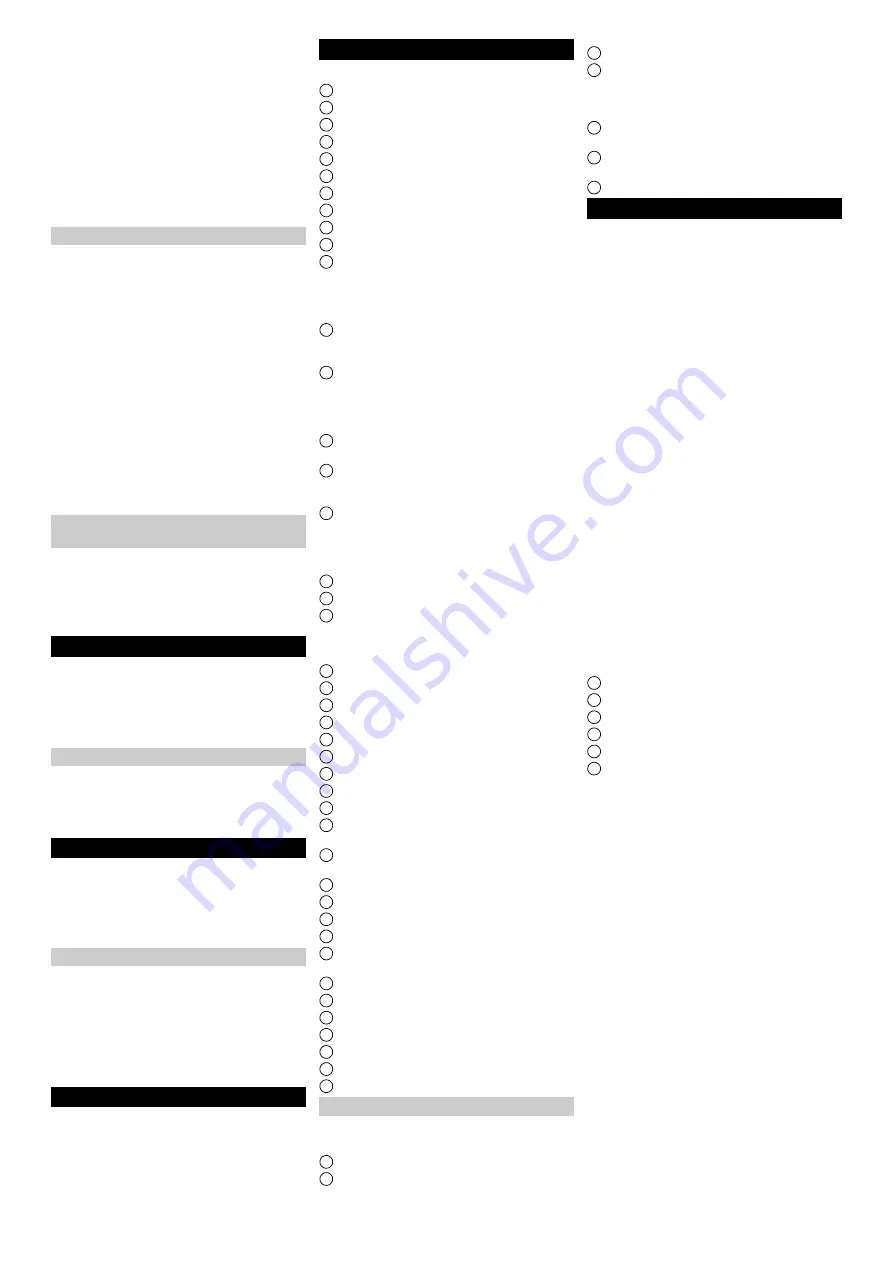
English
13
valve before unscrewing the extraction de-
vice. The gas bottle still has considerable
residual pressure.
Before returning it, screw the locking nut and
the protective cover onto the gas bottle.
