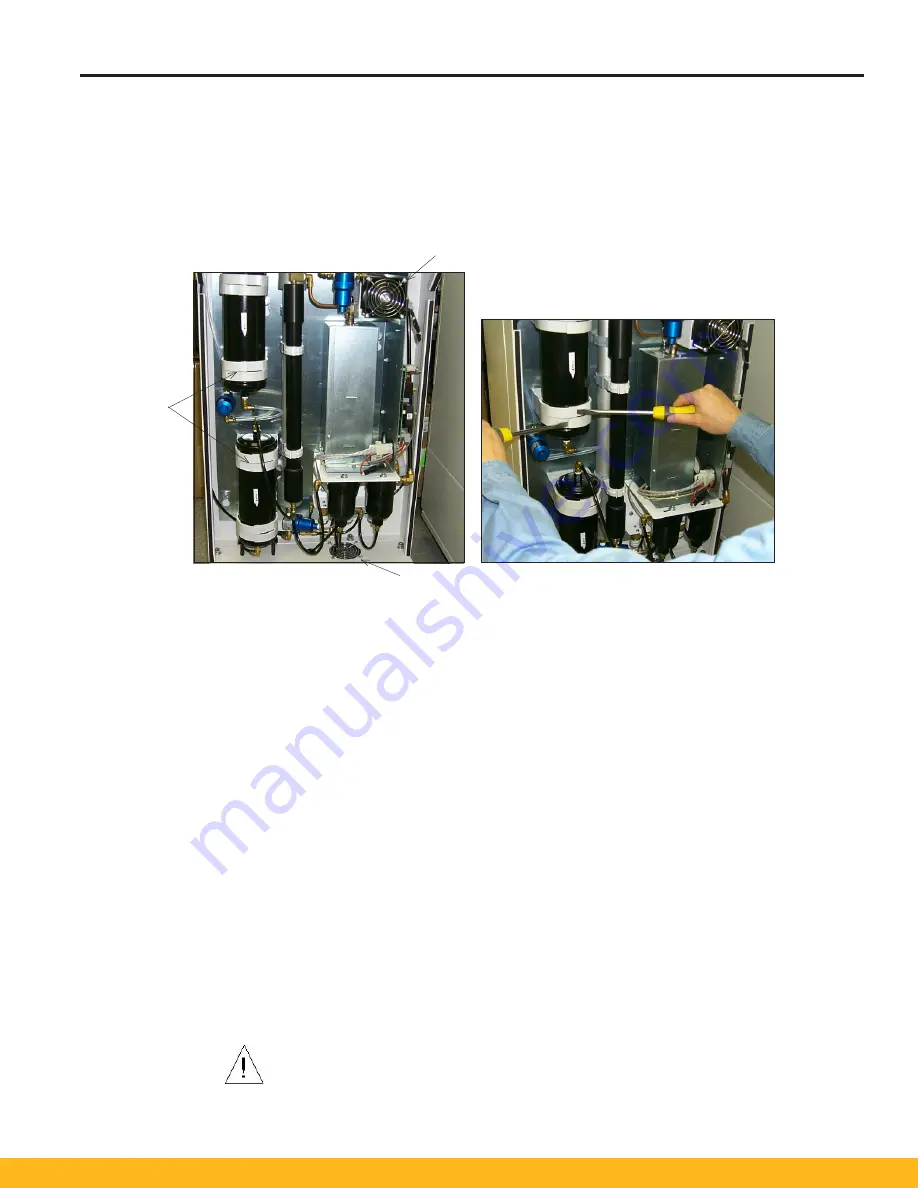
Bulletin TI-LCMS-SF5000J
Installation, Operation and Maintenance Manual
Super Flow Tri-Gas Generators
www.labgasgenerators.com
21
1-800-343-4048
In-Line Filters
There are four in-line filters requiring replacement (for model LCMS-SF5001NT three in-line
filters). The replacement element (050-05-BX) is the same for all in-line filters (see figure 24A).
By hand (or with wide-grip pliers, if necessary), rotate the bowl counter clockwise, remove and
replace the filter element with a new one, return bowl, and hand tighten (see figures 34 & 35).
There are two carbon modules that require changing. Note the flow direction arrow prior to
removing the spent modules (see figure 36).
Carbon Modules
Figure 36 Carbon Flow Arrow
Figure 37 Tri-Gas Changing In-Line Filter
1
Disconnect the plastic tubing from the press fittings on the inlet and outlet ports of the module.
To remove the tubing from the press fitting, push the tubing into the fitting, hold the collar of
the fitting back, and pull the tubing out of the fitting.
2
Release the ratcheting bands that clamp the module to the unit using two screw drivers
(see figure 37).
3
Replace with a new carbon module, with the flow arrow pointing in the proper direction (see
figure 36).
4
Push the module firmly for the ratcheting bands to clamp the module.
5
Re-insert inlet and outlet tubing. Use a soap or a leak detecting solution to check for leaks
when pressurizing (re-starting) the unit.
Inspect and clean the fan guard (see figure 36).
Inspect and clean the ventillation guard on the bottom of the cabinet (see figure 36).
Fan Guard
Ventillation Guard
FAN GUARD
CARBON
MODULES
VENTILATION
GUARD
For generators that apply to schedule 3, these instructions describe replacing the three outlet
carbon modules and three outlet filter elements.
1
Remove the back panel cover by removing two phillips head screws (see figure 38).
2
Lift back panel cover up about 1 inch and back. Put cover aside (see figure 39).
Note: Replace one carbon module at a time. Be careful tubing does not slide back into
the generator cover.
Outlet Carbon Modules