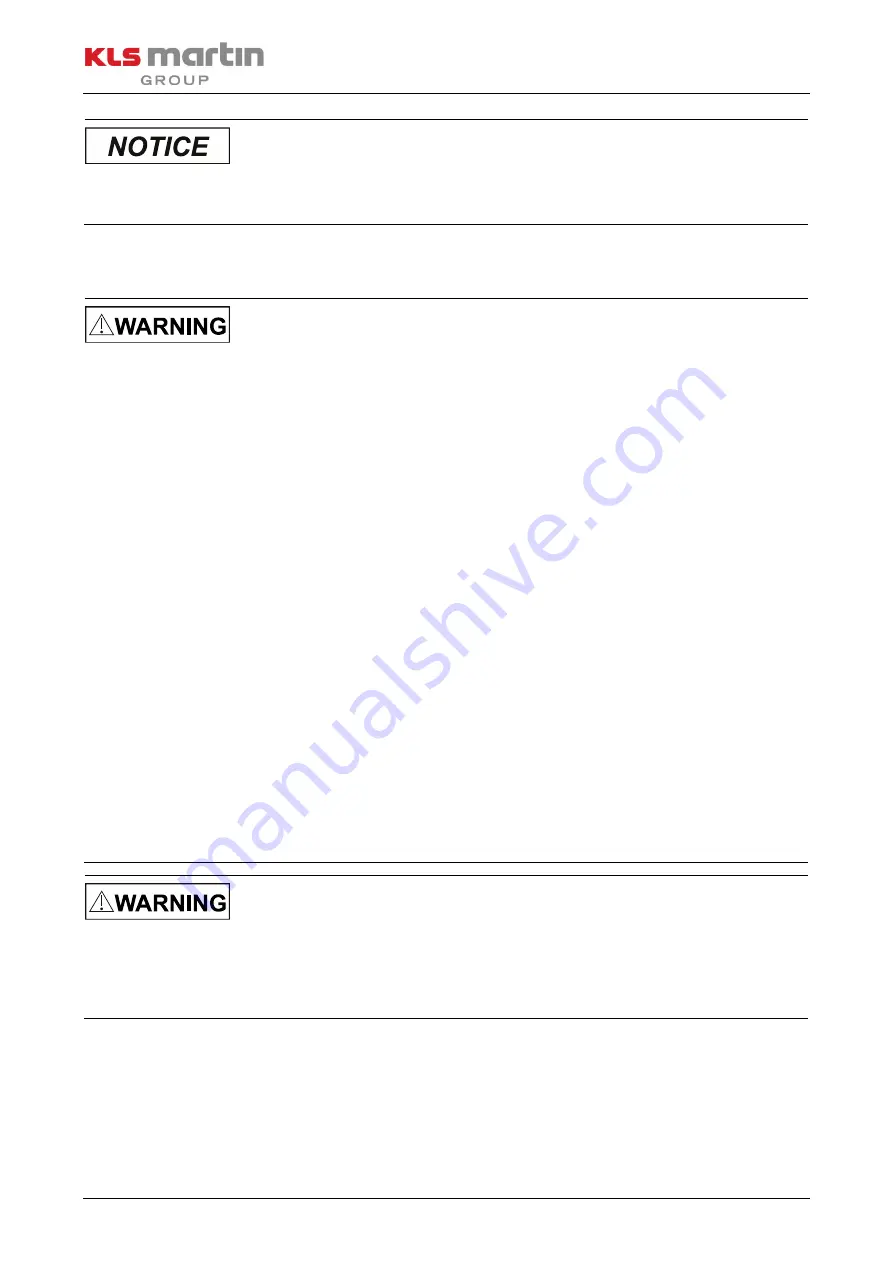
14
Only components or systems approved as accessories by Gebrüder Martin may be attached, installed or
fixed to the lighting systems.
3.2
Personal Protection
Danger of serious injury from electric shock!
•
Before starting any servicing work, verify that all power supply lines are off-circuit and cannot be
energized while working on the light!
•
The building installation must include a disconnector (e.g. circuit breaker) allowing all-pole and
simultaneous disconnection of all electric circuits of the light (100–240 V mains supply, 24–36 V direct
voltage supply) from the power source to which the light is connected. The switch or circuit breaker
used must comply with IEC 61058-1 requirements regarding creepage distances and clearances or must
be UL-listed.
•
To prevent any risk of electric shock, be sure to connect the lights only to power supply systems
providing protective grounding.
•
For mobile lights with detachable mains plug (power supply cable), free access to the socket-outlet
must be possible at any time to ensure that the light can be easily disconnected from the power
supply.
•
The DC voltage supply of the light must meet the requirements of safety extra-low voltage (SELV)
according to IEC 60601-1.
•
Be sure to switch off the building-side circuit breaker before performing any servicing work on the light
system!
•
The mains connecting wires must be protected against accidental loosening or fracture at the terminal
(strain relief)!
Danger of serious injury from defective lights!
Defective operating lights can damage the health or even threaten the lives of users and/or patients!
•
Therefore, never operate defective lights!