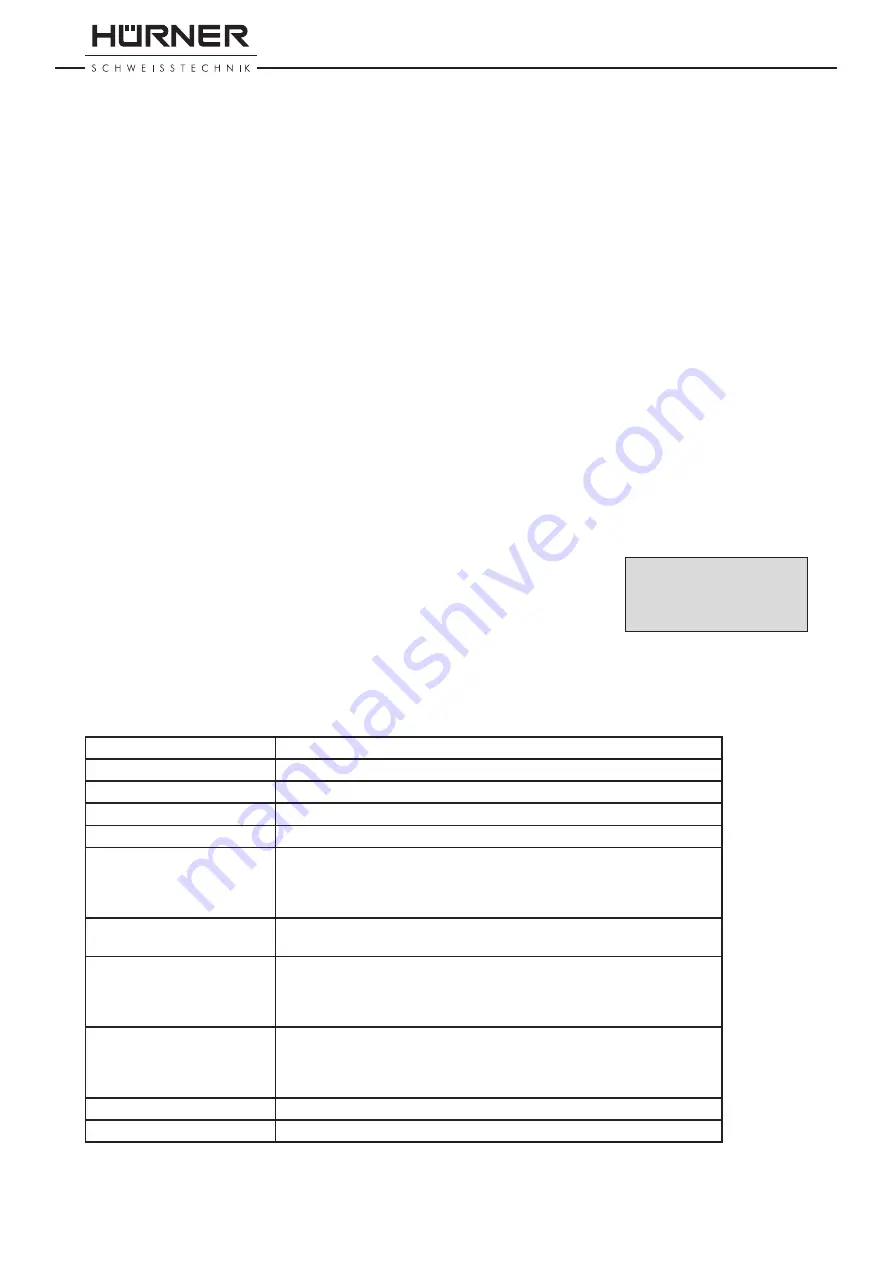
Version January 2019
22
EN
HÜRNER WeldControl 2.0 630 User’s Manual
H Ü R N E R S c h w e i s s t e c h n i k G m b H
Nieder-Ohmener Str. 26
35325 Mücke, Germany
4.4.4 Joining and Cooling Stage
Set the carriage mover lever to its close-in position again in order to
move the pipe butts in on each other and to build the joining pres-
PROBÐ-
5
+ P
t
) according to a consistent increase. Watch the value on
the display screen. Building the joining pressure must correspond to a
linearly increasing ramp and its duration must neither be longer nor
shorter than indicated for your welding situation in the welding value
tables in the Appendix at t
4
.
