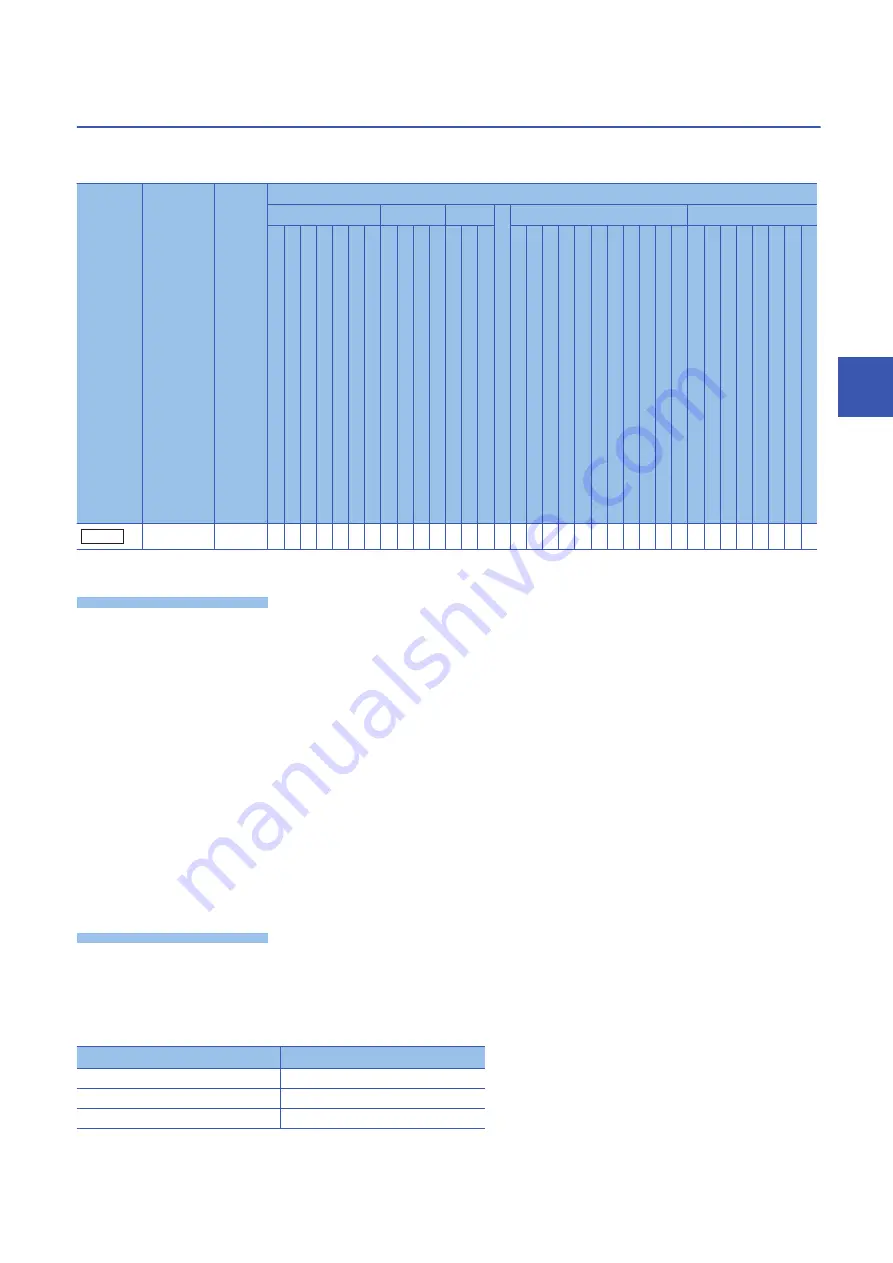
5 POSITIONING CONTROL
5.22 Current Value Change
413
5
5.22
Current Value Change
The current value of the specified servo motor/command generation axis is changed.
: Must be set,
: Set if required
*1 Only when the reference axis speed is specified
Processing details
• Executing the CHGA instruction changes the current value in the following procedure.
1.
The "[St.1040] Start accept flag (R: n/Q: M2001+n)" corresponding to the specified axis is turned on. For the
command generation axis, "[St.345] Command generation axis start accept flag (R: 32n/Q: M9810+20n)"
corresponding to the specified axis is turned on.
2.
The feed current value of the specified axis is changed to the specified address. In this case, the servo motor (output
axis) does not move.
3.
Start accept flag is turned off at completion of the feed current value change.
• When the servo program is not assigned to the command generation axis program, the operation is as follows.
• When the servo program is assigned to the command generation axis program, a current value change is performed for the
specified command generation axis.
Program example
A program for performing the current value change control of Axis 2 is explained as an example.
This program example is explained in the "Q series Motion compatible device assignment" device assignment method.
■
The current value change control conditions
• The current value change control conditions are shown below.
• Start command of current value change control: Leading edge of X0 (OFF
ON)
• The current value of the specified servo motor axis is changed.
• The address which made the current value change by CHGA instruction is valid on the power supply turning on
• The feed current value that is restored after the Multiple CPU system power supply or the control circuit power supply of the servo amplifier is turned ON
again, is returned to the state before the performing of the current value change by the CHGA instruction.
Items
Setting value
Servo program No.
10
Control axis No.
2
Current value change address
50
Positioning data set in servo instructions
Common
Servo
instruction
Positioning
method
Number
of
control
axes
Arc
OSC
Parameter block
Others
Parameter block No.
Acceleration time
Deceleration time
Rapid Stop deceleration time
Torque limit value
Deceleration processing on stop input
Allowable error range for circular interpolation
S-curve ratio
Advanced S-curve acceleration/deceleration
Bias speed at start
Repeat condition
Program No.
Command speed (Continuous trajectory)
Skip
FIN acceleration/deceleration
WAIT-ON/OFF
Fixed position stop
Axis
Address/travel value
Command speed
Dwell time
M-code
Torque limit value
Auxiliary point
Radius
Central point
Number of pitches
Starting angle
Amplitude
Frequency
Interpolation control unit
Speed limit value
Reference axis No.
*1
Fixed position stop acceleration/deceleration time
CHGA
Absolute
1
¨ ¨
Summary of Contents for MELSEC iQ-R16MTCPU
Page 2: ......
Page 477: ...APPENDICES Appendix 1 Processing Times of the Motion CPU 475 A MEMO ...
Page 481: ......