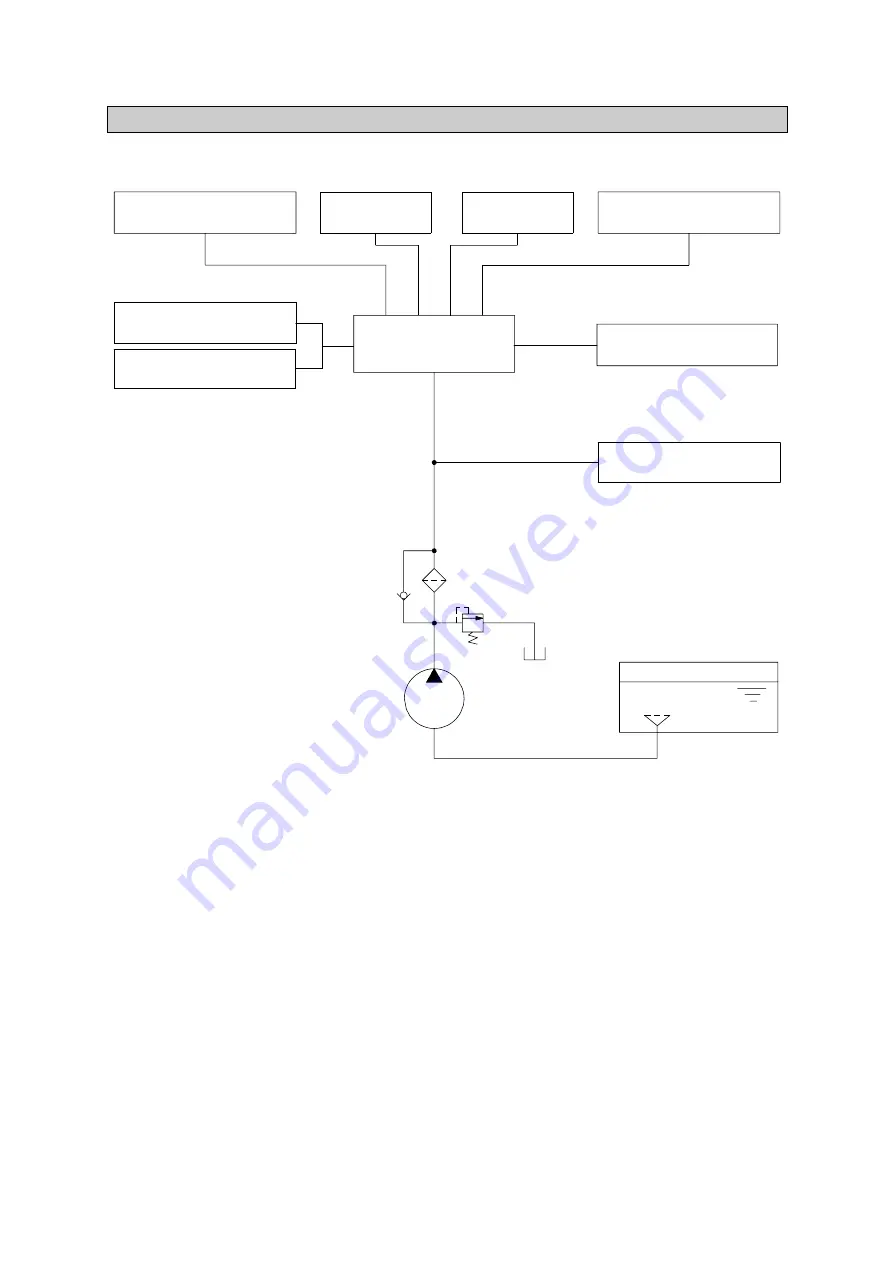
3-5
GROUP 3 PILOT CIRCUIT
The pilot circuit consists of suction circuit, delivery circuit and return circuit.
The pilot pump is provided with relief valve, receives the oil from the hydraulic tank through the suction
filter.
The discharged oil from the pilot pump flows to the remote control valve through line filter, solenoid valve
assemblies, swing parking brake, main control valve and safety lock solenoid valve.
Control valve
Remote control valve
(LH lever)
Travel pedal
RCV dozer
Remote control valve
(RH lever)
Safety lock
solenoid valve
Swing parking brake
Line filter
Relief valve
30kgf/cm
2
Travel speed solenoid valve
Pilot pump
Suction filter
R35Z73HC00
Boom swing pedal