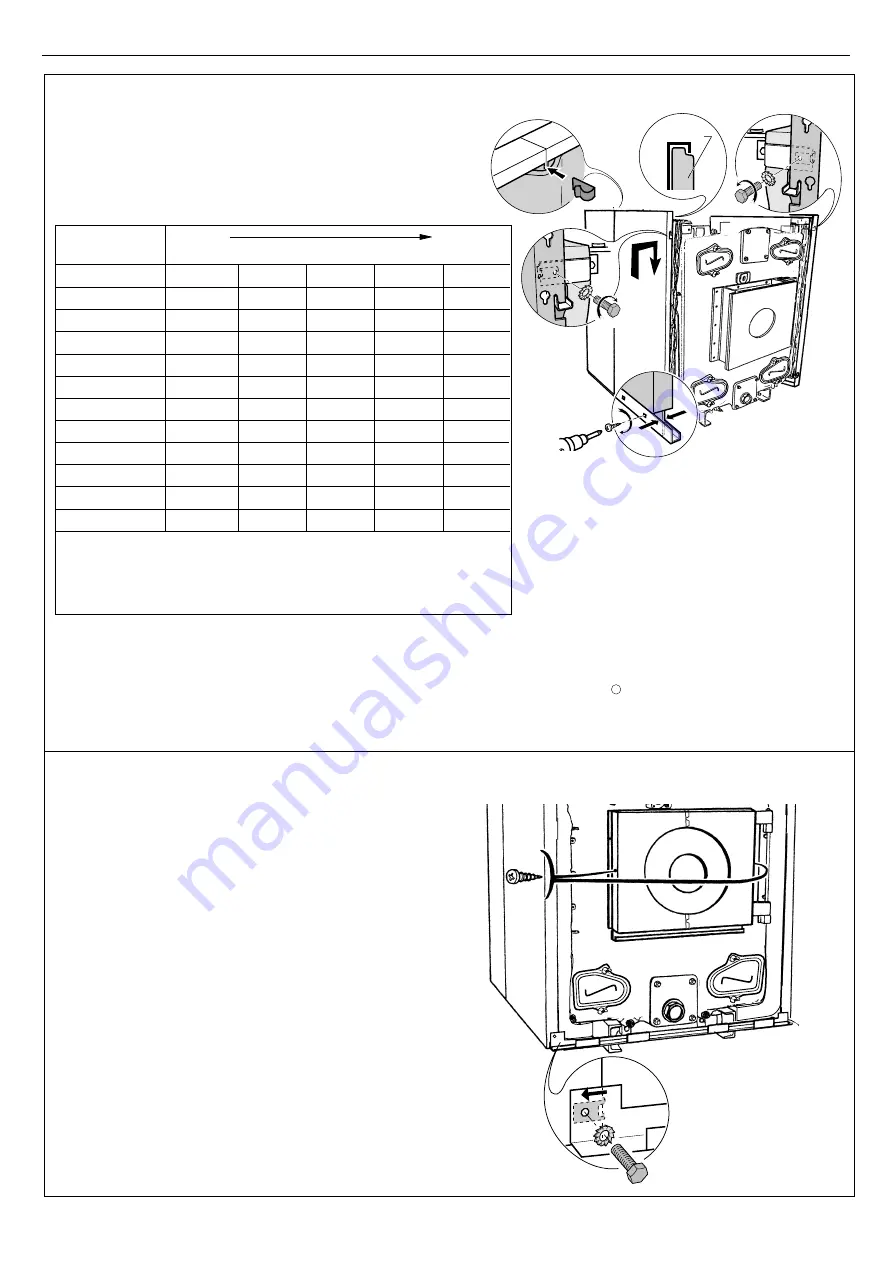
32
Ideal Viscount GTE
- Installation, Assembly & Servicing
1
2
4
5
2
3
VIS5114
ASSEMBLY
43
Assembling the Side Casing Panels
Length and arrangement of panels for the boiler
model
•
Put the
furnace door panel
in place (package
FA5 or
FA
6) and fasten with two ø 3.94 x 12.7 tapping screws.
The furnace door panel may be cut in two at the micro-
joints.
•
Fit two Rapid nuts in the bottom of the front side panels.
•
Fix
the casing support lower crosspiece
(package
FA5
or FA
6) by means of two H 6x20 screws and two serrated
washers.
•
First assemble the panels on the front
using
the assembly length table opposite and
continue up to the rear section
①
.
•
Fix the front side panels
to the positioning
brackets with H 8 x 16 screws and serrated
washers
②
.
•
Push the insulating material into the top of the
side panels and fasten the panels
③
to the
lower rails by means of the self-tapping screws
with the electric screwdriver (2 screws per
panel) .
•
Fasten the side panels to each other with the
clips
⑤
.
Type of
Boiler
GTE 14
800
600
600
GTE 15
940
600
600
GTE 16
1050
600
600
GTE 17
940
600
400
400
GTE 18
1050
600
400
400
GTE 19
940
600
600
400
GTE 20
940
600
600
600
GTE 21
1050
600
600
600
GTE 22
940
600
600
400
400
GTE 23
1050
600
600
400
400
GTE 24
940
600
600
600
400
GTE 25
1050
600
600
600
400
400 mm long panel in Package FA 10
600 mm long panel in Package FA 11
800 mm long panel in Package FA 7
940 mm long panel in Package FA 8
1050 mm long panel in Package FA 9
Side Panels Length in mm
FRONT
REAR
44
Assembling the Furnace Door and Lower Crosspiece Panels
VIS5115
1
2
4