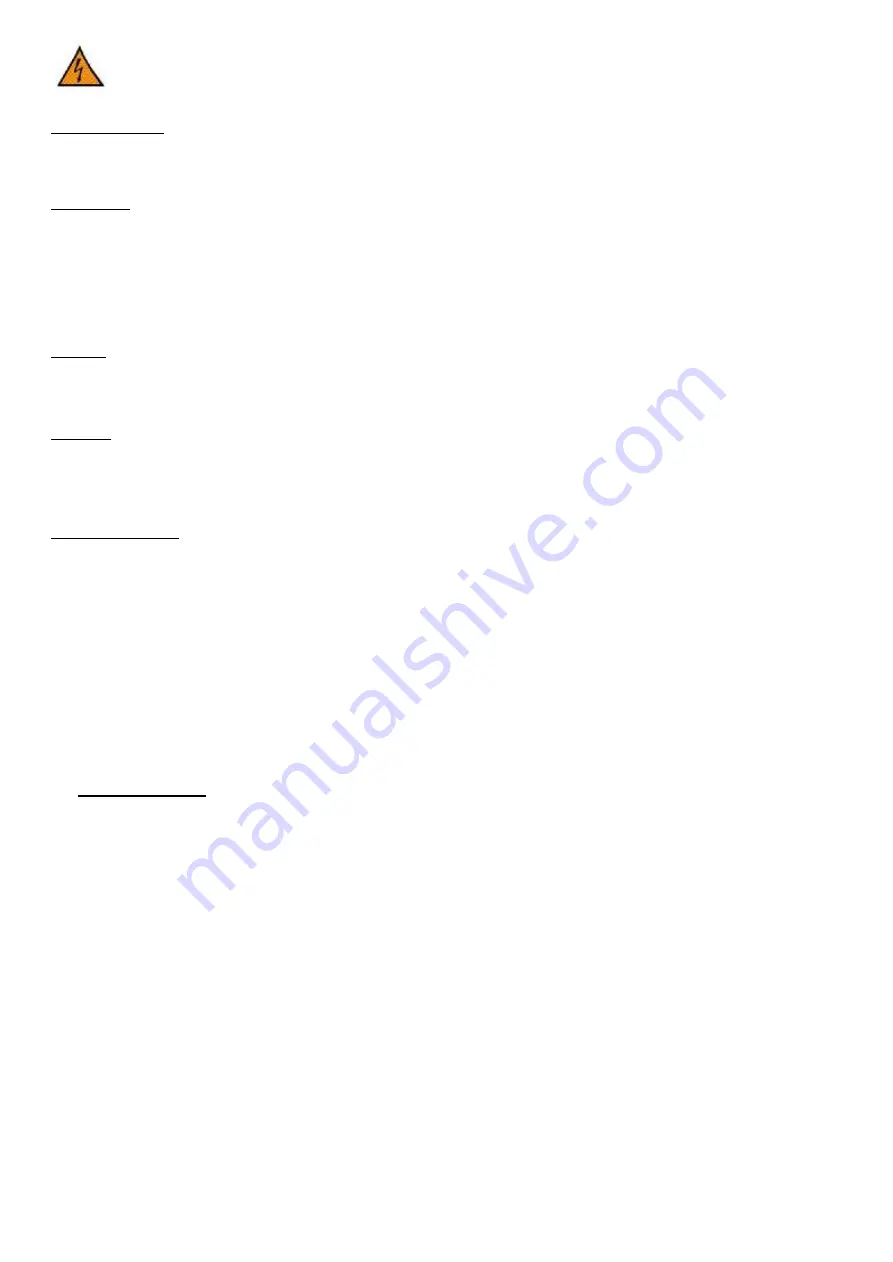
25
Never use any liquid substances to clean the finned pack. If necessary, contact an authorized
service centre to have the cleaning carried out!
Obligatory maintenance
Every 6 months:
In compliance with the Regulation CE/842/2006, refrigeration equipment that contains more than 30 kg of refriger-
ant has to be inspected every six months in order to prevent any occurrence of leakages. This inspection has to be
documented in the daily records (see Section 7.2).
Every year:
In compliance with the Regulation CE/842/2006, refrigeration equipment that contains more than 3 kg of refriger-
ant has to be inspected annually in order to prevent any occurrence of leakages. This inspection has to be docu-
mented in the daily records (see Section 7.2).
Ordinary maintenance operations
Ordinary maintenance work does not involve any access to internal machine parts. Do not remove, even partially,
any covers of the machine parts for this purpose.
Weekly:
1)
Check from the outside whether the level of cooling medium in the tank is within the limits that can be seen
on the display on the side of the chiller.
2)
Check whether the cooling medium temperature matches the required temperature.
Monthly:
1)
Check the finned pack of the condenser from outside. If there are any deposits, clean them using a com-
pressed air jet with a pressure of not more than 3 bar.
