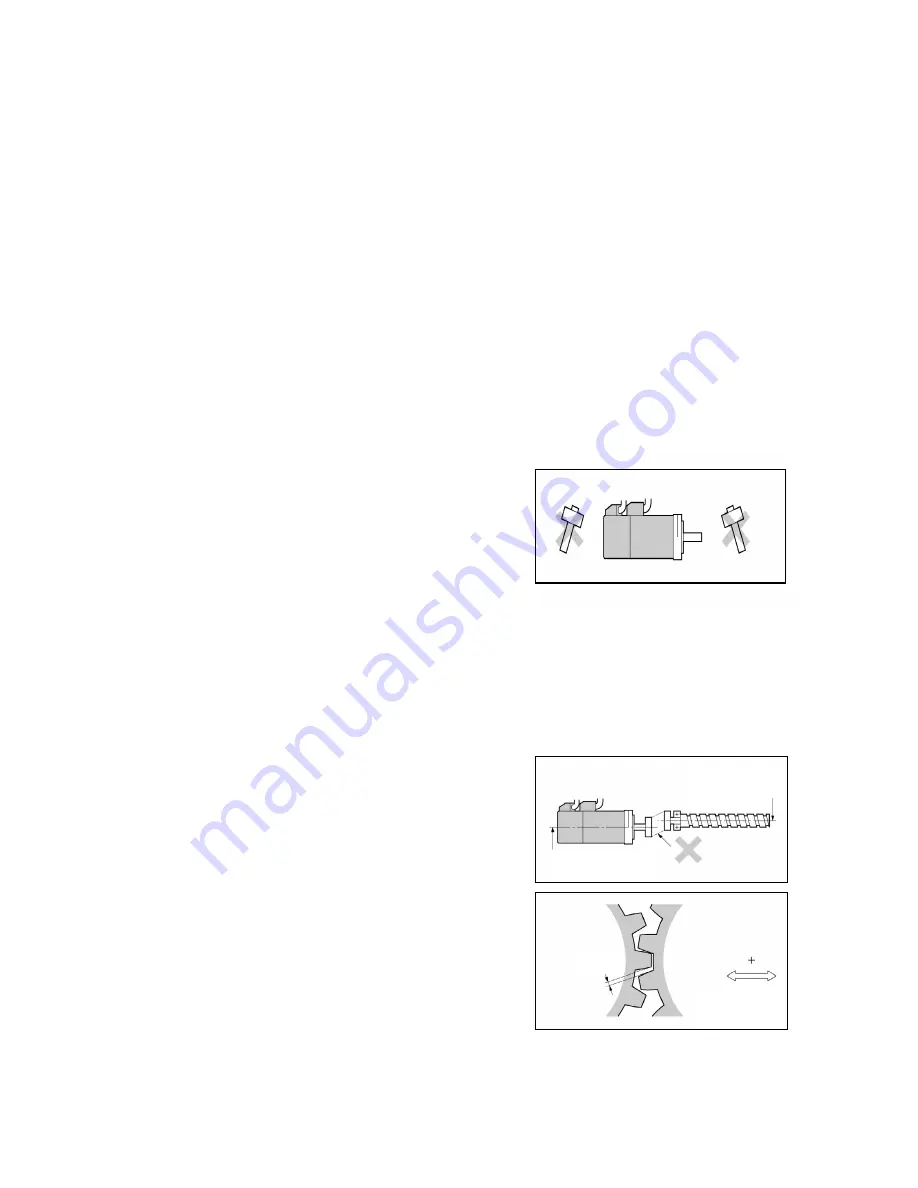
4-1 Installation Conditions
4-1-2 Servomotors
Keeping Foreign Objects Out of Units
•
Place a cover over the Units or take other preventative measures to prevent foreign
objects, such as drill filings, from getting into the Units during installation. Be sure to
remove the cover after installation is complete. If the cover is left on during operation,
heat buildup may damage the Units.
•
Take measures during installation and operation to prevent foreign objects such as
metal particles, oil, machining oil, dust, or water from getting inside of Servo Drivers.
4-1-2 Servomotors
Operating Environment
The environment in which the Servomotor is operated must meet the following conditions.
Operating the Servomotor outside of the following ranges may result in malfunction of the
Servomotor.
•
Ambient operating temperature: 0 to +40°C
•
Ambient operating humidity: 20% to 80% (with no condensation)
•
Atmosphere: No corrosive gases.
Impact and Load
•
The Servomotor is resistant to impacts of
up to 98 m/s
2
. Do not subject it to heavy
impacts or loads during transport,
installation, or removal.
•
When transporting it, hold onto the
Servomotor itself, and do not hold onto the
encoder, cable, or connector areas.
Holding onto weaker areas such as these
can damage the Servomotor.
•
Always use a pulley remover to remove
pulleys, couplings, or other objects from
the shaft.
•
Secure cables so that there is no impact o
load placed on the cable connector areas.
r
Connecting to Mechanical Systems
•
The axial loads for Servomotors are
specified in
3-2-2 Characteristics
. If an
axial load greater than that specified is
applied to a Servomotor, it will reduce the
service life of the motor bearings and may
damage the motor shaft.
Ball screw center line
Do not offset center lines.
Servomotor shaft
center line
Backlash
Adjust backlash by
adjusting the
distance between
shafts.
•
When connecting to a load, use couplings
that can sufficiently absorb mechanical
eccentricity and variation.
•
For spur gears, an extremely large radial
load may be applied depending on the
gear precision. Use spur gears with a high
degree of accuracy (for example, JIS class
2: normal line pitch error of 6 µm max. for
a pitch circle diameter of 50 mm).
•
If the gear precision is not adequate, allow
backlash to ensure that no radial load is
placed on the motor shaft.
4-3
Summary of Contents for SMARTSTEP Junior R7D-ZP
Page 3: ...2 ...
Page 18: ...Section 1 Configuration Features and System ...
Page 25: ...1 5 Applicable Standards 1 5 2 UL and cUL Standards 1 8 ...
Page 26: ...Section 2 Dimensions Standard Models and ...
Page 36: ...Section 3 Specifications ...
Page 62: ...Section 4 System Design ...
Page 86: ...Section 5 Operation ...
Page 96: ...Section 6 Troubleshooting ...
Page 109: ...6 5 Periodic Maintenance 6 5 3 Replacing the Cooling Fan 6 14 ...
Page 110: ...Appendix ...