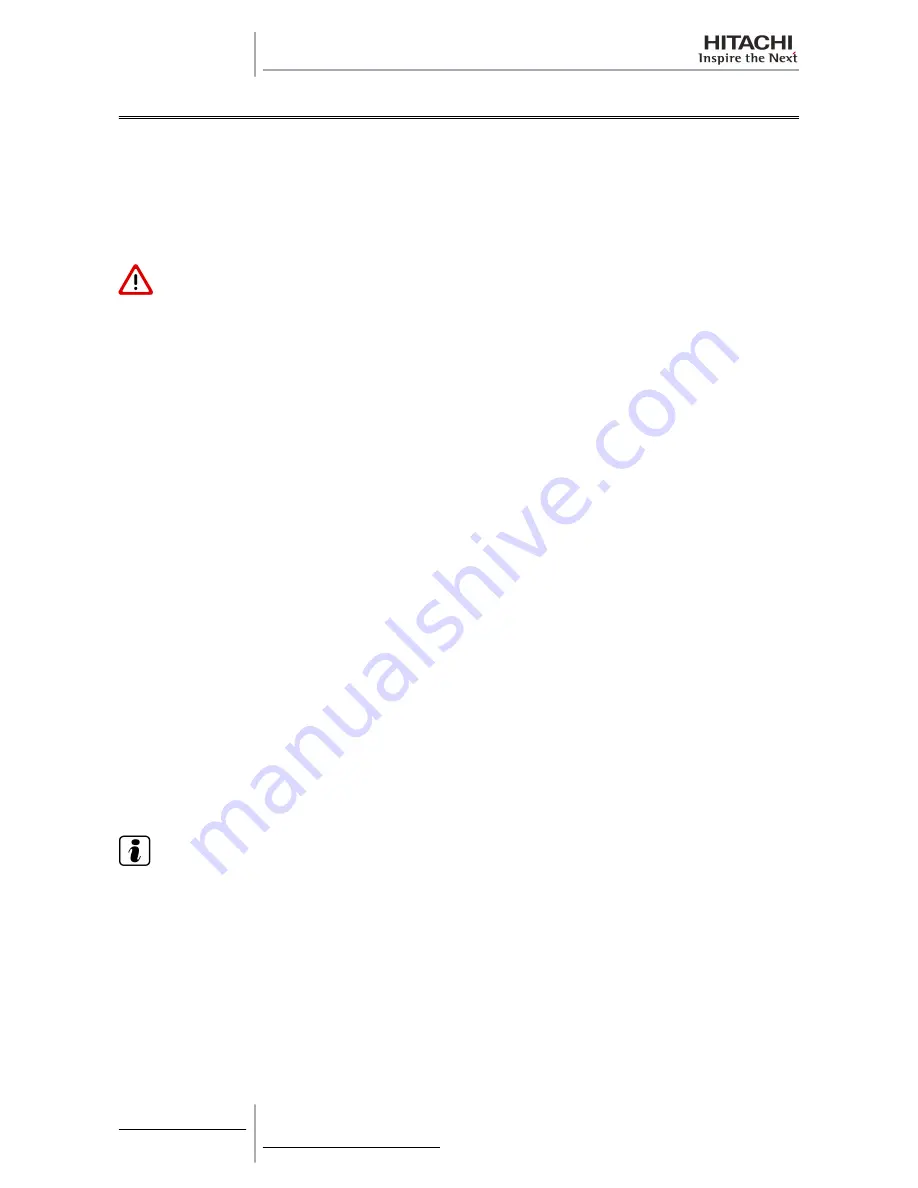
7.1 Checking procedure before the test run
When you have finished the installation, perform the test run according to the following procedure. After performing the test
run, hand over the system to the customer.
Perform the test run of the indoor units one by one in order.
Make sure that the electrical wiring and the refrigerant piping are correctly connected.
Start the indoor units one by one in order to make sure that the indoor units are correctly numbered.
You should perform the test run according to
Test run procedure using the remote control switch
, see on page 176
D A N G E R
•
Do not operate the system until all the check points have been cleared.
– Measure the resistance between the ground and the terminal of the electrical components. Make sure that
the electrical resistance is more than 1 M
Ω
. Otherwise, do not operate the system until you find the electrical
leakage and you repair the electrical leakage. Do not impress the voltage on the terminals for transmission
1 and 2.
– Make sure that the stop valves of the outdoor unit are fully open. Then, start the system.
– Make sure that the switch on the main power source has been ON for more than twelve hours in order to
warm the compressor oil by means of the oil heater.
•
Pay attention to the following items while the system is running.
– Do not touch any of the parts at the discharge gas side with your hands because the compressor chamber
and the pipes at the discharge gas side are hot at a temperature that is higher than 90 °C.
– DO NOT PUSH THE BUTTON OF THE MAGNETIC SWITCH(ES). If you do, you will cause a serious accident.
•
Do not touch any electrical components for more than three minutes after turning OFF the main switch. Make
sure that the stop valve of the gas line and the stop valve of the liquid line are fully open.
Checking procedure
1
Make sure that the stop valve of the gas line and the stop valve of the liquid line are fully open.
2
Make sure that there is no refrigerant leakage. The flare nuts sometimes loosen because of the vibration during the
transportation.
