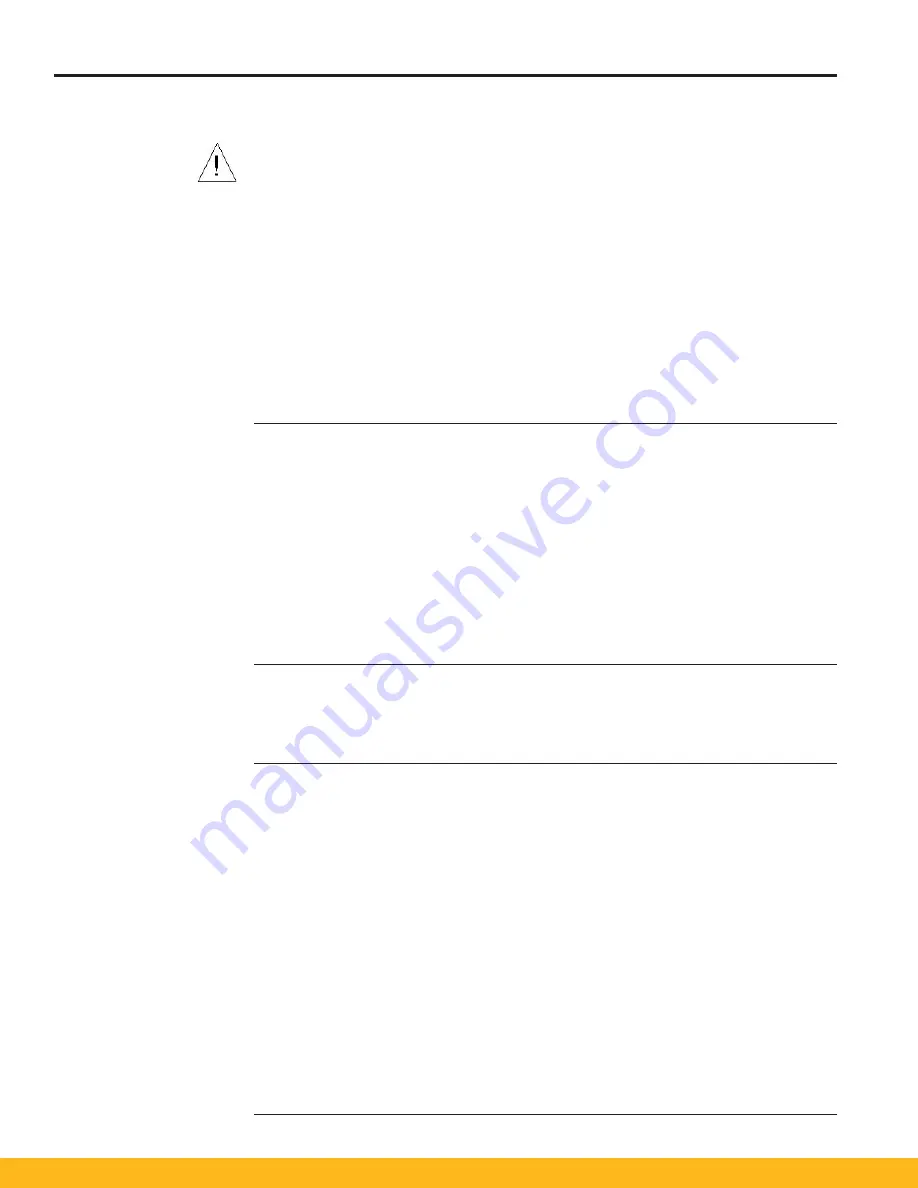
Bulletin TI-LCMS-SF5000J
Installation, Operation and Maintenance Manual
Super Flow Tri-Gas Generators
www.labgasgenerators.com
30
1-800-343-4048
Disconnect the electrical power and depressurize the generator before attempting any trouble-
shooting activities according to the shut down steps in the operation section. Only trained per-
sonnel using reasonable care should perform any troubleshooting activities.
Determine whether the trouble is with the compressed air source or the Tri-Gas Generator. First,
check that the compressed air source is delivering. If you have an integrated compressor (Model
LCMS-SF5000), refer to the compressor troubleshooting section, otherwise check that the
compressed air source is delivering a minimum, continuous flow of 180 SLPM (6.3 SCFM) at a
pressure between 110 - 140 PSIG (7.6 - 9.6 barg).
If the compressor air supply is confirmed, then go to the Tri-Gas Generator troubleshooting sec
-
tion, and begin troubleshooting the Tri-Gas Generator.
POWER ON light (green)
does not appear
• Power not plugged in sup-
ply outlet.
• Main disconnect is not ON.
• Blown fuse or tripped OFF
circuit breaker at customer
provided power supply.
• Blown fuse at primary side
of transformer.
• LED power switch has
failed.
• Plug in power cord.
• Switch disconnect to ON.
• Replace fuse or switch
disconnect to ON.
• Replace fuse on primary
side. Be sure to use the
same type and size.
• Replace switch.
Compressor Troubleshooting
Symptom
Probable Cause
Corrective Action
POWER ON light is on but
motor will not start
• Motor overload has tripped
• Wrong or low voltage
• Motor failed
• Determine fault and reset
overload (Blue button)
• Check incoming power sup-
ply and unit power rating
• Replace motor
Troubleshooting
Compressor is running but
will not make pressure
• Depressurize Valve on
TriGas Generator is OPEN
• Auto Drain Valve is open
continuously
• Drive belts broke or are too
loose
• Clogged intake filter ele
-
ment
• Pressure relief valve has
opened
• Excessive tip seal wear
• Motor running wrong
direction
• Close Valve
• Replace Auto Drain Valve
• Replace drive belts and (or)
tighten to specification
• Replace intake filter element
per instructions
• Pressure switch needs
replacing or motor contacts
welded shut
• Replace tip seals per in-
structions every 5,000 hrs
• Correct power connections