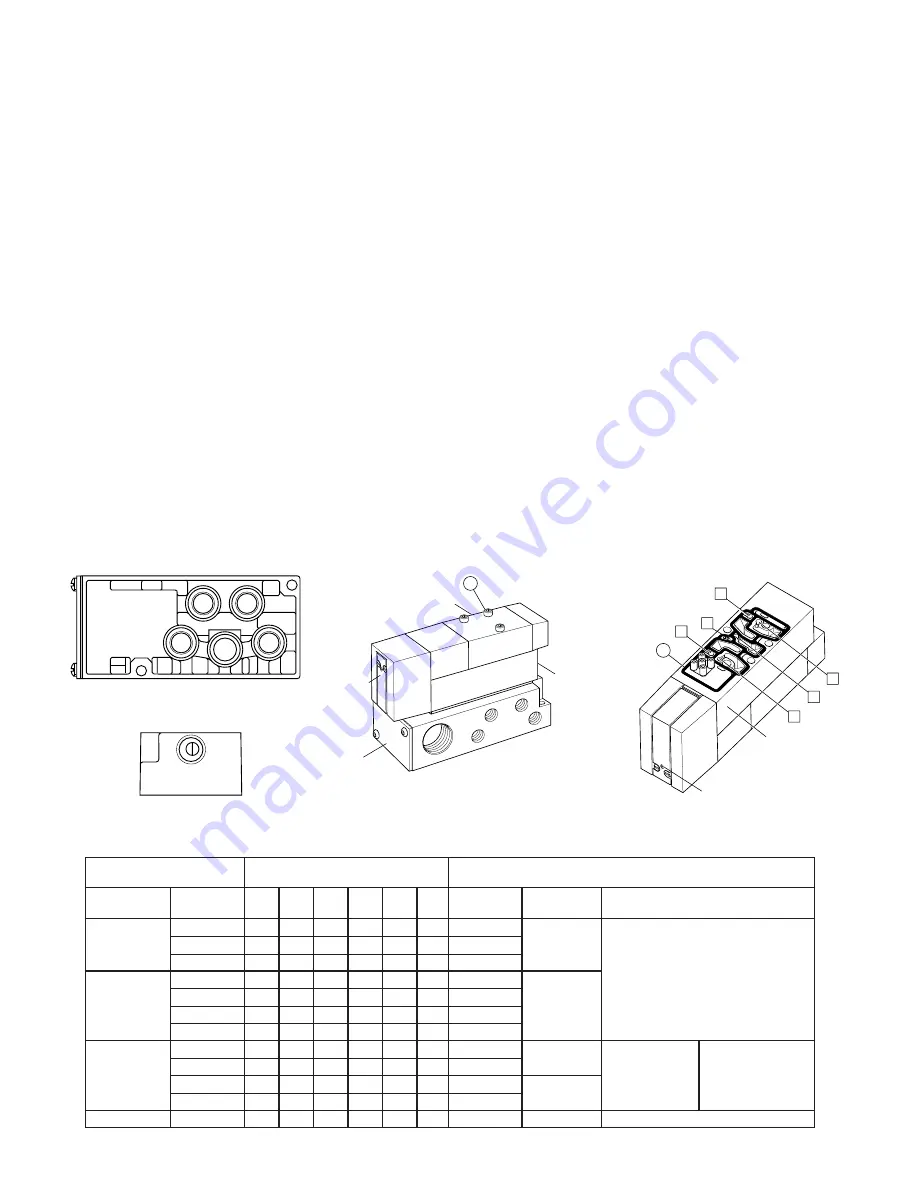
F3 Series Valves - Subbase Installation
V-414CP
4.
Line up the captive mounting screws. Tighten using a 3 mm wrench;
torque from 2.5 to 2.9 N•m (22 to 26 in-lbs) using progressive steps
with a criss-cross pattern.
5.
Apply main pressure and check for leaks. If any are present, do not
operate the valve - repeat the reassembly process until satisfactory.
Port Connections
(Below is a brief summary of typical port connections. See Technical
Data section of the F3 catalog for more details.)
1.
Connect a single inlet air supply to port #1. (For dual pressure
applications connect inlet air supplies to ports #3 and #5.)
2.
Connect mufflers (or pipe exhaust) to ports #3 and #5 for single air
supply. For dual pressure applications, connect to port #1.
3.
Connect cylinder ports marked #2 and #4 to cylinder or other device
to be supplied air.
4.
External pilot supply may be applied to ports #12 or #14. Double air
piloted valves need to use both #12 and #14 ports for remote pilot
signal; and single air piloted valves have to use port #14 for remote
pilot signal.
5.