3
Make sure that the refrigerant piping and the electrical wiring belong to the same system Make sure that the setting of
the unit number of DSW1, DSW6 and RSW1 of indoor units correspond to the system.
4
Make sure that the setting of the DIP switches on the printed circuit board of the indoor units and the outdoor units are
correct. Especially, pay attention to the setting of the lift between the indoor units and the outdoor units. Refer to chapter
4 “Electrical Wiring” for details.
5
Make sure that the switch on the main power source has been ON for more than twelve hours in order to warm the
compressor oil by means of the oil heater.
6
Check whether or not the electrical wiring of the indoor units and the outdoor units are connected as shown in chapter
4 “Electrical Wiring”.
7
Make sure that each wire terminal (L1,L2,L3 and N or L1 and N) is correctly connected at the power source.
N O T E
•
Make sure that the field-supplied electrical components (main switch fuse, fuse-free breaker, earth leakage
breaker, wires, conduit connectors and wire terminals) have been properly selected according to the electrical
data in the technical catalogue of the unit. Also, make sure that the field-supplied electrical components comply
with the national codes and the local codes.
•
Use the shielded cables for the field wiring in order to avoid the electrical noise. (The length of the shielded
cable should be less than 1000 m. The size of shielded cable should comply with the local codes).
•
Make sure that the terminals for the power supply wiring (“L1” to “L1” and “N” to “N” of each terminal board
for AC 230 V and the terminals for the intermediate wires between the indoor unit and the outdoor unit
(Operating Line: terminals of each terminal board for DC 12 V) match correctly. Otherwise, you may damage
some components.
•
Check to ensure that the crankcase heater is turned ON for more than 4 hours. The operation is not available
within 4 hours after turning ON the power supply.
7 Test Run
174
SMGB0060 rev. 1- 12/2010
Summary of Contents for RAS-10HRNM
Page 2: ......
Page 4: ...Index ii SMGB0060 rev 1 12 2010 ...
Page 56: ...2 Unit Installation 48 SMGB0060 rev 1 12 2010 ...
Page 117: ...RAS 4 6 HVRNM1E 4 Electrical Wiring 109 SMGB0060 rev 1 12 2010 4 ...
Page 118: ...RAS 4 6 HRNM1E 4 Electrical Wiring 110 SMGB0060 rev 1 12 2010 ...
Page 121: ...RAS 3HVRNS 4 Electrical Wiring 113 SMGB0060 rev 1 12 2010 4 ...
Page 122: ...RAS 4 6 HVRNS1E 4 Electrical Wiring 114 SMGB0060 rev 1 12 2010 ...
Page 123: ...RAS 8 10 HRNSE 4 Electrical Wiring 115 SMGB0060 rev 1 12 2010 4 ...
Page 124: ...4 Electrical Wiring 116 SMGB0060 rev 1 12 2010 ...
Page 145: ...Dry operation Continues in the next page 5 Control System 137 SMGB0060 rev 1 12 2010 5 ...
Page 147: ...Heating operation Continues in the next page 5 Control System 139 SMGB0060 rev 1 12 2010 5 ...
Page 148: ...5 Control System 140 SMGB0060 rev 1 12 2010 ...
Page 153: ...Activation for protection device control 5 Control System 145 SMGB0060 rev 1 12 2010 5 ...
Page 162: ...Activation for protection device control 5 Control System 154 SMGB0060 rev 1 12 2010 ...
Page 166: ...Preheating control of compressor 5 Control System 158 SMGB0060 rev 1 12 2010 ...
Page 168: ...5 Control System 160 SMGB0060 rev 1 12 2010 ...
Page 180: ...6 Optional functions 172 SMGB0060 rev 1 12 2010 ...
Page 224: ...8 Troubleshooting 216 SMGB0060 rev 1 12 2010 ...
Page 263: ...RAS 4 6 HVRNS1E 8 Troubleshooting 255 SMGB0060 rev 1 12 2010 8 ...
Page 264: ...RAS 8 10 HRNSE 8 Troubleshooting 256 SMGB0060 rev 1 12 2010 ...
Page 269: ...RAS 8 10 HRNSE 8 Troubleshooting 261 SMGB0060 rev 1 12 2010 8 ...
Page 337: ...RAS 4 6 HVRNM1E Cycle and structural parts 9 Spare Parts 329 SMGB0060 rev 1 12 2010 9 ...
Page 340: ...RAS 4 6 HRNM1E Cycle and structural parts 9 Spare Parts 332 SMGB0060 rev 1 12 2010 ...
Page 342: ... Electrical parts 9 Spare Parts 334 SMGB0060 rev 1 12 2010 ...
Page 354: ... Electrical parts 9 Spare Parts 346 SMGB0060 rev 1 12 2010 ...
Page 356: ...RAS 8 10 HRNSE Cycle and structural 9 Spare Parts 348 SMGB0060 rev 1 12 2010 ...
Page 359: ... Electrical parts 9 Spare Parts 351 SMGB0060 rev 1 12 2010 9 ...
Page 440: ...10 Servicing 432 SMGB0060 rev 1 12 2010 ...
Page 464: ...11 Electrical checks of main parts 456 SMGB0060 rev 1 12 2010 ...
Page 481: ......