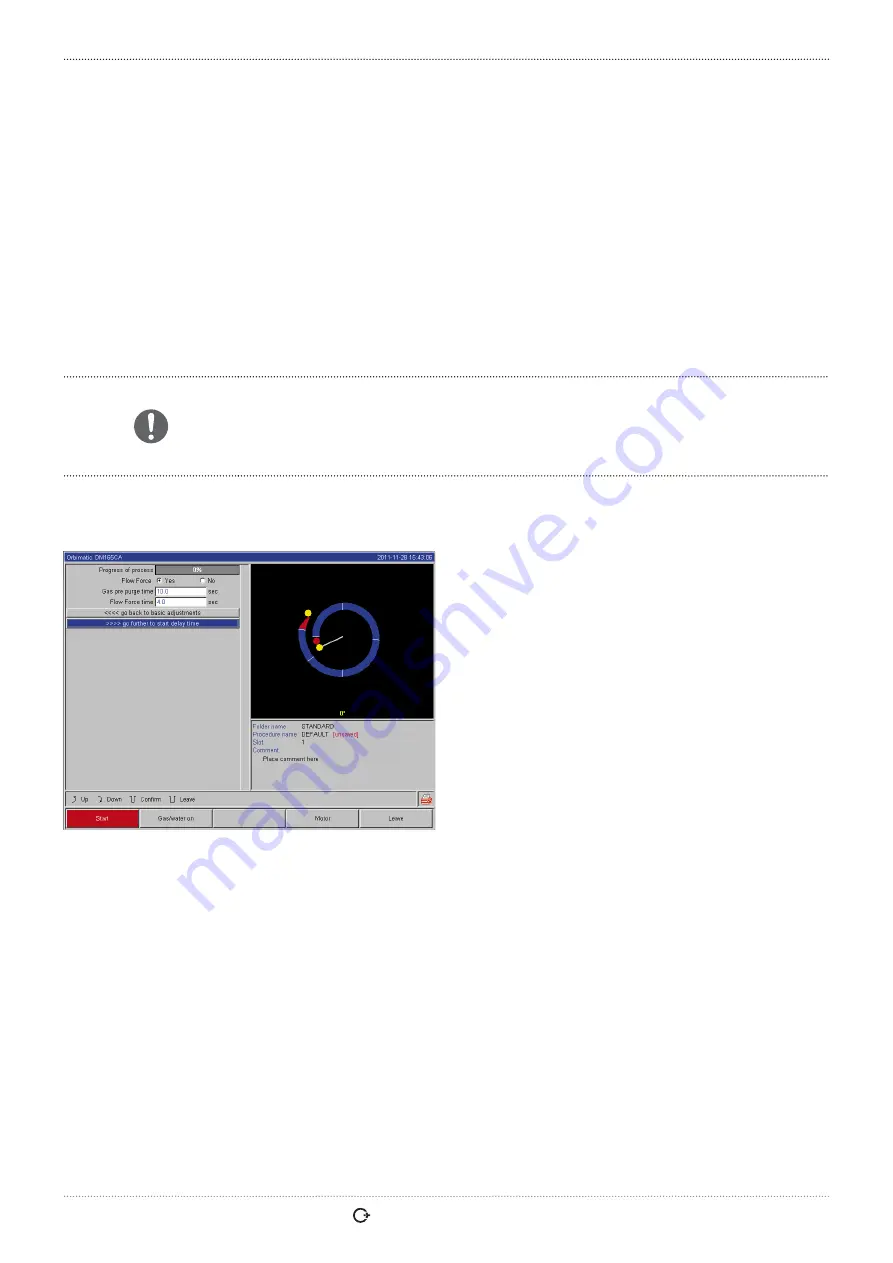
(01.2012) OM_BA_ORBIMAT_CA_01_EN
orbitalum tools
GmbH, D-78224 Singen, www.orbitalum.com, Tel. +49 (0) 77 31 792-0
| 47
ORBIMAT CA
| Operating instructions
OPERATION
8.7
Using the second gas pressure level ("flow force")
Auto programming generates gas pre purge times of 30 seconds if a closed weld head is selected.
The machine can first fill the weld head with a higher gas pressure during the gas pre purge time to reduce the time.
The gas pre purge time is the total time for filling the welding pocket before welding.
Only values which are at least 2 seconds shorter than the total gas pre purge time are possible for the flow force. This
time difference of 2 seconds is necessary so that a corresponding pressure compensation can occur in the weld head
before ignition of the arc. The increased flow speeds of the flow force also causes turbulence, which could negatively
affect stable arc ignition.
The correct value depends on the following parameters: Pressure setting on pressure reducer, pocket size, weld head
size and pipe diameter
If oxidation occurs near the start position on the fully welded part, the potential reduction has been reached.
The oxidation indicates possible uneven gas coverage at the start of welding.
X
Determine setting values by testing.
The flow force must be activated manually. During the pre purge at increased pressure,
the measuring tube on the front of the machine does not indicate the correct value. Gas
monitoring by the sensor does not occur until the end of the time of the "second gas
duct", i.e. at the start of the pressure compensation. Using this function together with
open-type weld tongs has no advantage and is of no use.
Activating a gas pressure level
1. Switch to "Welding" mode with "go forward to gas pre purge time" to set the gas pre purge time.
The following display appears:
Fig. 27: Flow force
2. Select the "Yes" option for "Flow Force".
The "Flow Force time" field is activated.
3. Enter and save value for the flow force.
8.8
Connecting supplementary devices
8.8.1
ORB 1001 Residual Oxygen Meter
The BUP control unit enables a defined and programmable internal pipe pressure (forming gas) to be built up in con-
junction with suitable plugs for closing off the pipe on both sides. This pressure is controlled based on the electrode
position. Thus an incursion of the weld seam which occurs in the flat position can be reduced or eliminated.
The residual oxygen meter can be used separately or connected to the machine.
Separate use
: If the limit value set at the meter is undershot by the device, a warning signal is sounded. This has no
effect on the welding process. The operator can carry out other measures.
Connection to the machine
: The machine cannot be started as long as the residual oxygen value lies above the set limit
value. If the limit value is exceeded, the process is canceled and a note is entered in the log.
Summary of Contents for ORBIMAT 165 CA
Page 78: ...orbitalum tools gmbh Notizen Notes ...
Page 79: ......