For 2-way and 3-way functions, you will need to plug some of the
ports - consult the Technical Data section of the F3 catalog.
NOTE: Some subbase kits come with pipe plugs. These plugs should
be located as desired. The common exhaust port is common to
ports #3 and #5, side and bottom.
Instruction Sheets Available:
V-410DP - Valve Installation & Operating Instructions
V-411DP - Valve Body Service Instructions
V-412DP - Solenoid Service Instructions
V-413DP - Manifold Installation Instructions
V-415CP - Sandwich Flow Control Installation Instructions
V-416CP - Sandwich Regulator Installation & Operating Instructions
V-417CP - Sandwich Regulator Conversions & Service Instructions
V-418CP - Manifold With Electrical Interconnect Installation
Method 1: Using Model No.
Pilot Supply Holes:
Method 2: Using Attributes of Valve & Operator(s)
to Determine Plug Locations
(See key code below)
to Determine Plug Locations
3rd Digit
6th Digit
1
3
5
BP
12
14
Pilot Supply
Main Press
Control Mechanism
in Model No.
in Model No.
Supply Type
Operator Types
B or C
M
M
X
X
Int. Port 1
1 or E
P or Q
X
M
M
X
Ext. Port 12
Single
L or M
X
M
M
X
Ext. Port 14
2, 5, 6, 7
E or F
X
X
X
X
Int. Port 3
All Solenoids
H or J
X
X
X
X
Int. Port 5
Dual
P or Q
X
M
M
X
Ext. Port 12
L or M
X
M
M
X
Ext. Port 14
0 or C
M
M
X
X
Int. Port 1
Single
Air Return or
3 or F
P or Q
X
M
M
X
Ext. Port 12
Single Air Pilot
Spring/Air
E or F
X
X
X
X
Int. Port 3
Dual
on 14 End
Return on 12 End
P or Q
X
M
M
X
Ext. Port 12
4, 8, 9, 0
0
X
M
M
X
None
Single or Dual
Double Air Pilot
Key Code:
X = Pilot hole must be plugged.
M = Pilot holes may be molded shut and will not need a plug; however some holes may be open and therefore
Blank = Pilot hole must be left open.
will require a plug. Use a probe to test if holes are open - the probe must be able to pass through the thickness
of the sandwich block for the holes to be open.
Pilot Pressure Supply
This valve requires a source of air pressure for shifting - a pilot supply.
The sixth character in the model number identifies this supply when the
valve was assembled at the factory. If changes have occurred in the field,
the character will no longer represent that pilot arrangement. If a new
valve is ordered with the same model number as the old one, perform an
examination at the time of replacement and move the plugs (if necessary)
so that the new valve has them in the same locations as the old one
(described in steps 1-3 following).
Conversion in the field from an internal pilot supply to an external type, or
vice versa, is possible. However, conversion from a single pressure valve
to a dual pressure type is not possible in the field - special parts are
required. (However, dual pressure valves can be converted back to single
pressure in the field.) All of these conversions are performed by relocating
small plugs as follows:
1.
The bottom surface of the sandwich block has several holes which
receive the small plugs. This is accessed by loosening the three main
body mounting screws (item A) with a 3 mm hex wrench and removing
the valve from its base. These holes have identification alongside as
shown in Figure 5 and plugs must be located in the holes as described
in Table 1. (See the two identification methods located in Table 1.)
2.
To remove a plug, insert a narrow tool under the side of the nib and
pry it upward slightly. Then, grasp the projecting nib (long nose pliers
may help) and pull it out. Examine the o-ring to be sure it is not torn or
nicked, and that it has a coating of grease. Install the plug into the
appropriate hole (o-ring end enters first) by pushing it in place until it
comes to a stop and the nib is flush with the surface of the sandwich
block.
3.
Replace the valve on its base, making certain first that the interface
gasket (item B) is in place in its grooves in the sandwich block.
Engage the electrical plug carefully during this process. Tighten the 3
main body mounting screws from 2.5 to 2.9 N•m (22 to 26 in-lbs).
4.
Apply main pressure and check for leaks. If any are present, do not
operate the valve - repeat the reassembly process until satisfactory.
3-5
FIGURE 2: Bottom View of Subbase -
showing optional bottom ports
FIGURE 3: End View of Subbase - showing optional
common exhaust port
FIGURE 4
FIGURE 5
4
5
1
3
2
ELECTRICAL
JUNCTION BOX
SANDWICH
BLOCK
SOLENOID
VALVE
BODY
SANDWICH
BLOCK
OVERRIDE
A
B
14
5
1
3
12
BP
Table 1 - Sandwich Block Pilot Plug Locations (Reference Illustrations Above)