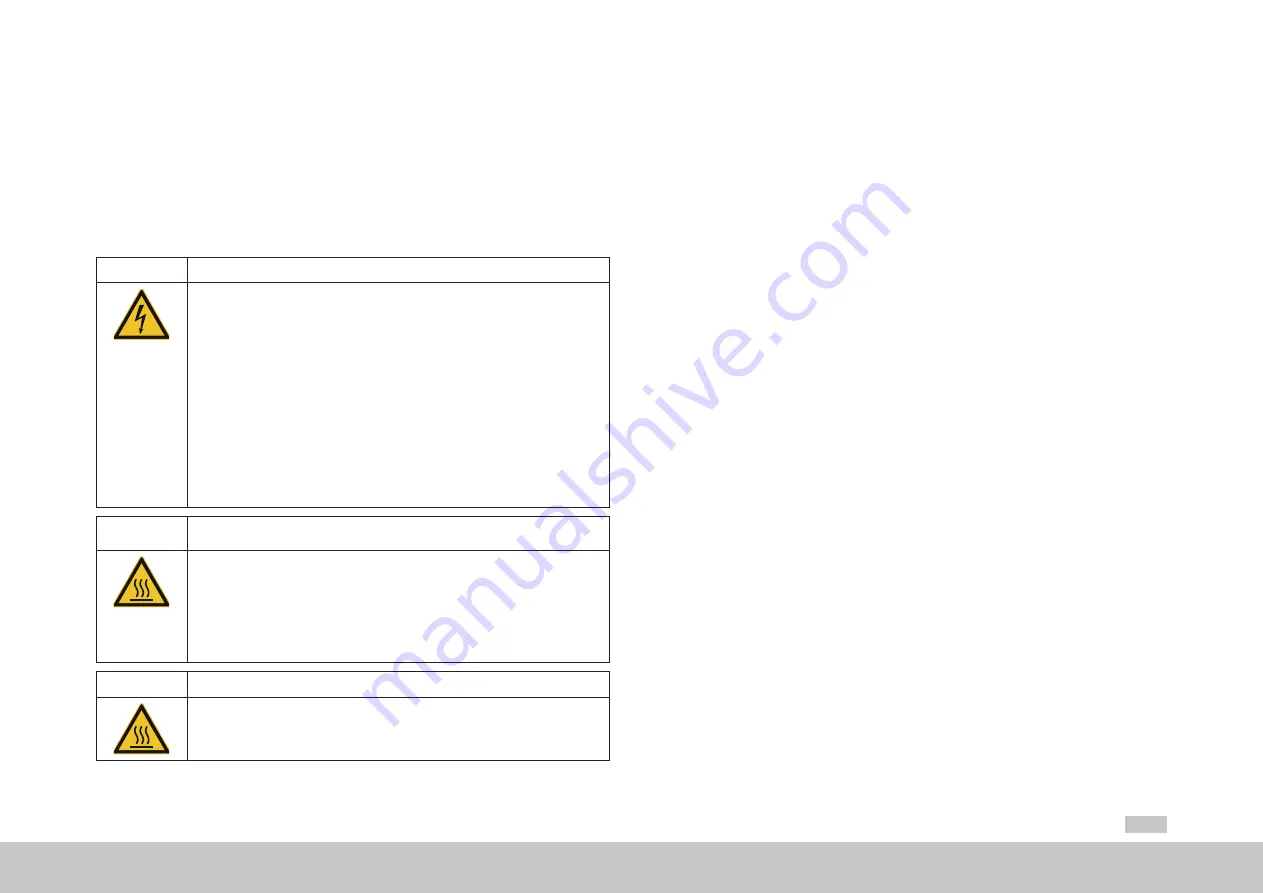
MSD Single-Axis System Operation Manual AC-AC Servo Drive
ID no.: CA65642-001 06/2018
moog
21
Electrical installation
4
Electrical installation
4.1 Notes for installation
It is imperative you pay attention to the following warnings and safety instructions prior to
and during installation.