If the gas escapes uncontrolled, close the
bottle valve. If the gas emission cannot be
stopped, take the bottle outside or leave the
room, lock the access and only enter and
ventilate the room if a concentration meas-
urement rules out a danger.
Regulations and guidelines
In the Federal Republic of Germany, the fol-
lowing regulations and guidelines apply to
the operation of this system (available from
Carl Heymanns Verlag KG, Luxemburger
Straße 449, 50939 Cologne):
●
DGUV R 100-500 Working with blasting
machines
●
DGUV 113-004 Working in confined
spaces
●
DGUV 113-004 Use of protective cloth-
ing
●
DGUV 113-004 Use of protective gloves
●
DGUV 113-004 Working with jet units
●
DGUV 213-056 Gas warning unit
●
VDMA 24389 Systems for dry ice jet -
safety requirements
Switching off in the event of an
emergency
1. Release the trigger of the jet gun.
2. Turn the program switch to "0/OFF".
3. Close the stop valve on the carbon diox-
ide bottle.
4. Shut off the compressed air supply.
Safety devices
몇
CAUTION
Missing or modified safety devices
Safety devices are provided for your own
protection.
Never modify or bypass safety devices.
Safety lever
The safety lever prevents unintentional ac-
tivation of the jet gun.
The trigger can only be operated when the
safety lever has been raised beforehand.
Accessories and spare parts
Only use original accessories and original
spare parts. They ensure that the appliance
will run fault-free and safely.
Information on accessories and spare parts
can be found at
www.kaercher.com
.
Protective clothing
Full-view safety goggles, anti-fog, part no .:
6.321-208.0
Cold protection gloves with anti-slip profile,
category III according to EN 511, part no .:
6.321-210.0
Hearing protection with headband, part no
.: 6.321-207.0
Scope of delivery
Check the contents for completeness when
unpacking. If any accessories are missing
or in the event of any shipping damage,
please notify your dealer.
Control elements
Illustration A
1
Steering roller with parking brake
2
Abrasive hose coupling
3
Control cable coupling
4
Control panel
5
Push handle
6
Holder for jet gun
7
Storage area
8
Nozzle holder
9
Display
10
Program switch
11
Fault indication pellet dosing
– Lights up red: The drive motor of the
dosing device is blocked
– Flashes red: The drive motor of the
dosing device is overheated
12
Fault indication pellet generation
– Lights up red: The drive motor for pel-
let production is blocked
13
Compressed air supply fault indicator
– Lights up red: Compressed air supply
has too little pressure
– Flashes red: The internal pressure is
too high
14
Voltage supply indicator lamp
– Lights up green: Voltage supply OK
15
Compressed air indicator light
– Lights up green: Compressed air sup-
ply OK.
16
Jet gun fault indicator
– Lights up yellow: The trigger is fas-
tened (e.g. cable tie)
– Flashes yellow: no jet gun connected
to the device
17
Jet nozzle
18
Jet gun
19
Compressed air / pellets button with in-
dicator light
– Lights up red: Compressed air jet
– Off: Pellet jet
20
Trigger
21
Safety lever
22
Retaining cone
23
Abrasive hose
24
Bottle connection
25
Screw plug
26
Copper sealing ring
27
Carbon dioxide filter
28
Screw flange
29
Bottle connection seal (order number
6.574-316.0)
30
Carbon dioxide immersion pipe bottle
(not included in the scope of delivery)
31
Carbon dioxide hose
32
Carbon dioxide bottle retaining belt
33
Homebase retaining rail
34
Hose/cable holder with rubber tensioner
35
Opening for resetting the motor circuit
breaker
36
Handle
37
Compressed air connection
38
Storage space for carbon dioxide bottle
39
Carbon dioxide exhaust hose
40
Mains connection cable with mains plug
41
Holder for abrasive hose
42
Drain tap for condensation water
Display
Program switch at level 1 ... 3:
Illustration B
1
Jet pressure
2
Total operating time
3
Customer Service visit is due
4
Blasting jet time since last reset
Program switch in the reset position:
Illustration C
1
To reset the jet time, press the com-
pressed air / pellets button
2
Period of time until the next Customer
Service visit
3
Blasting jet time since last reset
Initial startup
DANGER
Risk of injury
Dry ice pellets can escape from damaged
components and cause injuries.
