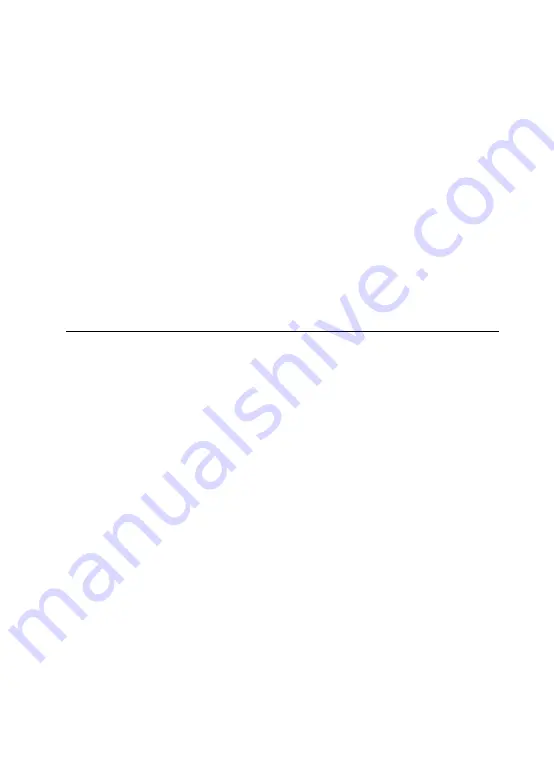
SVF-MN Series Mini Type Sensorless
Vector Frequency Inverter
Operation Manual
Material Version
:
V1.4
Date of Filing
:
2014-10-24
Company Standard
:
Q/0300SSC 001-2012
Shandong Shenchuan Drive Technology CO., LTD. could
supply all-round technology support for clients. The users
could contact the nearby agency or customer service center
of Shandong Shenchuan Drive Technology CO., LTD, and also
could contact the manufacturer directly.
All rights reserved. Any alteration is made without notice.
Head office: Shandong Shenchuan Drive Technology CO., LTD.
Customer hotline: 86-533-6285662
Service hotline: 86-13375338006 or 86-13375338007
URL: www.chinsc.com
E-mail: [email protected]