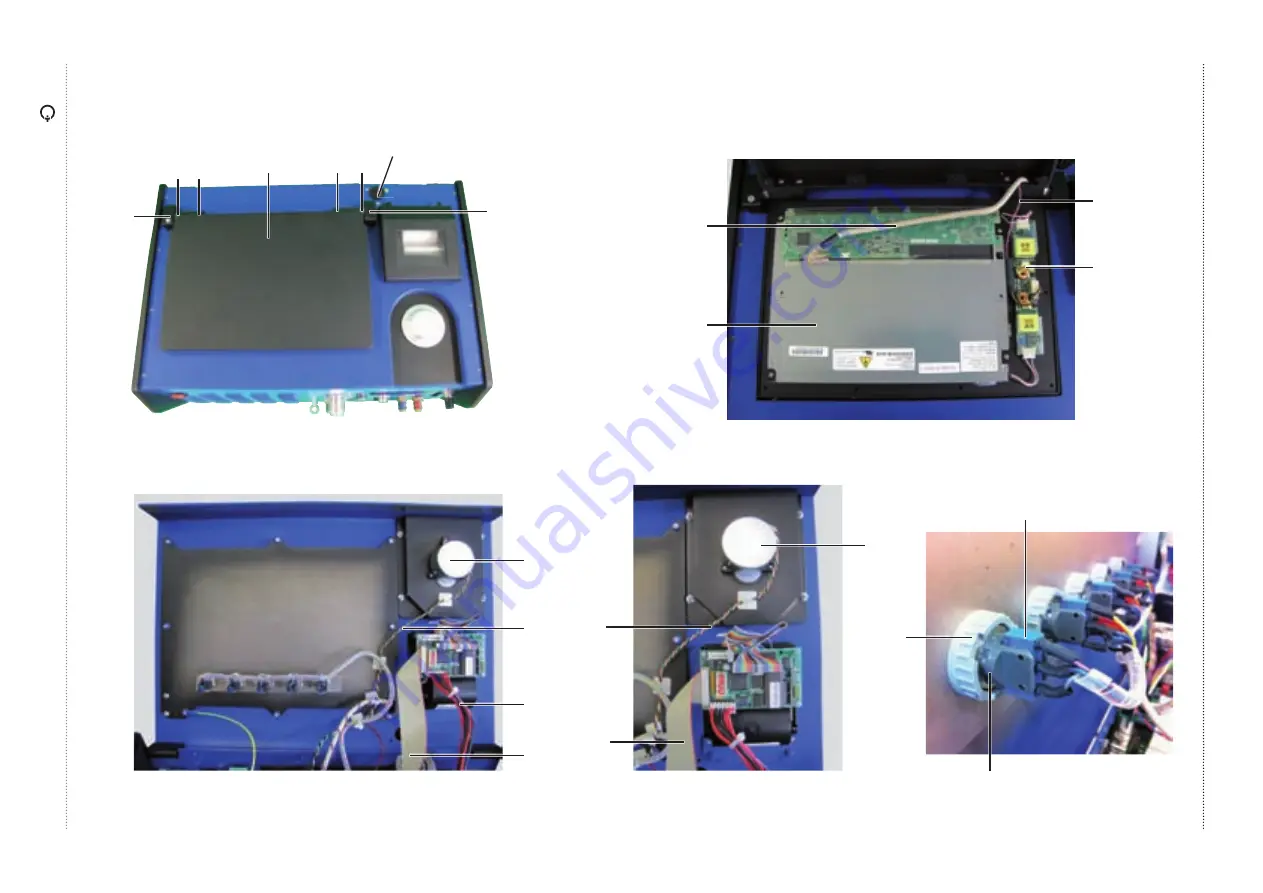
8 |
or
bi
ta
lum
to
ol
s
G
m
bH
, D
-7
82
24 S
in
ge
n, w
w
w
.o
rb
ita
lu
m
.c
om
, T
el. +
49 (
0) 7
7 3
1 7
92
-0
O
W
_E
TL
_O
RB
IM
AT
_1
65
C
A
_8
71
.0
60
.1
01
_D
E_E
N_
03
16
5 C
A H
au
b
e & D
is
p
la
y | M
ain C
ov
er & D
is
p
la
y
O
R
B
IM
AT 1
65 C
A
|
E
rs
at
zt
ei
lli
st
e |
S
pa
re
pa
rt
s li
st
7
1 2
3
16
6
4
5
165 CA HAUBE & DISPLAY | MAIN COVER & DISPLAY
9
10
11
8
12
13
15
14
17
18
19
13
12
14
Summary of Contents for ORBIMAT 165 CA
Page 78: ...orbitalum tools gmbh Notizen Notes ...
Page 79: ......