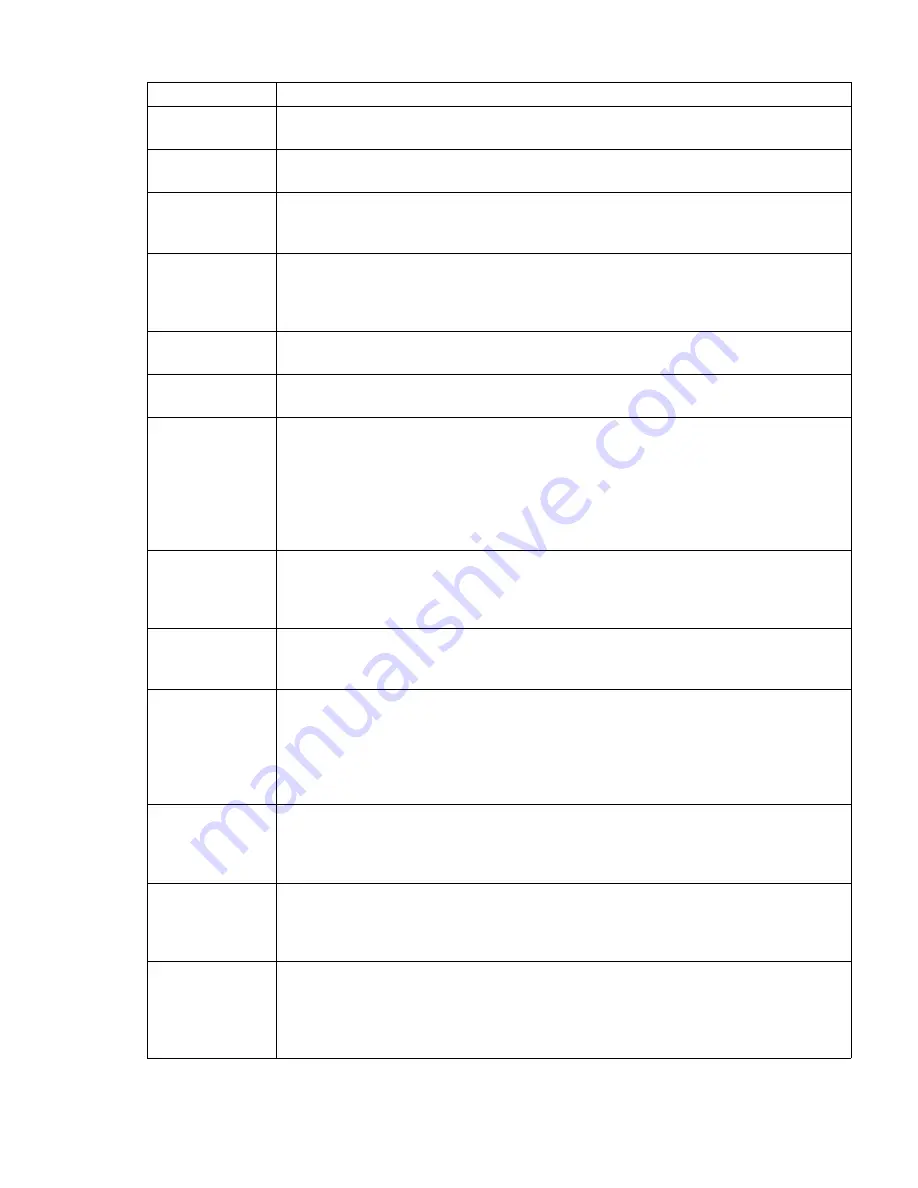
How to Operate the Arizona T220UV
61
Hints and Tips
[21] Hints and Tips
Situation
Solution
Maximum Ink
Restrictions
You can go right up to the maximum of 100% with 100% overstrike, if required. Use only enough
ink to achieve sufficient Dmax and good-looking reds.
Recommended
Dmax Values
Recommended Dmax values are approximately: C,M 1.4, Y .8, K 1.6.
Increasing Black
Density
Use ICC profiles. Or use color replacement to change 100%K to a rich black. 40% C, 30% M, 30%
Y, 100 %K have given good results on a variety of media. The maximum recommended values are
60% C, 40% M, 40% Y, 100% K.