Before initial startup, check all components
of the device, especially the abrasive hose,
to ensure that they are in good condition.
Replace damaged assemblies with flaw-
less ones. Clean soiled assemblies and
check that they are working properly.
ATTENTION
Risk of damage
Condensation water can drip from the de-
vice casing onto the floor.
Do not operate the device on surfaces that
are sensitive to moisture.
1. Open the drain tap and drain the con-
densation water that has collected in the
device.
2. Close the drain tap.
3. Store the device on a level and flat sur-
face.
4. Block the steering rollers with the park-
ing brakes.
5. Connect the abrasive hose to the cou-
pling on the device.
Illustration H
1
Control cable
2
Union nut
3
Control cable coupling
4
Abrasive hose coupling
5
Union nut
6
Abrasive hose
6. Unscrew the union nut of the abrasive
hose and slightly tighten it with an open-
end wrench.
7. Plug the control cable into the device.
8. Screw on the union nut of the control ca-
ble and tighten by hand.
9. Insert the jet gun with the retaining cone
into the holder on the device.
DANGER
Risk of asphyxiation
Carbon dioxide escapes from the exhaust
hose. From a concentration of 8 percent by
volume in the breath, carbon dioxide leads
to unconsciousness, respiratory arrest and
death. The maximum workplace concentra-
tion is 0.5%. Carbon dioxide is heavier than
air and collects in pits, basements and de-
pressions.
Lay the exhaust hose so that nobody is en-
dangered by the escaping carbon dioxide.
Note:
Carbon dioxide is heavier than air.
Make sure that carbon dioxide does sink to
lower-lying areas, for example by flowing
Summary of Contents for IB 10/8 L2P
Page 2: ...A...
Page 3: ...B C D E F G H I J K L M N O P...
Page 85: ...85 300 m 3 5 7 10 K RCHER 79 C EN 511 Pellet...
Page 90: ...90 K RCHER 1 2 100 1 500 1 2 1 2 DGUV R 100 500 1 1 1 N 1 2 3 4 K rcher...
Page 100: ...100 10 300 3 5 7 10 K RCHER 79 C EN 511...
Page 105: ...105 L 1 2 3 4 10 11 12 13 1 2 3 4 2 5 M K RCHER 1 2 100 1 500 1 2 1 2 DGUV R 100 500 1 1 1...
Page 106: ...106 N 1 2 3 4 K rcher 1 O 31 C a b 30 c d...
Page 172: ...172 K RCHER 1 2 100 1 500 1 2 1 2 DGUV R 100 500 1 1 1 N 1 2 3 4 K rcher...
Page 173: ...173 1 O 1 2 1 3 4 P 1 2 3 4 5 6 7 8 9 80 Nm ABS 2 574 006 0 31 C a b 30 c d...
Page 196: ...196 REACH www kaercher com REACH 10 300 3 5 7 10 K RCHER 79 EN 511...
Page 201: ...201 12 13 1 2 3 4 2 5 M K RCHER 1 2 100 1 500 1 2 1 2 DGUV R 100 500 1 1 1 N 1 2 3 4...
Page 202: ...202 K rcher 1 O 1 2 1 3 4 P 1 2 3 4 5 6 31 C a b 30 c d...
Page 210: ...213 12 13 1 2 3 4 5 M K RCHER 1 2 100 1 500 1 1 2 DGUV R 100 500 1 1 1 N 1 2 3 4 K rcher...
Page 215: ......