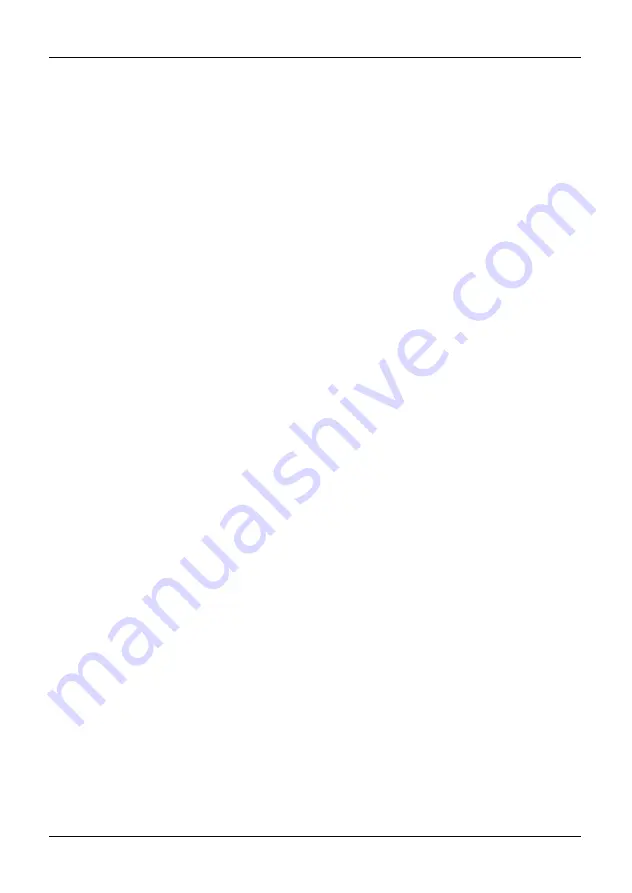
Preface
1
Preface
Thank you for buying AS600M series driver made by ShenZhen ALPHA Inverter
Co.,Ltd.
This series of drivers adopt the closed-loop vector control technology that features
precision speed control, high torque at low frequency and load capacity strongly. The
revised weak magnetic algorithm makes the divers have qucik reponse on high speed
area with the great load inertia, which can provide high-performance speed and
position servo function for your equipments.Its powerful function and simple operation
are easy to achieve the high precision turning,milling,spindle position control,
rigidity
tapping,
thread cutting and so on.
This series of drivers have wide speed range, quick response
,
high torque at low
frequency and position tracking. They apply to most motor drive applications,
including the numerical control lathe, processing center, CNC milling machine, CNC
boring machine, and other fields such as textile industry, plastic industry, carton
packaging industry, woodworking machinery and so on.
If you have any problem that can’t be solved in operation, please contact the nearest
local agents, or contact our company directly.
The instruction manual must be made avaible to the user. Prior to performing any work
on the unit the user must familiarize himself with the unit. This especially applies to the
knowledge and observance of the following safety and warning indications. The used
pictograms have following significance.
Summary of Contents for AS600M Series
Page 96: ...96 ...