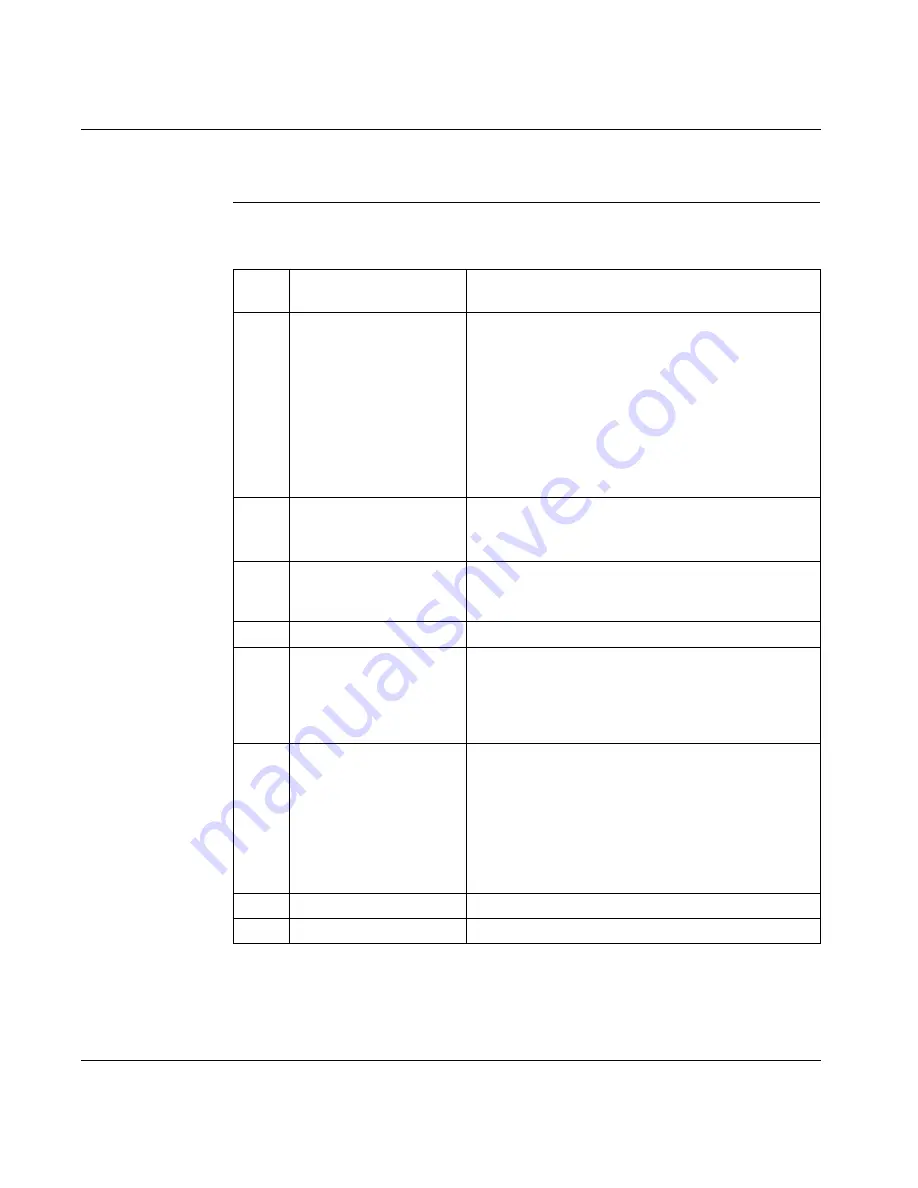
103
Error Messages, continued
Error
Identification
and Description,
continued
Error
Code
Error (Fault)
Possible Cause/Corrective Action
F14
Drive output stage fault.
- Check motor cable for damage or shorts.
- Output module is overheated; improve ventilation.
- Short-circuit or short to ground in the external Regen
resistor.
- Motor has short-circuit/ground short; replace motor.
- Output stage is faulty; return drive to manufacturer.
F15
I²t maximum value
exceeded.
- I
rms
or I
peak
set incorrectly.
- Reduce motion profile duty cycle.
F16*
Mains supply missing two
or three phases.
- Check mains fuses.
- Check mains wiring and connections on drive.
F17
A/D converter error.
Return drive to manufacturer
F18
Regen circuit faulty or
incorrect setting.
- Check jumper on X8 if using internal regen resitor.
- Check wiring of external regen resistor if used.
- Check fuses of external regen resistor.
F19*
Mains supply missing one
phase.
- For single phase operation, set “Phase Missing”
parameter to “no message”.
- Check mains supply fuses.
- Check mains connector on drive.
- Check mains supply wiring.
F20
Slot fault
Hardware fault of the expansion card
F21
Handling fault
Software fault of the expansion card
Summary of Contents for MHDA1004
Page 1: ...Version 2 0 June 2003 31001643_K01_000_04 Lexium Servo Drive 17D Series User Guide...
Page 2: ......
Page 4: ...Preface iv 890 USE 120 00...
Page 14: ...Contents xiv 890 USE 120 00...
Page 28: ...14...
Page 46: ...32...
Page 56: ...42...
Page 112: ...Chapter 5 System Operation 98 890 USE 120 00...
Page 130: ...116 Continued on next page...
Page 148: ...134...
Page 172: ...158...
Page 198: ...184...
Page 204: ...Index 190 890 USE 120 00...