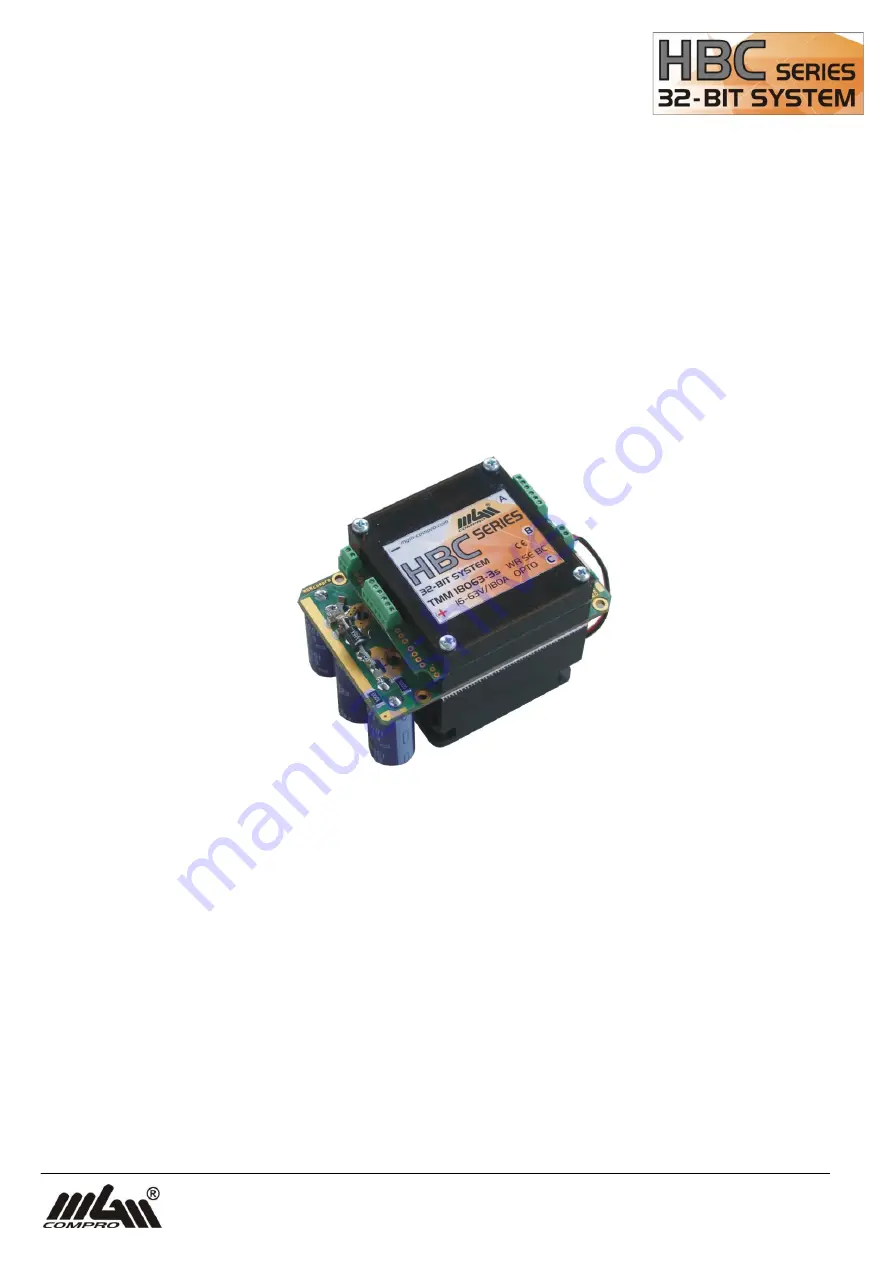
HBC-series - page 1 / 72
HBC - SERIES V7
18063-3 / 25063-3 / 100120-3 / 140120-3
L
ow
V
oltage (63V) +
M
edium
V
oltage (120V)
Programmable brushless controllers for industry using
Operating Manual
– firmware version 3.8 or higher
Development, manufacture,
service:
Tel.: +420 577
001
350
MGM
COMPRO
, Ing. G. Dvorský
E-mail: mgm
@
mgm-compro.cz
Sv. Čecha 593, 760 01 Zlín, Czech Republic
Info: www.mgm-compro.com