DANGER!
Risk of injury due to electrical power!
•
Carelessness will result in serious injuries or death.
Never make or disconnect electrical connections while they are electrically live! Always
disconnect the power before working on the device. Even 10 min. (Size 1 to Size 4) / 30 min.
(Size 5 to Size 7) after switching off the mains supply, dangerously high voltages of ≥50 V
may still be present (capacitor charge).
So check that electrical power is not
present!
Work on the device must only be carried out after the DC link voltage has dropped below a
residual voltage of 50 V (on Size 1 to Size 6A to be measured on the terminals X11/L+ and L-,
on Size 7 on the terminals X11/ZK- and X11/ZK+).
Any existing additional DC link connections as well as all motor connections are to be checked
in relation to each other and in relation to earth to ensure they are not carrying any electrical
power. If necessary, all cable connections are to be discharged using suitable means.
A dangerous voltage may be present at the device, even if the device does not emit any visual
or audible signals/indications (e.g. with mains voltage applied to terminal X11 and missing
control 24 V on X9/X10 and X44)!
WARNING
!
Risk of injury due to hot surfaces on the device (heat sink)!
•
Carelessness may result in serious burns.
The device and especially the heat sink heat up significantly during operation and can reach
temperatures of up to +100 °C (+212 °C). Prior to starting work, make sure the device has
cooled down.
On touching there is a risk of burns to the skin. For this reason provide protection against
touching.
During mounting maintain an appropriate distance to neighbouring assemblies.
WARNING
!
Risk of injury due to hot coolant!
•
Carelessness may result in serious burns.
In operation the coolant reaches high temperatures. Prior to starting work, make sure the
coolant has cooled down.
4.2 Effective EMC installation
4.2.1
Cable type
y
Use only shielded mains, motor and signal cables. For all shielded connections, use cables with
double copper braiding with 60 to 70 % coverage.
y
If it is necessary to lay very large cable cross-sections, instead of shielded cables it is also
possible to lay separate individually shielded wires. Please contact our application specialists on
the Helpline.
4.2.2
Routing of cables
You should take into account the following points on laying the cables:
y
Route mains, motor and signal cables separated from one another. Maintain a distance of at
least 200 mm (7.87 in).
y
For smaller distances use separators for shielding; fasten the separators directly and
conductively to the backing plate.
y
Route the cables close to ground potential. On the usage of cable ducts made of plastic, the
cable ducts must be fastened directly to the backing plates or the frame. Open space must not
be spanned, as otherwise the cables could act like antennae.
y
Route motor cables without interruptions (e.g. not via terminals) and lay them by the shortest
route out of the switch cabinet.
y
If a motor contactor or a motor choke is used, the component should be positioned directly at the
servo drive and the shielding on the motor cable should not be stripped back too far.
y
Avoid unnecessary cable lengths and "loops of spare cable".
y
Route long cables in places not be susceptible to interference. Otherwise coupling points may be
created.
y
Twist wires for the same electrical circuit.
y
Ideally, route the signal cables separated from encoder cables.
y
All signal cables should be combined and routed away upward.
y
Avoid extending cables via terminals.
Summary of Contents for G305-170
Page 1: ...moog AC AC Servo Drive Single axis System 4 A to 450 A MSD Servo Drive Operation Manual...
Page 6: ...6 MSD Single Axis System Operation Manual AC AC Servo Drive ID no CA65642 001 06 2018 moog...
Page 82: ...82 MSD Single Axis System Operation Manual AC AC Servo Drive ID no CA65642 001 06 2018 moog...
Page 88: ...88 MSD Single Axis System Operation Manual AC AC Servo Drive ID no CA65642 001 06 2018 moog...
Page 89: ...89 MSD Single Axis System Operation Manual AC AC Servo Drive ID no CA65642 001 06 2018 moog...