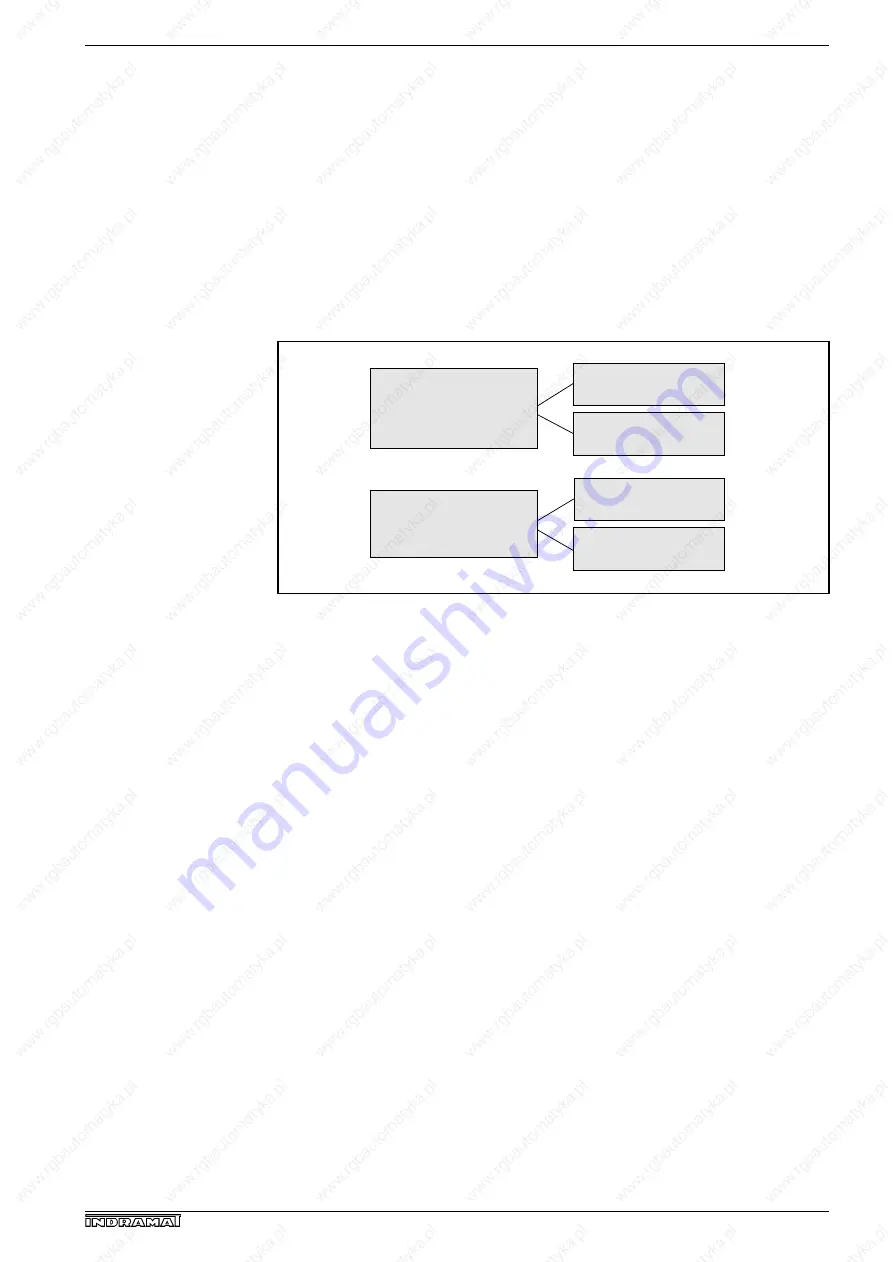
35
• DOK-POWER*-TVD*1.3****-ANW1-EN-E1,44 • 02.97
4. TVD 1.3 Interconnections
4.
TVD 1.3 Interconnections
The interconnections for mains and the DC bus of the TVD recommended by
INDRAMAT illustrate the operating principles of the unit. This section outlines
several interconnect configurations. Just which configuration is selected
depends on the functions and the sequence of actions required for the entire
machine and is the responsibility of the machine builder.
4.1. Optional Control Possibilities
by the NC control
unit
by the electronics
of the drive
controlled braking
with an E-stop or a
power failure
braking the
drives with faulty
drive electronics
without DC bus
dynamic braking
with DC bus
dynamic braking
Fig. 4.1: Optional control possibilities
The DC bus is short-circuited for braking the drives to a standstill as an
additional safety precaution if there is ever a fault in the drive electronics.
With DC bus dynamic braking, synchronous motors are always braked to a
standstill regardless of whether the drive electronics are functional or not.
Without DC bus dynamic braking, synchronous motors can not be braked with
faulty drive electronics.
Asynchronous motors cannot be braked if the DC bus is short-circuited!
Drives are generally brought to a standstill by the drive control with an E-stop
or mains failure.
In the event of an E-stop or if the drive-internal monitors are tripped, then drive
control switches to zero command value and there is a regulated braking of the
drives at maximum torque.
In some cases (e.g., electronically coupled tooth gear machines), it may be
necessary for the CNC to bring the drives to a standstill in an E-stop situation
or a mains failure.
There is then a regulated braking of the drives by the NC control unit with an
E-stop or if the drive-internal monitors are tripped.
Stopping the drives with
faulty drive electronics
with or without DC
dynamic braking
Braking with an E-stop
or mains failure at
maximum torque by the
drive electronics or in a
position loop by the
NC control unit