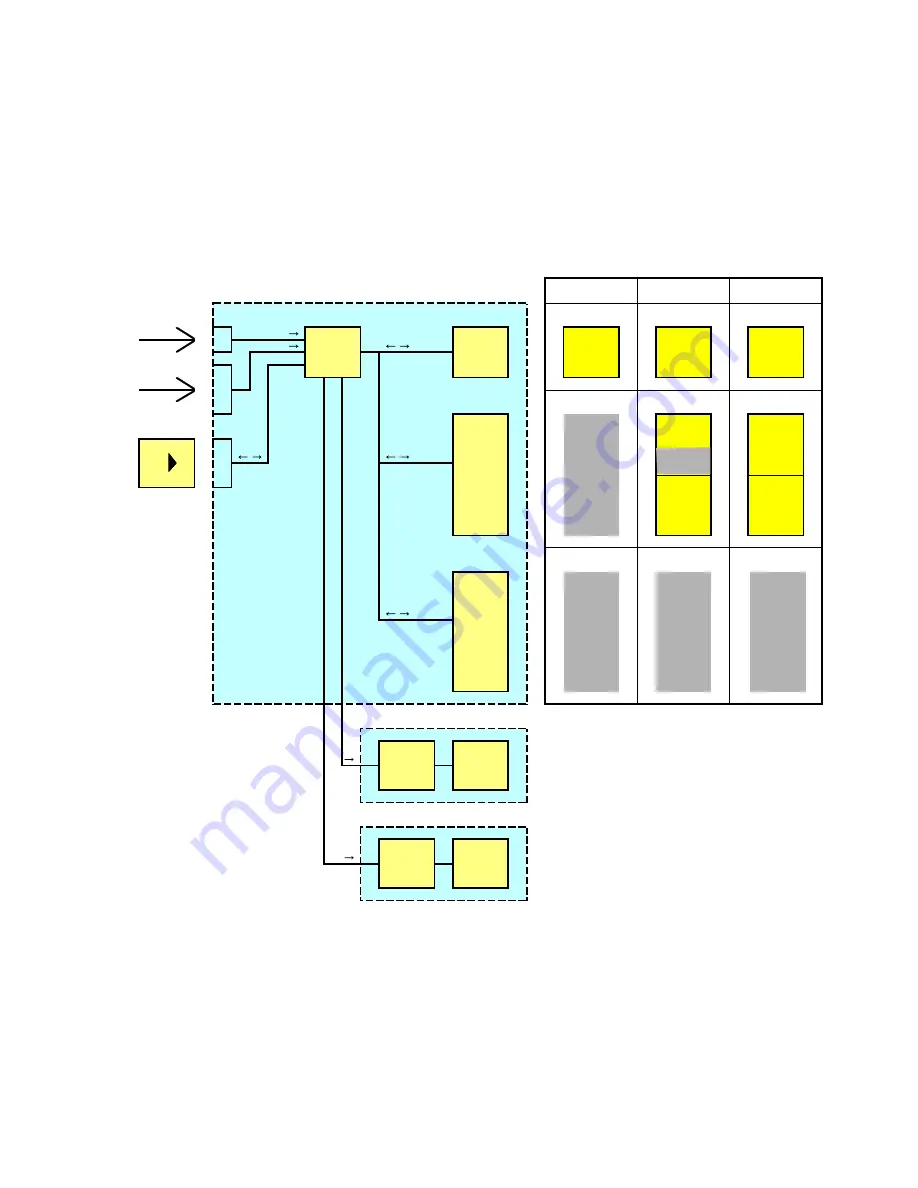
95
DP-8032/8025
2008
Ver. 1.2
3.7.
Updating the Firmware
The Quickest and Most Easiest Method of Updating the Firmware is to use the Network Firmware
Update Tool using Ethernet LAN Port and a Crossover Cable.
The Network Firmware Update Tool version must be 3.20 or higher.
3.7.1.
Firmware Configuration
A. Hardware Configuration
This machine is controlled by three (3) CPUs which are located on the System Control (SC) PC Board,
the Scanner Printer Control (SPC) PC Board and the Panel Control (PNL) PC Board.
B. SC PC Board Firmware
The 4 MB Program Memory (F-ROM) is integrated on the SC PCB. Two (2) Optional Expansion 8 MB
Program Memory (FRM8 PCB) can be installed into SLOT 1 and SLOT 2.
The Firmware to be written into the 4 MB onboard, the 8 MB of SLOT 1 / SLOT 2 depends upon the
configuration of the Standard, PCL or PS Options.
(1) Standard
The Standard Program (1) is only written into the 4 MB onboard, which is assigned as ROM
Code (A).
SC PC Board
Standard
Configuration
With PCL Option
Configuration
With PS Option
Configuration
On Board
(A)
4 MB
(B)
4 MB
(D)
4 MB
PC
(1)
(2)
(5)
CPU
4 MB
Program
Program
Program
Ethernet Port
F-ROM
PC
USB Port
Slot 1
(C) 8MB
(E) 8MB
(3)
(6)
Program
Program
8 MB
2 MB
(a)
4 MB
(a)
FRM8 PCB
(4)
(7)
Flash Memory
Card
Font
4 MB or 8 MB
4 MB
(b)
4 MB
(b)
Slot 2
8 MB
FRM8 PCB
PNL PC Board
Panel Control Program (Display & Key In)
CPU
4 MB
Bitmap Data
F-ROM
Font Data
SPC PC Board
CPU
512 KB
Scanner Control Program
F-ROM
Printer Control Program
Font
Summary of Contents for DP-8032
Page 2: ...2 ...
Page 3: ...3 ...
Page 5: ...5 Hinweis Beispiel ...
Page 9: ...9 ...
Page 10: ...10 ...
Page 11: ...11 ...
Page 12: ...12 memo ...
Page 397: ...Published in Japan ...