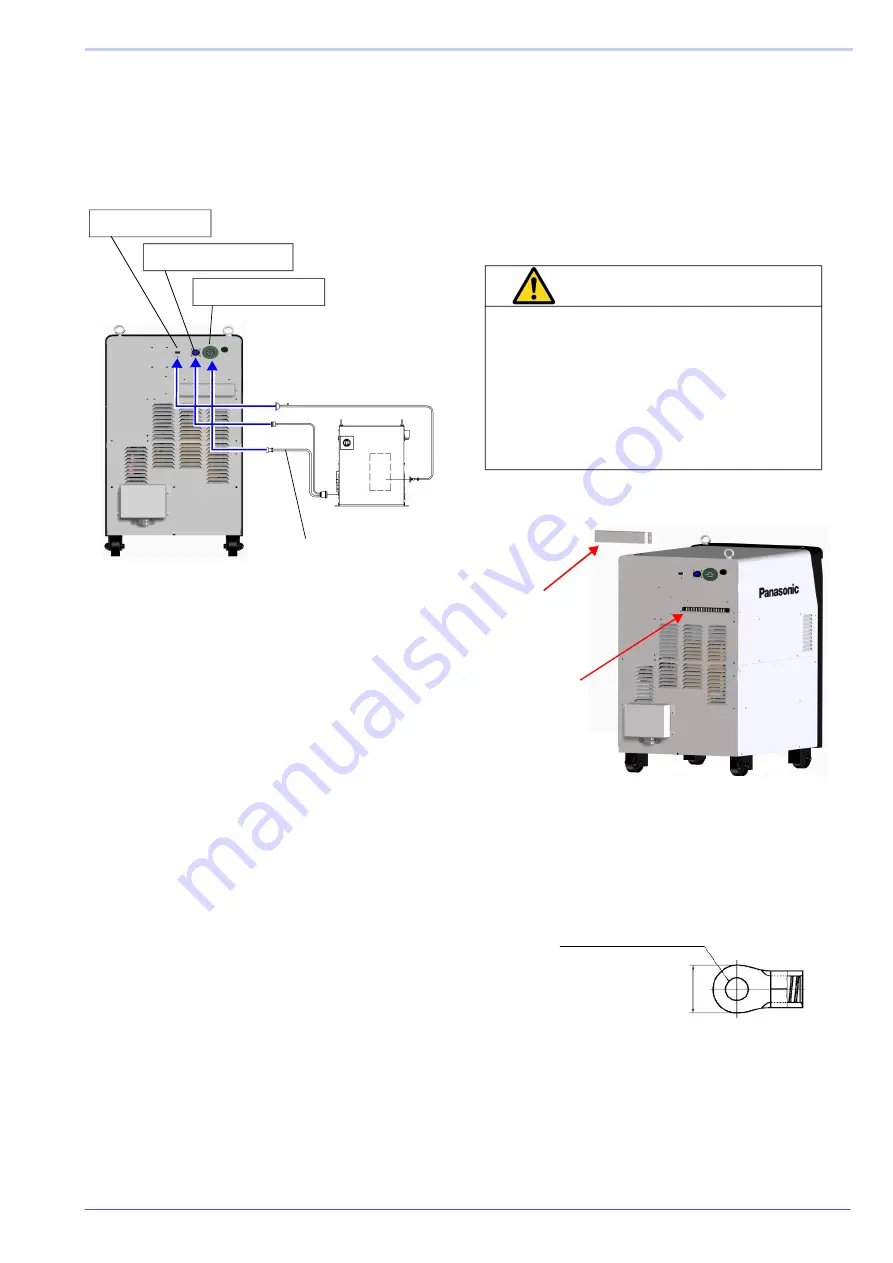
6. Connection
WMD078TE0PAA07
43
6.2.5 Connecting cables for robot con-
troller
(1) Connect control cable
Connect the control cable between the
encoder connector and the robot connector.
(2) Connect communication cable
Connect the communication cable to the D-
sub connector.
6.2.6 Communication error
In case that an error occurs while communicating
with the robot, the error codes (main and sub)
are indicated on the operation panel of the weld-
ing power source. See section “
” on page
6.3 Connecting to other devices
Use the jig terminal to apply an emergency stop
or a halt to the power source from an external
device, or to apply the current detection signal to
an external device and so on. The product pro-
vides terminals for external voltmeter and amme-
ter.
Precautions for handling jig terminals
•
Do not tighten the jig terminal screws too
tight, otherwise, the terminal block may be
damaged.
Tightening torque: 0.45 N
•
m-0.55 N
•
m
<Recommended crimp terminal>
•
Lay signal cables from other devices away
from welding torch cable, output cable and
so on to avoid any trouble caused by noise.
•
Cable should be 10 m or shorter.
D-sub connector
Encoder connector
Robot connector
<Welding power source>
<Controller>
Communication cable
Control cable
(Rear side)
WARNING
Prior to connection work, make sure to
turn off power switch to the power dis-
tribution box and confirm safety at the
working area. After the connection
work, put all panels back in place.
Do not touch any live parts. Otherwise,
it may result in electric shock or death or
serious injury.
Jig terminal cover
Jig terminals
3.2 mm to 3.3 mm (dia.)
6.2 mm or less