2)
Make sure that the compressor is not producing any unusual vibrations.
3)
Check the cleanliness of the filter and clean it if necessary.
Every 4-6 months:
1)
Check whether the current consumption of the compressor group is within the target values indicated in
these instructions.
2)
Clean the fin pack of the condenser using a compressed air jet with a pressure of not more than 3 bar in
order to remove all deposits that might impair its efficiency. The frequency of cleaning depends on the qual-
ity of the ambient air; in any case we suggest that you clean the condenser at the beginning of the sum-
mer. if necessary, straighten any bent aluminium fins.
3)
Check the quality of the cooling medium.
Change the glycol mixture according to the chiller application (see glycol safety sheet).
To change the mixture, undo the level indicator and empty the tank through the discharge tube.
If you have any further queries arise concerning products, applications and any problems that arise, please contact
the manufacturer of an authorized Technical Service Centre.
To guarantee the efficiency and safety of the chiller, you should always order and use only original spare parts.
DAILY RECORD
According to European standard EN 378-1 (Safety of pressure vessels), it is necessary to keep a daily record of the
cooling system.
The record, the form of which is at the user
½
s discretion, must contain the following information:
All repair and maintenance operations:
1)
Refrigerant loss (new, reused, recycled) and refrigerant quantities used for each maintenance operation.
2)
Test results for the refrigerant.
3)
Source of the refrigerant.
4)
Modifications and replacement of system components.
5)
Periodic test results.
6)
Daily operating time of the refrigeration equipment.
Always store the record within reach of the person responsible for the maintenance, e.g. in the machine room.
Summary of Contents for OCGE 111
Page 69: ...69 11 2 WIRING DIAGRAM MODELS PCGE 11 to PCGE 25 PCGEZ 08 230V 1Ph 50Hz POWER COMMAND DIAGRAM ...
Page 70: ...70 MODEL PCGE 28 230V 1Ph 50Hz POWER COMMAND DIAGRAM ...
Page 71: ...71 MODEL PCGE 28 400V 3Ph 50Hz POWER COMMAND DIAGRAM ...
Page 72: ...72 MODELS PCGE 31 to PCGE 41 OCGE 31 to OCGE 41 230V 1Ph 50Hz POWER SECTION ...
Page 73: ...73 MODELS PCGE 31 to PCGE 41 OCGE 31 to OCGE 41 230V 1Ph 50Hz COMMAND SECTION ...
Page 78: ...78 MODELS PCGE 590 to PCGE 3300 PCGEZ 360 to PCGEZ 480 400V 3Ph 50Hz ...
Page 79: ...79 ...
Page 80: ...80 ...
Page 81: ...81 ...
Page 86: ...86 MODEL PCGE 1100 with tank and pump MODEL PCGE 1300 with tank and pump ...
Page 87: ...87 MODEL PCGE 1900 2200 with tank and pump MODEL PCGE 2900 3300 with tank and pump ...
Page 91: ...91 MODEL PCGE 1100 without tank MODEL PCGE 1300 without tank ...
Page 92: ...92 MODEL PCGE 1900 2200 without tank MODEL PCGE 2900 3300 without tank ...
Page 97: ...97 710 1789 00 00 02B 轜 07 05 2008 ...
Page 166: ...69 11 2 WIRING DIAGRAM MODELS PCGE 11 to PCGE 25 PCGEZ 08 230V 1Ph 50Hz POWER COMMAND DIAGRAM ...
Page 167: ...70 MODEL PCGE 28 230V 1Ph 50Hz POWER COMMAND DIAGRAM ...
Page 168: ...71 MODEL PCGE 28 400V 3Ph 50Hz POWER COMMAND DIAGRAM ...
Page 169: ...72 MODELS PCGE 31 to PCGE 41 OCGE 31 to OCGE 41 230V 1Ph 50Hz POWER SECTION ...
Page 170: ...73 MODELS PCGE 31 to PCGE 41 OCGE 31 to OCGE 41 230V 1Ph 50Hz COMMAND SECTION ...
Page 175: ...78 MODELS PCGE 590 to PCGE 3300 PCGEZ 360 to PCGEZ 480 400V 3Ph 50Hz ...
Page 176: ...79 ...
Page 177: ...80 ...
Page 178: ...81 ...
Page 183: ...86 MODEL PCGE 1100 with tank and pump MODEL PCGE 1300 with tank and pump ...
Page 184: ...87 MODEL PCGE 1900 2200 with tank and pump MODEL PCGE 2900 3300 with tank and pump ...
Page 188: ...91 MODEL PCGE 1100 without tank MODEL PCGE 1300 without tank ...
Page 189: ...92 MODEL PCGE 1900 2200 without tank MODEL PCGE 2900 3300 without tank ...