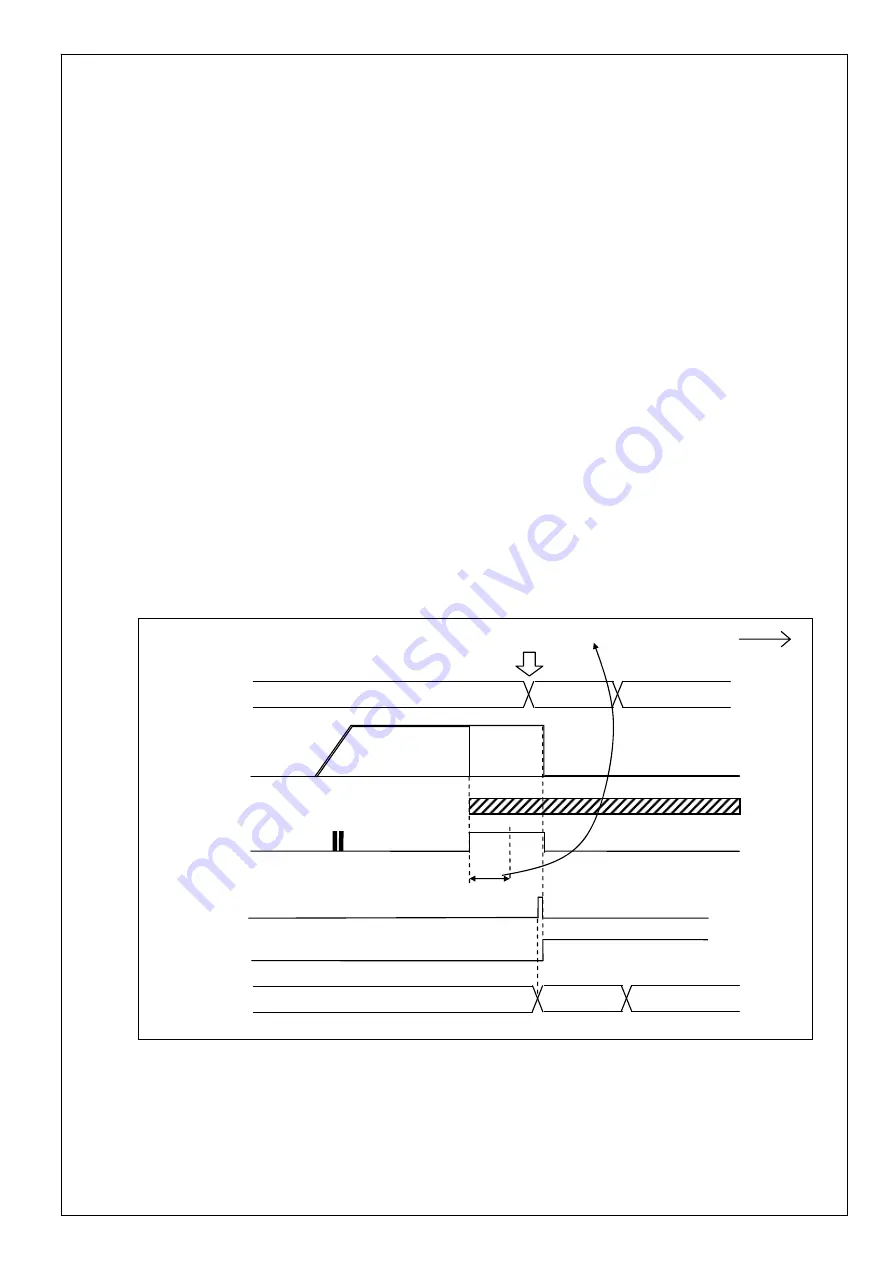
No. SX-DSV02310 - 119 -
R2.0 Motor
Business
Division,
Appliances Company, Panasonic Corporation
7-2-3-4 Example of cyclic homing operation 4
Below shows an example of return-to-home operation in the cyclic position control (CP) mode using the mechanical
stopper.
1) Lower the thrust limit value with using parameter command (26h) or TL SW bit of command.
Note: For setting the thrust limit value, see section 4-5-3.
2) Execute the positioning according to command position, which is based on the position at power-up. At this time,
lower Command Velocity for safety.
3) Actual velocity will be 0 when the slider hit the stopper, and the status will show the thrust limited (thrust limited
bit will be 1).
4) After verifying that the thrust limited status continued for specified period (t1), switch the command from
normal (20h) to return-to-home command (24h). Set Type_Code to actual position set (021h) and setting position
(Byte 12–15) to 0 (or desired value). Do not change the command position.
5) When the process of actual position set has completed in the servo driver, the driver will ignore the value of
command position and stop the motor (servo-lock) at the setup position. Then it will set homing complete bit to 1.
Note that during feedforward the value remains valid. If this causes a problem, keep feedforward value at 0
during homing process.
6) After confirming that homing complete bit has become 1, then set the command position to the set actual
position.
7) Change the command code back to normal command (20h).
Then, positioning will start according to the new reference. Therefore, be sure to perform step 6) before changing
the command code back to the normal command.
8) Bring the thrust limit value to the previous value.
*1) Command velocity is the differences of command position for the command update cycle. (It is internal
operation value of the servo driver.)
*2) Thrust limited bit may be 1 even if the slider does not hit the stopper since the thrust limit is lowered. Therefore,
adjust t1 to avoid mis-detecting.
Note that position deviation error (Err. 24.0) might occur when t1 is too large.
Command code
Actual velocity
Actual position set
Command
velocity
Torque_Limited
20h 20h
24h
*1)
*2)
Velocity
Time
t1
Homing_Complete
Busy
20h 20h
24h
Mechanical stopper
Command
code
echo