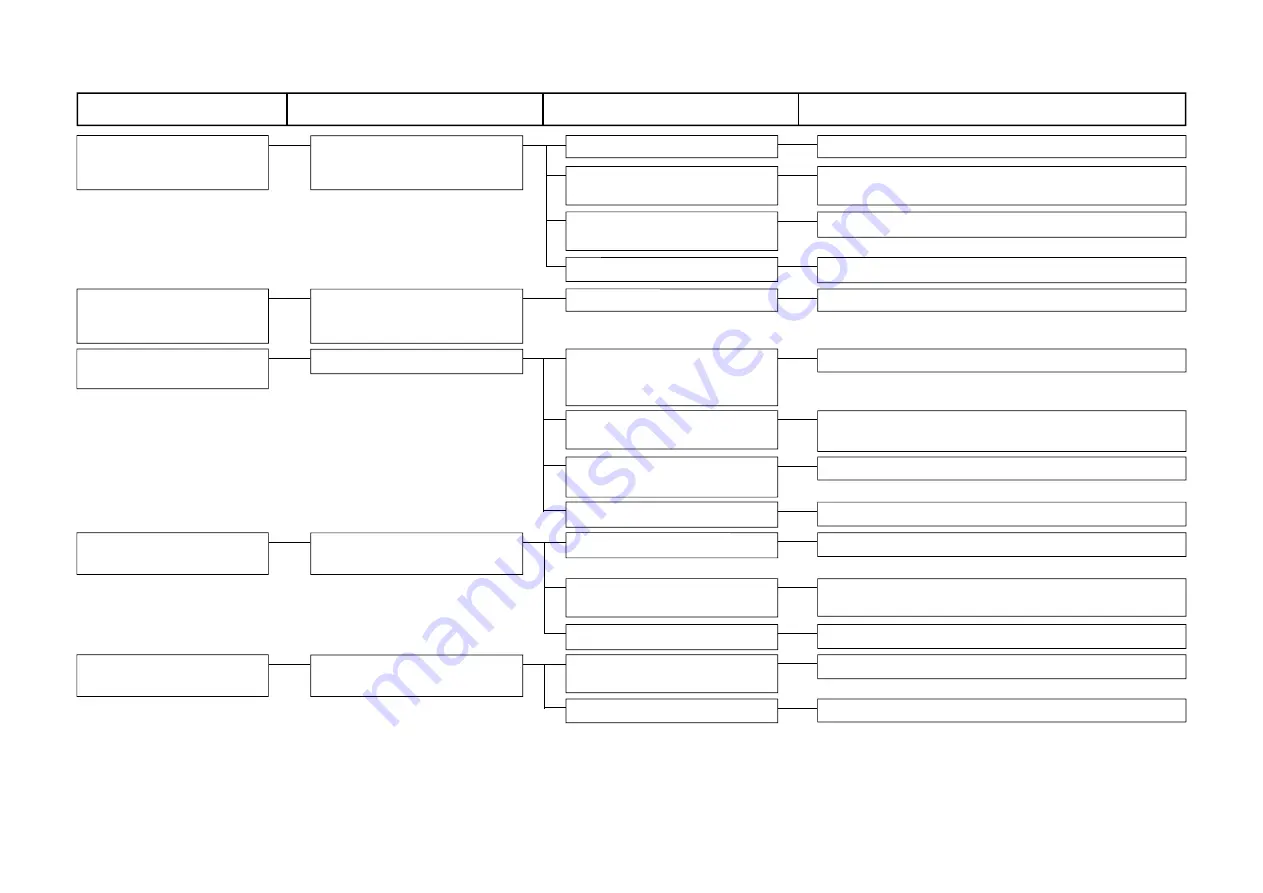
– 146 –
3) Sewing
1. E023 (Detection of step-out
1-1) Step-out of motor is
1-A) Presser motor stepped out.
Check presser lifter.
of presser lifting motor error)
detected when passing
is displayed.
presser lifting origin sensor.
1-B) Signal from presser lifting
Check connection or breaking of wire of presser lifting
origin sensor does not come.
origin sensor and MAIN-INT cord C asm.
1-C) Presser lifting origin sensor
Replace presser lifting origin sensor.
is broken.
1-D) MAIN p.c.b. is broken down.
Replace MAIN p.c.b.
2. E030 (Needle bar upper
2-1) Needle bar does not stop at
1-A) Load is heavy.
Remove the cause.
position failure) is
needle UP position at the
displayed.
time of needle UP operation.
3. E031 (Air pressure drop) is
3-1) Air pressure drop is detected.
1-A) Air pressure is too low or
Check open/close of air valve and air piping, or compressor.
displayed.
supply capacity of
compressor is too low.
1-B) Signal from pressure gauge
Check connection or breaking of wire of pressure gauge
does not come.
relay cord asm.
1-C) Setting of pressure gauge is
Adjust setting of pressure gauge (0.5 MPa).
too high.
1-D) Pressure gauge is broken.
Replace pressure gauge.
4. E050 (Stop switch) is
4-1) Stop switch is detected
1-A) Stop switch is pressed.
Release with reset key on the panel.
displayed
during machine running.
1-B) Signal from stop switch does
Check connection or breaking of wire of stop switch relay
not come.
cord asm.
1-C) Stop switch is broken.
Replace stop switch.
5. E098 (Needle bar down
5-1) Needle bar cannot be
1-A) Load of the machine is too
Check the sewing machine.
error) is displayed.
lowered.
heavy.
1-B) SDC p.c.b. is broken down.
Replace SDC p.c.b.
Trouble
Cause (1)
Cause (2)
Inspecting order and adjusting procedure
Summary of Contents for AMB-289
Page 11: ...7 MEMO...
Page 16: ...12 5 Wiper adjustment Wiper components 3 to 5mm 6 to 8mm Standard Adjustment...
Page 18: ...14 6 Adjusting the face plate thread tension A 12mm Standard Adjustment...
Page 22: ...18 8 Adjusting the position of Y top feed motor Standard Adjustment...
Page 24: ...20 9 Adjusting the position of Y bottom feed motor Standard Adjustment...
Page 26: ...22 10 Adjusting the tongue up down cylinder 19mm 5mm Gauge A Standard Adjustment...
Page 30: ...26 12 Adjusting the differential feed X top feed motor 6 0 5mm Align Standard Adjustment...
Page 36: ...32 15 Adjusting the chuck open close cylinder Standard Adjustment 26 0 5mm...
Page 42: ...38 16 Adjusting the respective sensors 3 3 C Standard Adjustment 14 5 0 5mm...
Page 48: ...44 2 Disassembling and assembling of the face plate Procedures of disassembling assembling...
Page 62: ...58 8 Replacing the thread trimmer cylinder 4 5mm Procedures of disassembling assembling...
Page 68: ...64 11 Replacing the thread drawing motor A B C C Procedures of disassembling assembling...
Page 70: ...66 12 Replacing the loader motor Procedures of disassembling assembling...
Page 81: ...77 MEMO...
Page 172: ...168 MEMO...
Page 176: ...172 MEMO...