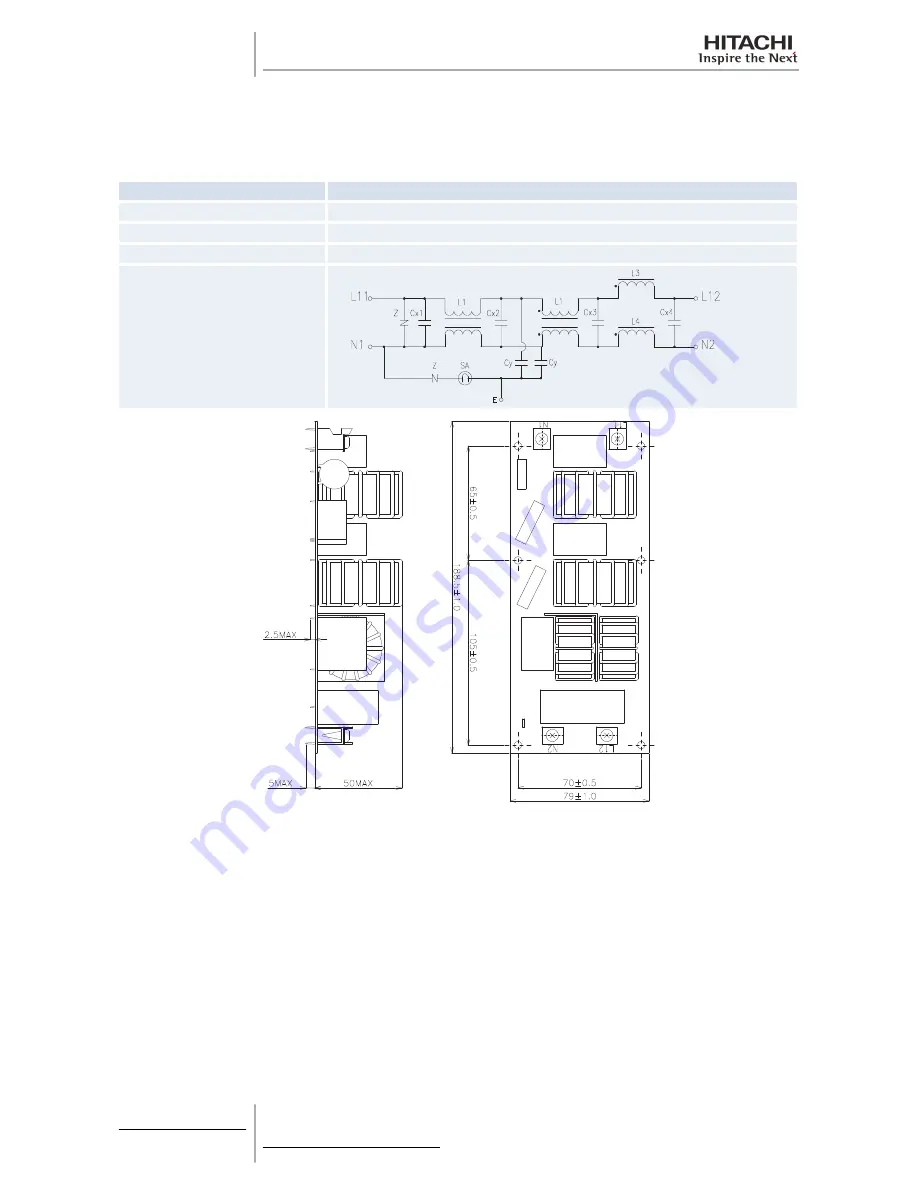
11.5.2 Noise filter for ES Series
The noise filter decreases the leakage of noise made by the inverter to the power supply side. Terminals indicated with
“LOAD” are connected to the inverter side and terminals indicated with “LINE” to the power supply side.
RAS-(4-6)HVRNS1E (230V/50Hz)
Items
Specifications
Model
LFB-14930-3M
Rated current
AC230V 30 A
Permissible temperature range.
-25 ºC to 85 ºC
Circuit diagram
Load
Line
11 Electrical checks of
main parts
450
SMGB0060 rev. 1- 12/2010
Summary of Contents for RAS-10HRNM
Page 2: ......
Page 4: ...Index ii SMGB0060 rev 1 12 2010 ...
Page 56: ...2 Unit Installation 48 SMGB0060 rev 1 12 2010 ...
Page 117: ...RAS 4 6 HVRNM1E 4 Electrical Wiring 109 SMGB0060 rev 1 12 2010 4 ...
Page 118: ...RAS 4 6 HRNM1E 4 Electrical Wiring 110 SMGB0060 rev 1 12 2010 ...
Page 121: ...RAS 3HVRNS 4 Electrical Wiring 113 SMGB0060 rev 1 12 2010 4 ...
Page 122: ...RAS 4 6 HVRNS1E 4 Electrical Wiring 114 SMGB0060 rev 1 12 2010 ...
Page 123: ...RAS 8 10 HRNSE 4 Electrical Wiring 115 SMGB0060 rev 1 12 2010 4 ...
Page 124: ...4 Electrical Wiring 116 SMGB0060 rev 1 12 2010 ...
Page 145: ...Dry operation Continues in the next page 5 Control System 137 SMGB0060 rev 1 12 2010 5 ...
Page 147: ...Heating operation Continues in the next page 5 Control System 139 SMGB0060 rev 1 12 2010 5 ...
Page 148: ...5 Control System 140 SMGB0060 rev 1 12 2010 ...
Page 153: ...Activation for protection device control 5 Control System 145 SMGB0060 rev 1 12 2010 5 ...
Page 162: ...Activation for protection device control 5 Control System 154 SMGB0060 rev 1 12 2010 ...
Page 166: ...Preheating control of compressor 5 Control System 158 SMGB0060 rev 1 12 2010 ...
Page 168: ...5 Control System 160 SMGB0060 rev 1 12 2010 ...
Page 180: ...6 Optional functions 172 SMGB0060 rev 1 12 2010 ...
Page 224: ...8 Troubleshooting 216 SMGB0060 rev 1 12 2010 ...
Page 263: ...RAS 4 6 HVRNS1E 8 Troubleshooting 255 SMGB0060 rev 1 12 2010 8 ...
Page 264: ...RAS 8 10 HRNSE 8 Troubleshooting 256 SMGB0060 rev 1 12 2010 ...
Page 269: ...RAS 8 10 HRNSE 8 Troubleshooting 261 SMGB0060 rev 1 12 2010 8 ...
Page 337: ...RAS 4 6 HVRNM1E Cycle and structural parts 9 Spare Parts 329 SMGB0060 rev 1 12 2010 9 ...
Page 340: ...RAS 4 6 HRNM1E Cycle and structural parts 9 Spare Parts 332 SMGB0060 rev 1 12 2010 ...
Page 342: ... Electrical parts 9 Spare Parts 334 SMGB0060 rev 1 12 2010 ...
Page 354: ... Electrical parts 9 Spare Parts 346 SMGB0060 rev 1 12 2010 ...
Page 356: ...RAS 8 10 HRNSE Cycle and structural 9 Spare Parts 348 SMGB0060 rev 1 12 2010 ...
Page 359: ... Electrical parts 9 Spare Parts 351 SMGB0060 rev 1 12 2010 9 ...
Page 440: ...10 Servicing 432 SMGB0060 rev 1 12 2010 ...
Page 464: ...11 Electrical checks of main parts 456 SMGB0060 rev 1 12 2010 ...
Page 481: ......