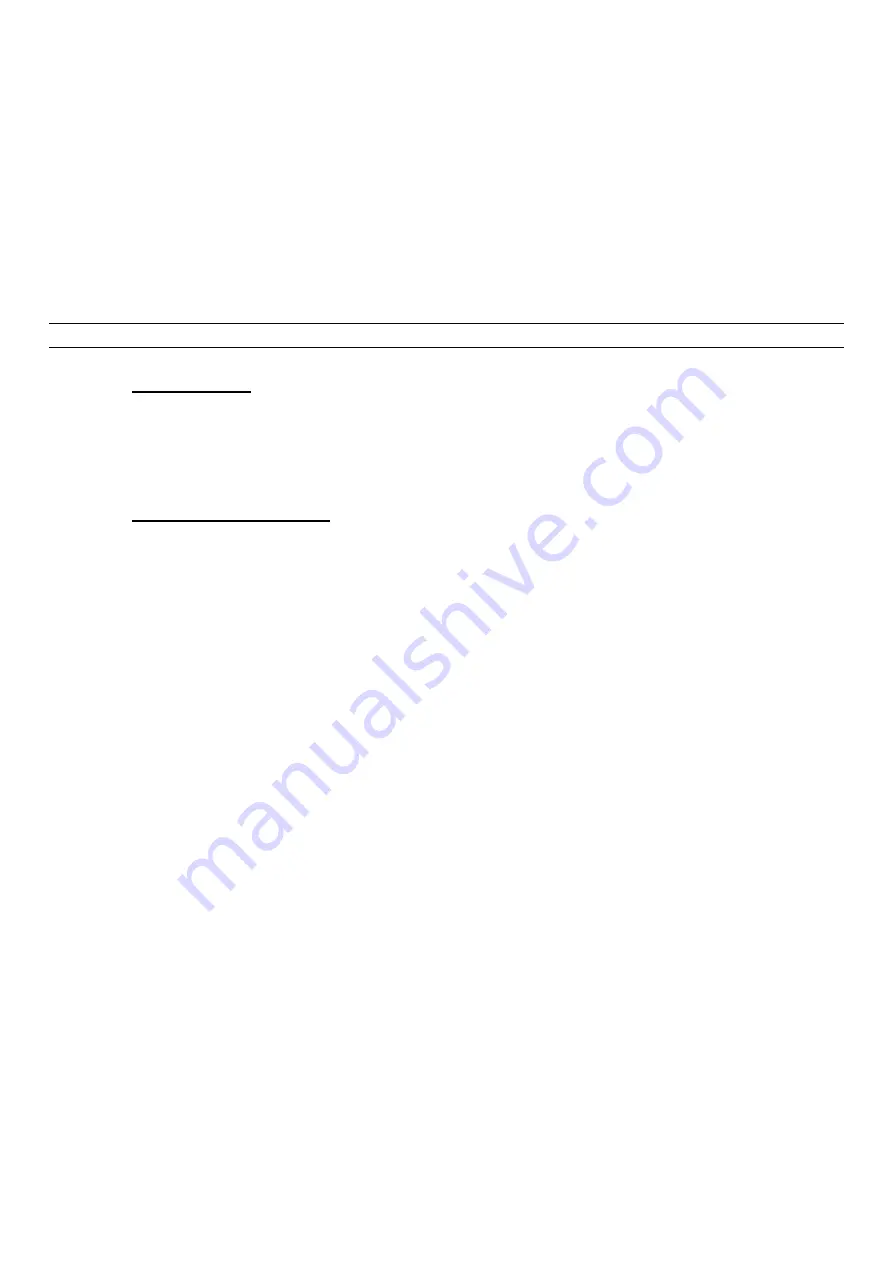
5
Make sure that suitable precautions have been implemented to avoid and combat any possible risks.
In the event of refrigerant leakage:
The refrigerant may lead to asphyxiation if it is inhaled in high concentrations. It is necessary to ensure adequate
ventilation for the room in which the chiller is installed.
Be sure to the read the safety data sheet with the relevant values and warnings.
Excessive pressure on the cooling medium side:
The chiller is equipped with safety devices on the cooling medium side.
These have to be mounted by the installation technician. The installation of any such devices must comply with the
applicable national standards and be carried out in accordance with the limits given in this manual.
Depletion of the ozone layer:
The use of HFC refrigerants, in compliance with Regulation CE/842/2006, reduces damage to the ozone layer and
minimizes the greenhouse effect.
3.
DESCRIPTION OF THE CHILLER, COMPONENTS AND OPTIONS
3.1
DESCRIPTION
The chiller is supplied ready for connection. It consists of a housing, a fully hermetically sealed cooling medium cir-
cuit, the refrigerant circuit, the cooling medium circuit and the electrical circuit, including all control and monitoring
devices which are required for fully automatic operation. The selected and used cooling medium must comply with
environmental standards and the legal provisions.
