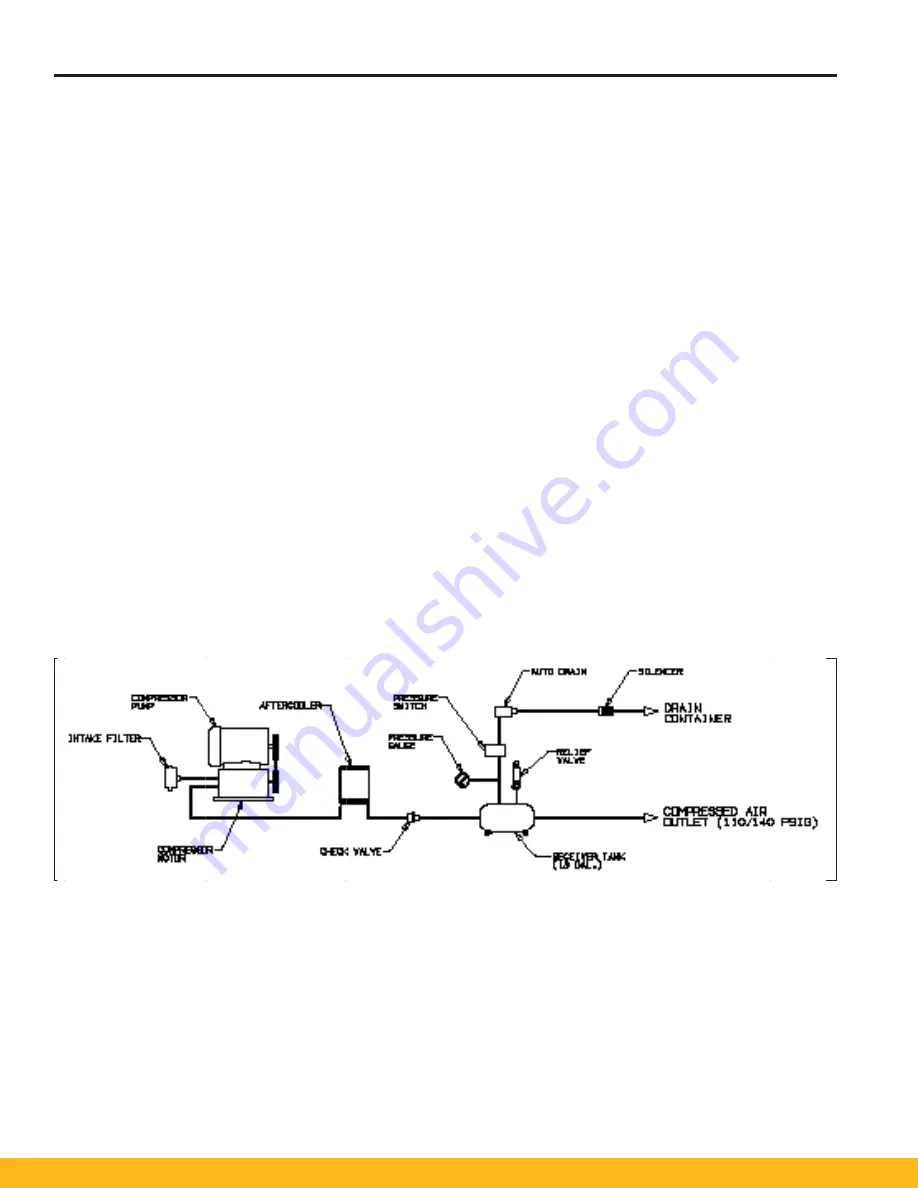
Bulletin TI-LCMS-SF5000J
Installation, Operation and Maintenance Manual
Super Flow Tri-Gas Generators
www.labgasgenerators.com
4
1-800-343-4048
The Source LC/MS Super Flow Tri-Gas 5000 Generator Series are available in three models (see
figures 1a,b,c):
(1) LCMS-SF5000, Tri-Gas Generator, Compressor and Receiver Tank (visually integrated model)
(2) LCMS-SF5001T, Tri-Gas Generator and Receiver Tank
(3) LCMS-SF5001NT, Tri-Gas Generator
The visually integrated system is engineered to produce pure nitrogen for curtain gas; zero grade
air for gas-1/gas-2 source gases; and clean, dry, -40°F dew point air for source exhaust gas from
compressed air delivered by a carefully matched scroll compressor. The system is housed in three
mobile, sheet metal cabinets: one cabinet produces the compressed air using an oil-less rotary
scroll compressor. The other two cabinets remove contaminants and separate the compressed air
into the three gases.
General Description
The generator is certified to the electrical safety requirements as specified by the IEC, UL, and
CSA standards. These units bear the CSA marking on the product. Product supplied internation-
ally also carries the CE mark. The product meets EMC compliance. Internal pressure receivers
are CRN and ASTM Certified or CE certified.
Regulatory
Compliance
The LCMS Source SF5000 contains the necessary components to produce reliable, oil-free com-
pressed air and the three gases required to operate the LC/MS instruments. The system con-
sists of six functional technologies: (1) compressed air, (2) liquid water removal (3) prefiltration
(4) oxygen/carbon dioxide/water vapor removal, (5) hydrocarbon removal and (6) final filtration.
The compressed air schematic (figure 2) shows the air flow through the intake filter, compressor
pump, aftercooler, receiver tank, and check valve. The gas separation schematic (figures 3 and
4) shows the compressed air flow through the receiver tank and prefiltration where additional wa
-
ter (liquid and vapor) is removed. After filtration, the compressed air flow passes through an acti
-
vated carbon prefilter, nitrogen membrane, post carbon filters, pressure regulator, and flow meter,
providing the nitrogen curtain gas. The second flow passes through a dryer membrane, then
further divides into two paths. One path goes to a pressure regulator, flow meter as dry air or the
source exhaust gas. The second path flows into the hydrocarbon removal module, an aftercooler,
filter, pressure regulator, flow meter resulting in zero air gas or gas 1/gas 2 as output. To protect
from environmental contaminants, all three gas lines pass through final activated carbon filters
before entering the instrument.
Integrated System
Figure 2: Compressor Flow Schematic LCMS-SF5000
The oil-less rotary scroll compressor is based on the theory of scroll compression. It offers high
reliability and quiet operation. The scroll set consists of two identical spirals, offset 180° with re-
spect to the other so the scrolls mesh. One scroll is orbited around the fixed scroll, trapping and
compressing gas pockets as the pockets move to the center of the fixed scroll. The compressed
gas is discharged from the pump through the center outlet.
The air cooled aftercooler on the scroll compressor is a series of cooling fins and a high output
fan. The cooling features allow the scroll compressor to operate at lower temperatures and
extend bearing, tip seal and grease life. The aftercooler cools the temperature of the discharge
air. The temperature of the discharge air is lowered, producing trapped water in the tank. The
water is then discharged through the automatic electric drain valve and collected in a disposal
container.
Compressor Pump
Compressor
After Cooler