Head Swabbing
Frequency
Monitor the diagnostic strip and swab heads if a recovery purge of the problem color does not re-
solve the problem. The required swab frequency will be dependent on many factors such as: printer
duty cycle used, print volume, and media/air cleanliness. In a low volume production setting, typi-
cally swab heads about once a week.
Printing on uneven
surfaces
Use a thickness equal to the thickest value of the media, and print unidirectional.
Overprinting
Techniques
Overprinting may be required on some media to build up ink density - e.g., backlit material or glass.
Hitting color and proper linearization when using overprinting is difficult.
Thermal Expansion
of Media
Some media, such as Styrene, Fome-Cor, or plexiglass, is subject to expansion when subjected to
heat. If multiple pieces of these media are used, allow enough space between the pieces to allow for
thermal expansion. Placing tape on the table prior to laying down the media will prevent ink from
being imaged onto the table. When overprinting on media that will expand when heat is applied, we
recommend that you group the desired image with a preceding image so the printer is a consistent
temperature when starting to print the desired image. Note that color-to-color registration may be
affected if the media expands significantly between printing the first and last colors.
Using a generic ICC
Profile
If an ICC profile is not available for a particular media and it is not possible/convenient to create
one specifically for that media, determine the ink restriction values required to achieve Dmax for
that media. Then select an ICC profile for another media that uses the same ink restriction values
and has similar dot gain characteristics and the result may be satisfactory.
Imaging on
Fome-Cor
Fome-Cor has a tendency to warp when heat is applied. However it will go back to it’s original shape
once cooled. Media Holder Strips (aluminium bars) with a 45 degree chamfer are available to hold
down the Fome-Cor. The bars are 2” wide and 32” long.
Imaging on Core-
plast - avoiding
warping
When imaging on Coreplast set Full Carriage Travel to On in the Operator/Maintenance/Print. This
reduces the tendency of the media to turn warp near the outer edges from excessive heat generated
by the UV lamps. By having it travel beyond the edge of the media during each swath there is less
concentration of heat from the UV light during the time the carriage changes direction. Also consid-
er lower the power level of the UV lamps. The power level must be set only high enough to cure the
ink.
Imaging on Sintra -
avoiding brown
edges
When imaging on Sintra set Full Carriage Travel to On in the Operator/Maintenance/Print. This re-
duces the tendency of the media to turn brown near the outer edges from excessive exposure to UV
light. By having it travel beyond the edge of the media during each swath there is less concentration
of UV light during the time the carriage changes direction.
Avoid Printing
Large White Space
Areas
Do not add white space to an image to center it on the media, instead use the center media option in
the PosterShop Layout Preview dialog to center the image. Adding white space to the image increas-
es the print time and may dry out the nozzles resulting in over-spray and banding. Turning on the
regular stripe on the away side of the image, will help prevent the nozzles from over-spraying.
Imaging on a new
media
When imaging on a new media for the first time (i.e., you do not have a media model for the media),
we recommend that you guess at an appropriate ink restriction level and heater duty cycle. Then
print either a test image or the job to be printed prior to doing linearization. Once reasonable ink
restriction values and heater duty cycles are selected, linearization and ICC profiling can be done,
if required.
Summary of Contents for Arizona T220UV
Page 1: ...Arizona T220UV User Guide...
Page 5: ...5 Arizona T220UV User Guide Chapter 1 Introduction...
Page 10: ...10 T220UV User Guide...
Page 11: ...11 Arizona T220UV User Guide Chapter 2 Product Overview...
Page 15: ...15 Arizona T220UV User Guide Chapter 3 Safety Information...
Page 30: ...30 T220UV User Guide...
Page 31: ...31 Arizona T220UV User Guide Chapter 4 User Interface...
Page 40: ...40 T220UV User Guide...
Page 41: ...41 Arizona T220UV User Guide Chapter 5 How to Operate the Arizona T220UV...
Page 63: ...63 Arizona T220UV User Guide Chapter 6 Ink System Management...
Page 71: ...71 Arizona T220UV User Guide Chapter 7 Media Management...
Page 77: ...77 Arizona T220UV User Guide Chapter 8 Error Handling and Troubleshooting...
Page 92: ...92 T220UV User Guide...
Page 93: ...93 Arizona T220UV User Guide Chapter 9 Printer Maintenance...
Page 114: ...114 T220UV User Guide...