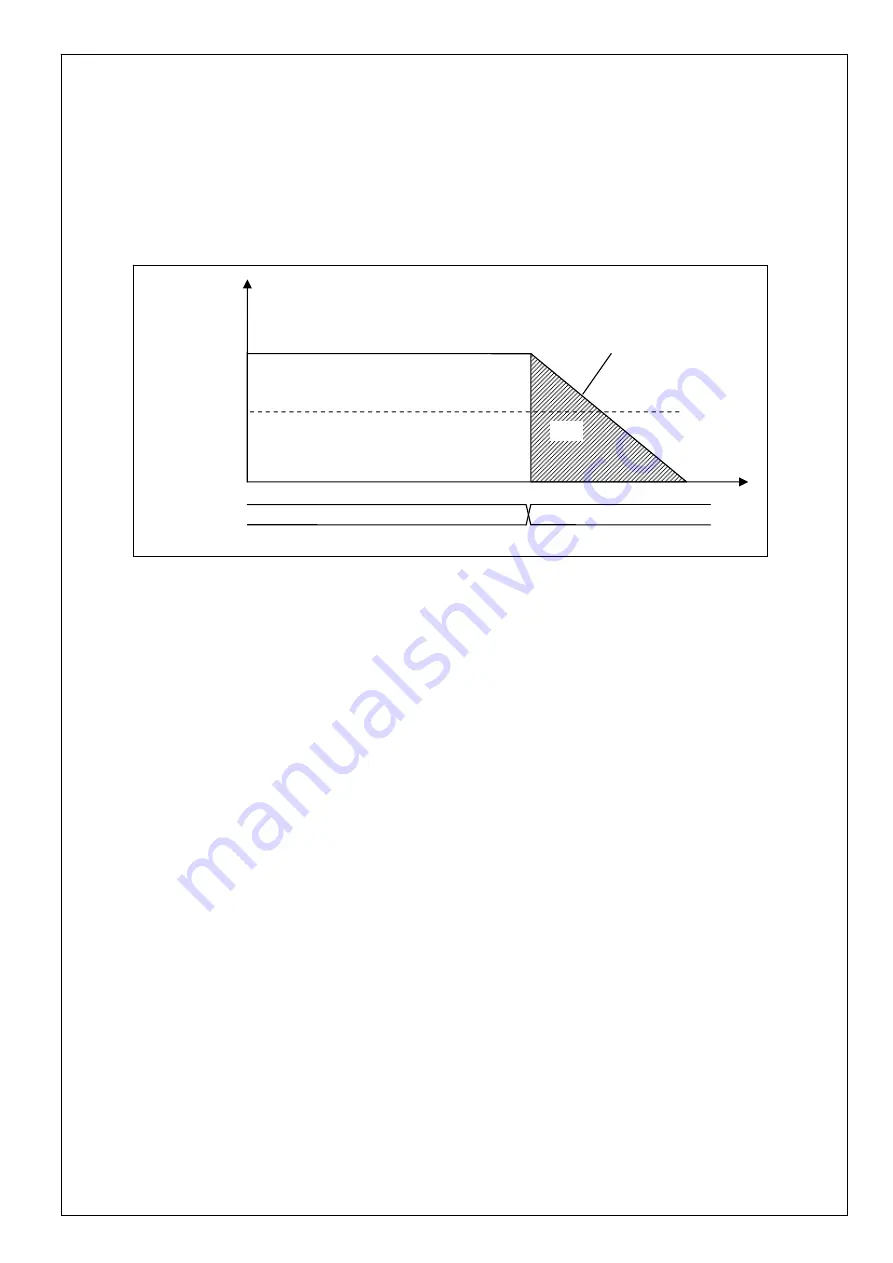
No. SX-DSV02310 - 143 -
R2.0 Motor
Business
Division,
Appliances Company, Panasonic Corporation
•
The speed (including initial speed upon changing control mode) at the start of deceleration and Pr.8.04 (Profile linear
deceleration constant) shall meet the following restriction.
<Restriction>
Amount of movement distance (P) necessary to decelerate from the initial speed to the target speed <
7FFFFFFFh (command unit)
For example, if the initial speed upon switching from the cyclic thrust control does not meet the restriction, Err.27.5
(command generation error protection) will be generated.
P
Pr.8.04 (Profile linear
deceleration constant
10000)
Initial speed upon
switching
(Feedback speed)
Speed
(Command unit/s)
Time (s)
Cyclic thrust control, etc.
Profile position control
Upper limit of
target speed