Once the joining pressure is reached and has stabilized at P
5
+ P
t
ÐQEBÐ
MOBPPROBÐTFIIÐ?BÐHBMQÐ>QÐQEFPÐIBSBIÐRKQFIÐQEBÐBKAÐLCÐQEBÐGLFKFKDÐME>PBÐQ
5
in
QEBÐAF>DO>JÐ&KÐQEFPÐPQ>DB ÐQEBÐKBTÐGLFKQÐ>IPLÐPQ>OQPÐ@LLIFKDÐALTK
Pipe and fitting manufacturers may include data on how long the new
GLFKQÐPELRIAÐKLQÐ?BÐBUMLPBAÐQLÐBUQBOK>IÐPQO>FKÐIPL ÐQEBÐ>MMIF@>?IBÐ
TBIAFKDÐPQ>KA>OAÐJ>VÐOBNRFOBÐ>ÐJFKFJRJÐ@LLILKÐQFJBÐQ
6
in the dia-
DO>JÐ&KÐJLPQÐ@>PBP ÐELTBSBO ÐQ
6
is not relevant to the welder.
4.4.5 End of Welding
The welding is finished at the end of a successful joining and cooling
stage. The welder has to shut the pressure off from the pipes using
either the manual pressure release valve or the START/SET key.
4.5 Aborted Welding Process
&CÐ>KÐBOOLOÐ@LKAFQFLKÐFPÐABQB@QBA ÐQEBÐJ>@EFKBÐ>?LOQPÐQEBÐTBIAFKDÐMOL
-
@BPPÐ>KAÐAFPMI>VPÐQEBÐBOOLOÐ%LTBSBO ÐQEFPÐFPÐLKIVÐMLPPF?IBÐTEBKÐTBIAFKDÐ
according to the WeldControl mode of the butt-welding process. In
QEBÐ*>KR>IÐ*LABÐLCÐ?RQQÐTBIAFKD ÐBOOLOÐABQB@QFLKÐFPÐKLQÐ>S>FI>?IB
1EBÐBOOLOÐQE>QÐJ>ABÐQEBÐTBIAFKDÐ>?LOQÐFPÐAFPMI>VBAÐLKÐQEBÐP@OBBKÐPBBÐ
!FPMI>VÐÐAAFQFLK>IIV ÐFKÐQEBÐTBIAFKDÐAF>DO>JÐQEBÐ)"!ÐQE>QÐ?BILKDPÐ
to the welding stage with the malfunction starts flashing.
The errors listed in the following table can be displayed on the
screen.
Type of Error
Description
a. Data Input
Input Error
Error while entering data with the cursor keys.
Code Error
Error while reading data from a bar code or an RFID card.
b. System and Conditions
System Error
The welding system has to be disconnected immediately from both
the power supply and the fitting. The auto-test has detected an
error in the system. The welder must no longer be operated and has
to be sent to an approved shop for check and repair.
Clock Error
The internal clock of the machine is defective; re-set the clock in the
Configuration Menu.
Unit to Service
The recommended next service date for the welder is overdue. The
service due message has to be acknowledged by pressing the START/
SET key. Send the welding system to the manufacturer or an
approved service point for service and check-up.
Power Supply Failure at Last
Welding
The last welding is incomplete. The welding unit was disconnected
from the power supply voltage while it was in progress. To go on
RPFKDÐQEBÐRKFQ ÐQEFPÐBOOLOÐE>PÐQLÐ?BÐ>@HKLTIBADBAÐ?VÐMOBPPFKDÐQEBÐ
STOP/RESET key.
Ambient Temperature high
Outside temperature outside the range from – 20°C to + 60°C.
Ambient Temperature low
Outside temperature outside the range from – 20°C to + 60°C.
WELDING ABORTED
Error Build-up Pres.
229°C ACT. 1.5bar
Display 32
Summary of Contents for WeldControl 2.0 630
Page 2: ......