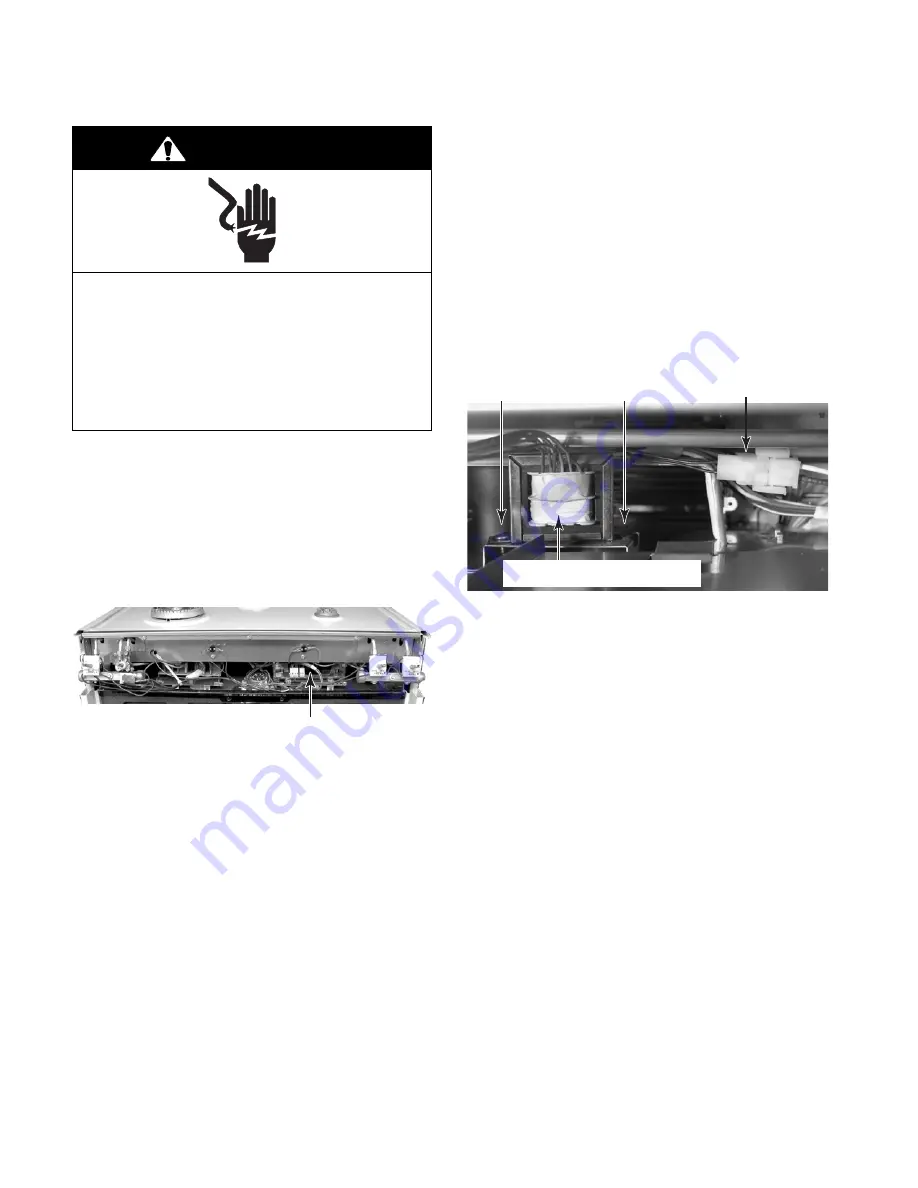
4-8
REMOVING THE POWER SUPPLY TRANSFORMER
1.
Unplug range or disconnect power.
2.
Turn off gas supply to range.
3.
Remove the control panel (see step 4 on
page 4-2 for the procedure).
4.
Remove the control power supply (see
step 7 on page 4-7 for the procedure).
Electrical Shock Hazard
Disconnect power before servicing.
Replace all parts and panels before
operating.
Failure to do so can result in death or
electrical shock.
WARNING
5.
Using a 90
°
offset screwdriver, remove
the screw from the power supply trans-
former.
6.
Disconnect the 2-wire primary wire con-
nector on the power supply transformer
from the wiring harness. Cut the wire tie
from around the primary wires.
7.
Unhook the flange on the end of the power
supply transformer from the mounting
bracket slot, and remove the transformer
from the front of the unit.
Power Supply Transformer
(Behind Control Power Supply)
Screw
Power Supply Transformer
Flange In Slot
Primary Connector
Summary of Contents for KGRA806P
Page 12: ...1 8 NOTES ...
Page 24: ...2 12 NOTES ...
Page 26: ...3 2 NOTES ...
Page 56: ...4 30 NOTES ...
Page 65: ...5 9 Display Board Connector Pinouts Low Voltage Transformer ...
Page 66: ...5 10 Power Board ...
Page 68: ...5 12 Low Voltage Transformer Display Board Connector Pinouts ...
Page 69: ...5 13 Power Board ...
Page 70: ...5 14 NOTES ...
Page 82: ...7 6 NOTES ...
Page 84: ......