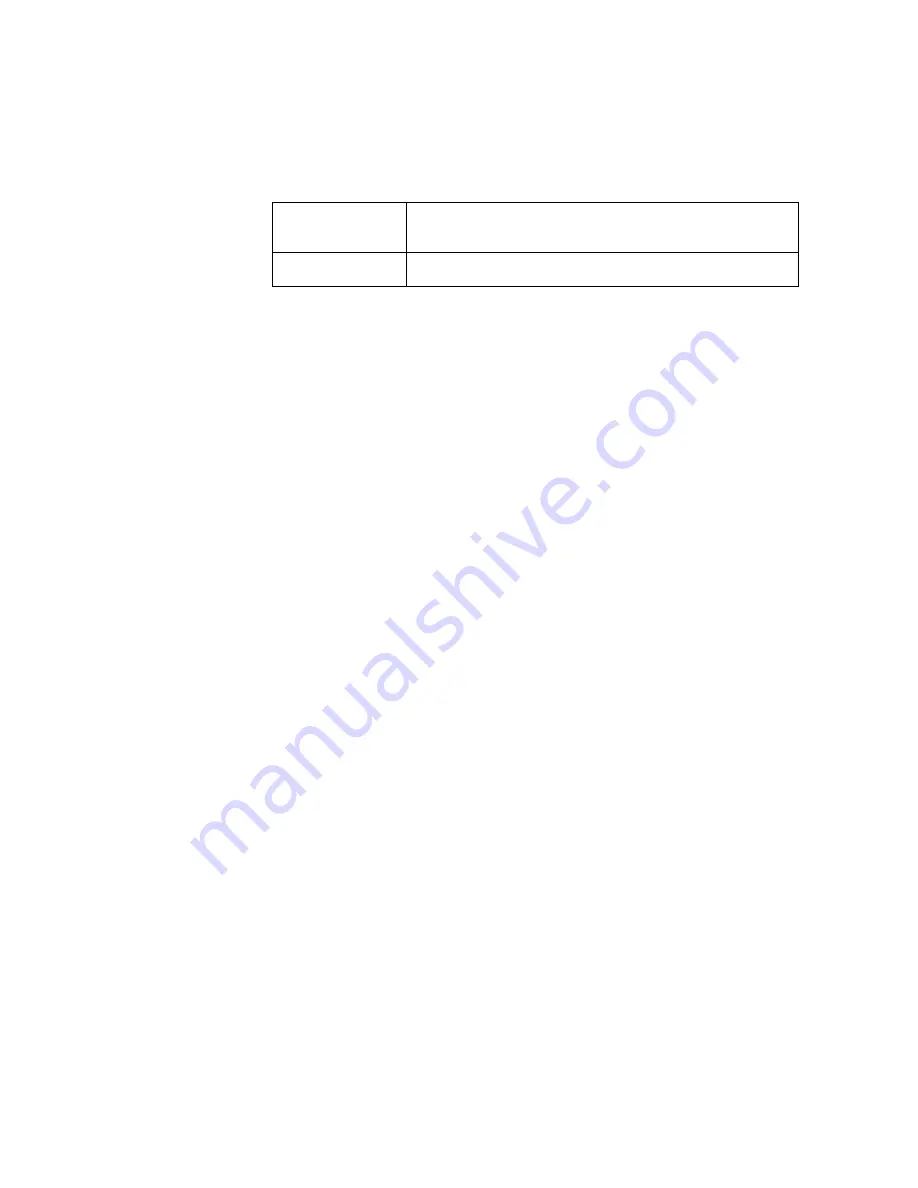
6-5 Periodic Maintenance
6-5-2 Servo Driver Maintenance
6-5-2
Servo Driver Maintenance
The recommended periodic maintenance schedule is listed in the following table.
Please consult with your OMRON representative to determine whether or not
components need to be replaced.
Aluminum electrolytic
capacitors
50,000 hours, at an ambient Servo Driver operating temperature of 40°C,
80% of the rated operation output (rated torque), installed as described in
operation manual.
Axle fan
30,000 hours, at an ambient Servo Driver operating temperature of 40°C
and an ambient humidity of 65%.
•
When using the Servo Driver in continuous operation, use fans or air conditioners to
maintain an ambient operating temperature below 40°C.
•
We recommend that ambient operating temperature and the power ON time be
reduced as much as possible to lengthen the maintenance intervals for Servo
Drivers.
•
The life of aluminum electrolytic capacitors is greatly affected by the ambient
operating temperature. Generally speaking, an increase of 10°C in the ambient
operating temperature will reduce capacitor life by 50%.
•
The aluminum electrolytic capacitors deteriorate even when the Servo Driver is
stored with no power supplied. If the Servo Driver is not used for a long time, we
recommend a periodic inspection and part replacement schedule of five years.
•
If the Servomotor or Servo Driver is not to be used for a long time, or if they are to
be used under conditions worse than those described above, a periodic inspection
schedule of five years is recommended.
6-5-3
Replacing the Cooling Fan
Please contact your OMRON representative regarding cooling fan replacement.
6-13
Summary of Contents for SMARTSTEP Junior R7D-ZP
Page 3: ...2 ...
Page 18: ...Section 1 Configuration Features and System ...
Page 25: ...1 5 Applicable Standards 1 5 2 UL and cUL Standards 1 8 ...
Page 26: ...Section 2 Dimensions Standard Models and ...
Page 36: ...Section 3 Specifications ...
Page 62: ...Section 4 System Design ...
Page 86: ...Section 5 Operation ...
Page 96: ...Section 6 Troubleshooting ...
Page 109: ...6 5 Periodic Maintenance 6 5 3 Replacing the Cooling Fan 6 14 ...
Page 110: ...Appendix ...