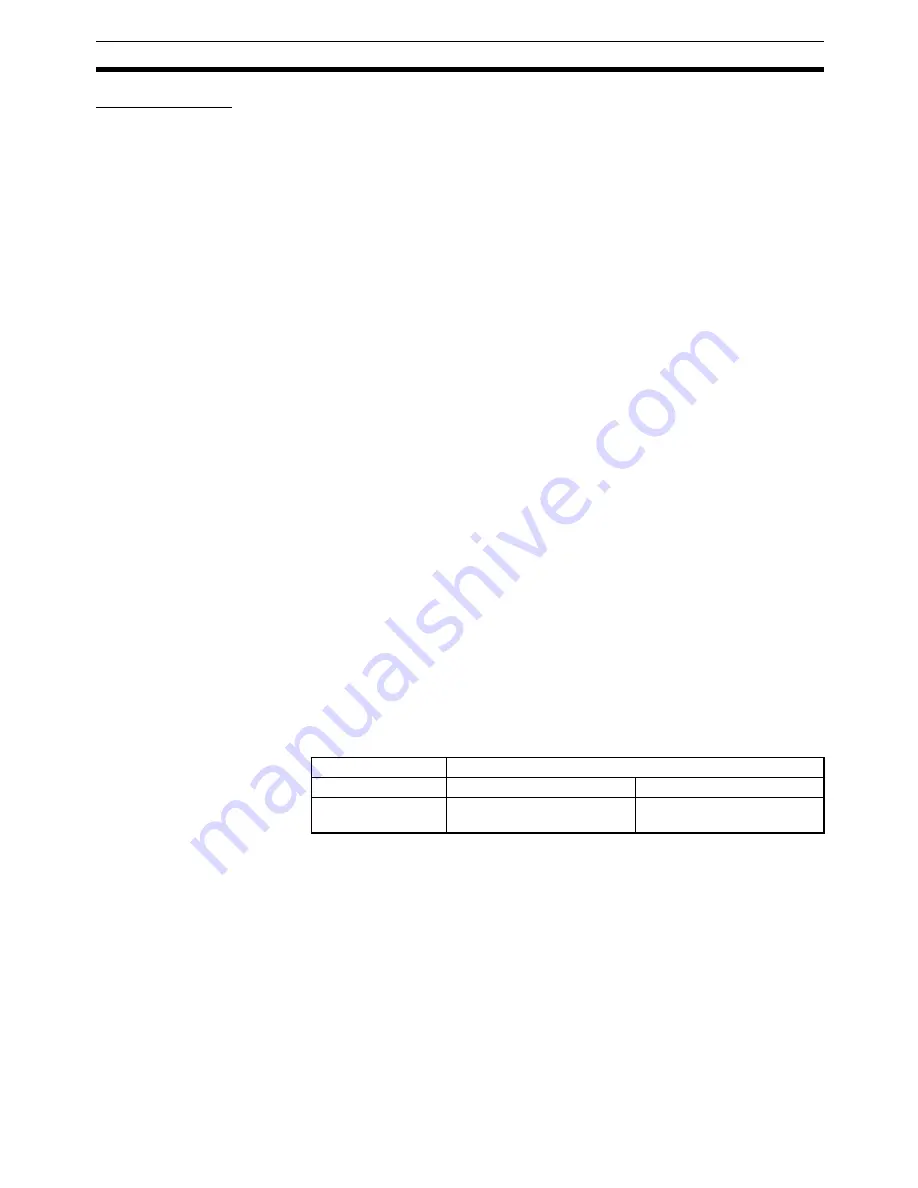
3
Introduction and Features
Section 1-1
Word Allocation
Data is exchanged between the CPU Unit and the Temperature Control Unit
through the PLC’s memory areas. A part of the CIO Area (the Special I/O Unit
Area) and part of the DM Area are reserved for the Special I/O Units.
The Temperature Control Unit requires 20 words in the CIO Area and 100
words in the DM Area. (The unit number set on the front of the Unit deter-
mines which words are actually allocated to the Unit.)
1-1-2
Features
Use ON/OFF Control or
PID Control with 2 or 4
Control Loops
The Temperature Control Unit can perform basic ON/OFF control as well as
PID control of two or four control loops. The PID control function has two
degrees of freedom and an autotuning function that can be used to autotune
the PID value.
Connect Temperature
Sensors Directly
Temperature sensors can be connected directly to the Temperature Control
Unit (two or four inputs). There are two models that support thermocouples
(R, S, K, J, T, B, and L thermocouples) and two models that support platinum
resistance thermometers.
500-ms Sampling Cycle
PID control is performed with a sampling cycle of 500 ms, regardless of the
CPU Unit’s cycle time.
Unrestricted CPU Unit
Cycle Time
There are no restrictions on the CPU Unit’s cycle time.
RUN/STOP Control from
CPU Unit
Commands can be sent from the CPU Unit to switch the Temperature Control
Unit’s PID control between RUN and STOP.
Independent Operation in
PROGRAM Mode
A switch on the front of the Unit (pin 1 of the DIP switch) selects whether the
Temperature Control Unit will continue operation or stop when the CPU Unit is
in PROGRAM mode.
Terminal Block
Connections
Both inputs and outputs are connected through a terminal block.
Store and Display Data in
BCD or Hexadecimal
A switch on the front of the Unit (pin 3 of the DIP switch) selects whether the
Temperature Control Unit’s data is handled as 4-digit BCD or binary (i.e., 4-
digit hexadecimal.) This switch setting controls both the display format and the
storage format in the memory areas (CIO and DM Areas) used to exchange
data between the CPU Unit and Temperature Control Unit.
Select ON/OFF Control or
PID Control
A switch on the front of the Unit (pin 6 of the DIP switch) selects whether the
Temperature Control Unit operates with ON/OFF control or PID control with 2
degrees of freedom.
Note
The setting on pin 6 sets the control method for all of the Unit’s control loops.
The factory setting is PID control.
Control Methods
• ON/OFF Control
With ON/OFF control, the control output will be ON when the PV is below
the SV. The control output will be OFF when the PV is at or above the SV.
(This control method is used when the Unit is set for reverse operation.)
• PID Control with Two Degrees of Freedom
In earlier versions of PID control, the same controller section controlled
both the response to the SV and the response to disturbances. The weak-
Example
Data storage/display format
Sensor input
Binary (4-digit hexadecimal)
4-digit BCD
K:
−
200 to 1,300
°
C
FF38 to FFFF to 0514
(
−
200 to
−
1 to 1,300)
F200 to 1300
(
−
200 to 1,300)
Summary of Contents for Sysmac CJ Series
Page 1: ...OPERATION MANUAL Cat No W396 E1 03 SYSMAC CJ Series CJ1W TC Temperature Control Units...
Page 2: ...CJ1W TC Temperature Control Units Operation Manual Revised December 2005...
Page 3: ...iv...
Page 5: ...vi...
Page 13: ...xiv...
Page 23: ......
Page 93: ......
Page 105: ......
Page 107: ......
Page 113: ......
Page 115: ......