3.2
REFRIGERANT CIRCUIT
3.2.1
STANDARD COMPONENTS USED IN THE CHILLER
The preceding abbreviations indicate the position in the drawings.
Not all components are contained in all models.
C
Ø
Compressor
Scroll-type compressor of fully hermetic design with integrated bimetal switch and oil sight glass.
Semi-hermetic compressor:
Semi-hermetic compressor with integrated bimetal switch and oil sight glass.
Reciprocating piston compressor:
Reciprocating piston compressor, fully hermetic with integrated bimetal switch and, in most models, an oil sight
glass.
CND
Ø
Condenser / Condenser safety grating
Condenser as fin-type heat exchanger consisting of copper pipes with aluminium fins. The safety grating for the
housing protects the condenser on the inside against mechanical damage. The positioning of the condenser avoids
any additional heat load on the components located inside the housing.
EVA
Ø
Evaporator
Insulated shell tube heat exchanger or stainless steel plate heat exchanger.
HP
Ø
High-pressure pressostat
The high-pressure pressostat protects the refrigeration circuit of the chiller against excessively high operating pres-
sure (high-pressure fault).
In this kind of fault, the high-pressure pressostat switches the compressor off when the preset limit is exceeded.
The compressor cannot be started up again until the preset differential pressure has been reached and the Reset
button located inside the chiller has been pressed. The fault is displayed on the control unit.
LP
Ø
Low-pressure pressostat
The low-pressure pressostat protects the refrigeration circuit of the chiller against excessively low operating pres-
sure (low-pressure fault).
When this kind of fault occurs, the low-pressure pressostat switches the compressor off when the preset limit is
undershot. The compressor starts up automatically if when the permitted pressure ratios have been re-established
between the high and low pressure sides via the internal pressure compensation system. The fault is displayed on
the control unit while it persists.
Summary of Contents for OCGE 111
Page 69: ...69 11 2 WIRING DIAGRAM MODELS PCGE 11 to PCGE 25 PCGEZ 08 230V 1Ph 50Hz POWER COMMAND DIAGRAM ...
Page 70: ...70 MODEL PCGE 28 230V 1Ph 50Hz POWER COMMAND DIAGRAM ...
Page 71: ...71 MODEL PCGE 28 400V 3Ph 50Hz POWER COMMAND DIAGRAM ...
Page 72: ...72 MODELS PCGE 31 to PCGE 41 OCGE 31 to OCGE 41 230V 1Ph 50Hz POWER SECTION ...
Page 73: ...73 MODELS PCGE 31 to PCGE 41 OCGE 31 to OCGE 41 230V 1Ph 50Hz COMMAND SECTION ...
Page 78: ...78 MODELS PCGE 590 to PCGE 3300 PCGEZ 360 to PCGEZ 480 400V 3Ph 50Hz ...
Page 79: ...79 ...
Page 80: ...80 ...
Page 81: ...81 ...
Page 86: ...86 MODEL PCGE 1100 with tank and pump MODEL PCGE 1300 with tank and pump ...
Page 87: ...87 MODEL PCGE 1900 2200 with tank and pump MODEL PCGE 2900 3300 with tank and pump ...
Page 91: ...91 MODEL PCGE 1100 without tank MODEL PCGE 1300 without tank ...
Page 92: ...92 MODEL PCGE 1900 2200 without tank MODEL PCGE 2900 3300 without tank ...
Page 97: ...97 710 1789 00 00 02B 轜 07 05 2008 ...
Page 166: ...69 11 2 WIRING DIAGRAM MODELS PCGE 11 to PCGE 25 PCGEZ 08 230V 1Ph 50Hz POWER COMMAND DIAGRAM ...
Page 167: ...70 MODEL PCGE 28 230V 1Ph 50Hz POWER COMMAND DIAGRAM ...
Page 168: ...71 MODEL PCGE 28 400V 3Ph 50Hz POWER COMMAND DIAGRAM ...
Page 169: ...72 MODELS PCGE 31 to PCGE 41 OCGE 31 to OCGE 41 230V 1Ph 50Hz POWER SECTION ...
Page 170: ...73 MODELS PCGE 31 to PCGE 41 OCGE 31 to OCGE 41 230V 1Ph 50Hz COMMAND SECTION ...
Page 175: ...78 MODELS PCGE 590 to PCGE 3300 PCGEZ 360 to PCGEZ 480 400V 3Ph 50Hz ...
Page 176: ...79 ...
Page 177: ...80 ...
Page 178: ...81 ...
Page 183: ...86 MODEL PCGE 1100 with tank and pump MODEL PCGE 1300 with tank and pump ...
Page 184: ...87 MODEL PCGE 1900 2200 with tank and pump MODEL PCGE 2900 3300 with tank and pump ...
Page 188: ...91 MODEL PCGE 1100 without tank MODEL PCGE 1300 without tank ...
Page 189: ...92 MODEL PCGE 1900 2200 without tank MODEL PCGE 2900 3300 without tank ...