex wrench for
socket head, back out the three captive mounting screws (item #21)
until the valve unit can be removed from the base.
!
CAUTION: Do not remove the valve body from the sandwich block.
Doing so could risk possible seal contamination. There are no
parts between the valve body and sandwich block that require
servicing.
3. On solenoid valves, loosen the two captive mounting screws
(item #11) and then remove the solenoid coil (item #9) and sandwich
adapter (item #13) as a unit from the operator adapter (item #15).
4. To remove the operator adapter from the valve body, remove its two
mounting screws (item #14). You will now be able to service the piston’s
seal, as well as the gasket which is located between the operator
adapter and the valve body.
5. On air operated and single solenoid valves, loosen the two screws
(item #25) until their end cap(s) can be removed from the valve body
(item #22).
6. Gently press on one end of the spool assembly until it slides out of its
bore, taking care not to scratch bore. Using a clean, lint free cloth,
clean the body bore and all sealing surfaces for gaskets prior to their
installation.
NOTE: If more aggressive cleaning is required, use mineral spirits or
equivalent solvent and dry thoroughly.
Inspect bore for nicks, scratches, or surface imperfections. If present,
reduced service life is probable and future replacement should be
planned.
Installation and Service
Instructions: V-411DP
F3 Series Valves - Valve Body Service
2 & 3-Position, 4-Way, 5-Ports
ISSUED: October, 1999
Supersedes: March, 1999
ECN# P27372
Introduction
Follow these instructions when installing, operating, or servicing the product.
CAUTION: Solenoid versions of this valve contain solid state
components that can be damaged by transient voltage spikes,
over-voltage or high temperature. To protect against premature
solenoid failure, please read and adhere to the following:
1.
If this solenoid operated valve is used in a circuit with other inductive
loads. The solenoid should be electrically protected with a voltage
suppression device (e.g. transient voltage suppressor or varistor) that
has a minimum rating of 1.6 times the rated voltage of the solenoid valve
and sufficient capacity to dissipate the energy of other inductive loads.
2.
Operating voltage is 85-110% of rated voltage. These limits should not
be exceeded.
Application Limits
These products are intended for use in general purpose compressed air
systems only. Compliance with the rated pressure, temperature, and voltage
is necessary - see Installation & Operating Instructions (V-410CP) packed
with valve.
Operating Pressure Range:
kPa
PSIG
bar
Min. (2-Position - Air Return)
140
20
1.4
Min. (2-Position w/Spring
and Air Return)
240
35
2.4
Min. (3-Position)
210
30
2.1
Max. (2 & 3-Position)
1030
150
10.3
NOTE: Solenoid operated valves, when specified with external pilot, may
have operating pressures down to vacuum in the main valve.
External pilot pressure and air pilot signals must be greater than
or equal to that in the main valve, but not outside the ratings
above.
Ambient Temperature Range: -15°C to 49°C (5°F to 120°F)
Voltage Range: Rated V10%, -15%
CAUTION: An interruption of 10 milliseconds or greater to the
power supplied to the solenoid of a solenoid operated valve may
cause the valve to shift. Provision must be made to prevent power
interruption of this duration to avoid unintended, potentially
hazardous, consequences.
Wiring Instructions
1. Follow all requirements for local and national electrical codes.
2. Remove end cover from base by backing off the two captive screws.
Reassemble cover to base by tightening screws from 0.8 to 1.0 Nm
(7 to 9 in-lbs).
Pneumatic Division North America
Richland, Michigan 49083
Pneumatic
!
WARNING
FAILURE OR IMPROPER SELECTION OR IMPROPER USE OF THE
PRODUCTS AND/OR SYSTEMS DESCRIBED HEREIN OR RELATED
ITEMS CAN CAUSE DEATH, PERSONAL INJURY AND PROPERTY
DAMAGE.
This document and other information from Parker Hannifin Corporation,
its subsidiaries and authorized distributors provide product and/or system
options for further investigation by users having technical expertise. It is
important that you analyze all aspects of your application, including
consequences of any failure and review the information concerning the
product or systems in the current product catalog. Due to the variety of
operating conditions and applications for these products or systems, the
user, through its own analysis and testing, is solely responsible for making
the final selection of the products and systems and assuring that all
performance, safety and warning requirements of the application are met.
The products described herein, including without limitation, product
features, specifications, designs, availability and pricing, are subject to
change by Parker Hannifin Corporation and its subsidiaries at any time
without notice.
EXTRA COPIES OF THESE INSTRUCTIONS ARE AVAILABLE FOR
INCLUSION IN EQUIPMENT / MAINTENANCE MANUALS THAT UTILIZE
THESE PRODUCTS. CONTACT YOUR LOCAL REPRESENTATIVE.
!
WARNING
To avoid unpredictable system behavior that can cause personal injury
and property damage:
•
Disconnect electrical supply (when necessary) before installation,
servicing, or conversion.
•
Disconnect air supply and depressurize all air lines connected to
this product before installation, servicing, or conversion.
•
Operate within the manufacturer’s specified pressure, temperature,
and other conditions listed in these instructions.
•
Medium must be moisture-free if ambient temperature is below
freezing.
•
Service according to procedures listed in these instructions.
•
Installation, service, and conversion of these products must be
performed by knowledgeable personnel who understand how
pneumatic products are to be applied.
•
After installation, servicing, or conversion, air and electrical supplies
(when necessary) should be connected and the product tested for
proper function and leakage. If audible leakage is present, or the
product does not operate properly, do not put into use.
•
Warnings and specifications on the product should not be covered
by paint, etc. If masking is not possible, contact your local
representative for replacement labels.
!
!