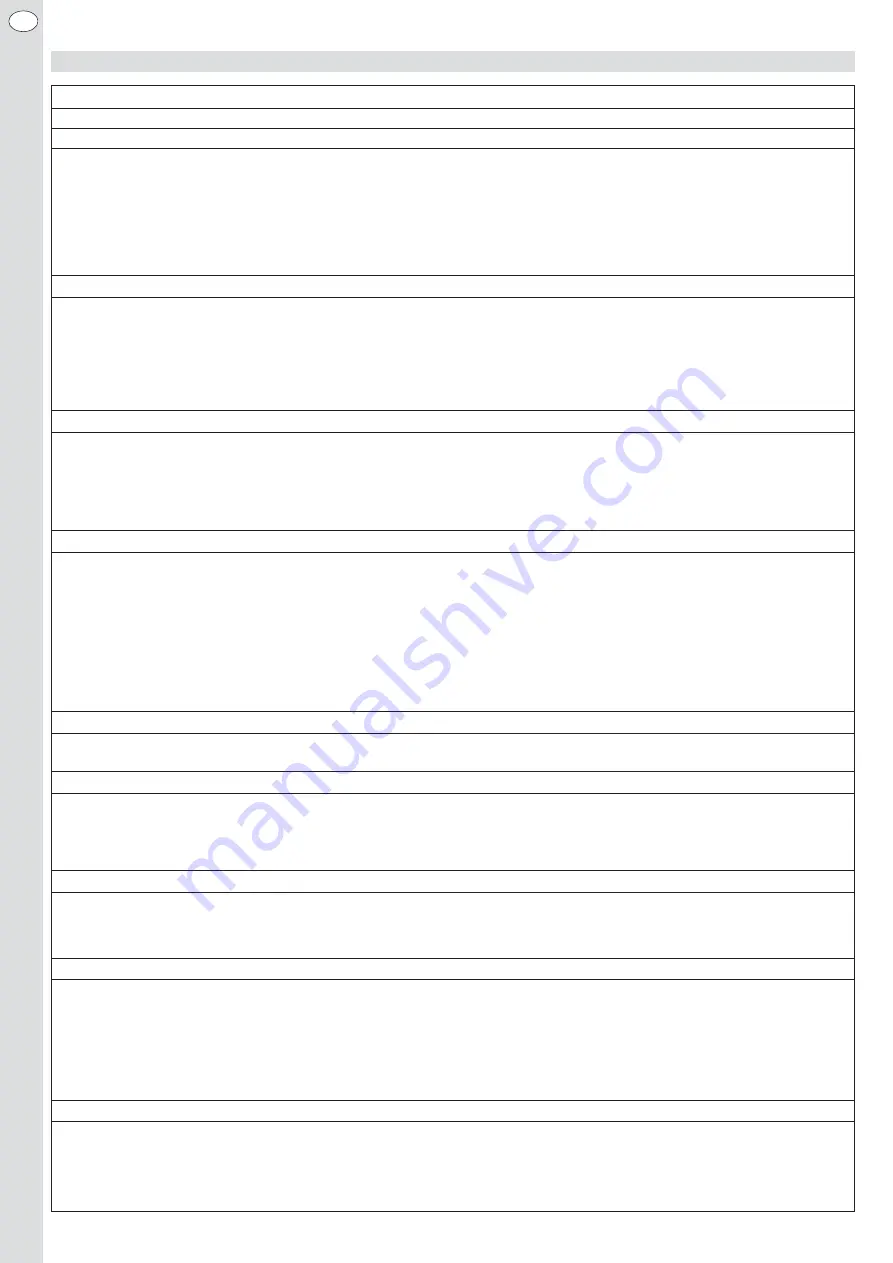
36
EN
Diagnosis
Cause
Rectification
1. Oil firing unit
Error signal lamp is not on
No voltage applied
Check wiring
Boiler temperature controller incorrectly adjusted
Adjust
Error signal lamp on
Oil firing unit switched to malfunction
Remedy malfunction
Oil firing unit defective
Replace
Incorrect wiring of terminal socket
Check wiring
Check oil pre-heater
Debug cause for malfunction by LED flashing code
Remedy debugged malfunction according
according to chapter 2.6 (only for Siemens LMO 14)
to error diagnosis point 2 ... 10
2. Motor
Motor does not start
Defective release thermostat of oil pre-heater
Replace oil pre-heater
Defective capacitor
Replace capacitor
Stiff bearing
Replace motor
Stiff oil pump
Replace oil pump
Loud noise caused by running motor
Motor defective
Replace motor
Bearing defective
Replace motor
Oil pump defective
Replace oil pump
3. Ignition
No generation of ignition sparks
Ignition unit defective
Replace ignition unit
Ignition cable defective
Replace ignition cable
Oil firing unit defective
Replace oil firing unit
Insulator defective
Replace ignition electrodes
Weak ignition spark
Incorrect position of the ignition electrodes
Position ignition electrodes
Ignition electrodes severely contaminated
Clean ignition electrodes
4. Oil pump
Inconsistent oil pressure, loud noise from
Intake pipe leaking (air entry)
Check oil supply (see chapter 3.5)
operating oil pump, no oil pressure is built up Oil supply not according to the specifications
Check oil supply (see chapter 3.5)
Intake pipe not de-aerated
De-aerate intake pipe
Oil stop valve closed
Open stop valve
Coupling defective
Replace coupling
Oil pump filter contaminated
Clean oil pump filter
Prefilter contaminated
Clean/replace prefilter
Oil pump drive defective
Replace oil pump
Paraffin sedimentation (+4 °C)
Install at a frost-free place
Fuel oil viscous (-1 °C)
Install at a frost-free place
5. Magnetic valve
Magnetic valve does not open
Coil of the magnetic valve defective
Replace coil of the magnetic valve
Oil firing unit defective
Replace oil firing unit
6. Flame monitoring
Fault shut-down without flame generation
Extraneous light (photoelectric current >5,5 μA)
Remove extraneous light
Photo conductive cell defective
Replace photo conductive cell
Fault shut-down with flame generation
Photo conductive cell contaminated
Clean photo conductive cell
Photoelectric current too weak (photoelectric
Reset burner
current < 55 μA)
7. Nozzle
Inconsistent atomisation, high CO and
Defective nozzle
Replace nozzle
soot emissions
Oil pressure not in compliance with specification
Adjust oil pressure
Diaphragm valve defective
Replace diaphragm valve
(only for burner versions E and F)
8. Baffle plate
Baffle plate / burner pipe very contaminated
Incorrect burner adjustment
Adjust burner according to chapter 3.8
and chapter 5 (basic adjustment table).
Inconsistent atomisation of the nozzle
Replace nozzle and diaphragm valve, if
necessary (only for burner versions E and F)
Nozzle is dripping
Replace diaphragm valve (only for burner
version E and F)
Incorrect nozzle type (spraying angle,
Insert nozzle according to specification
spraying characteristics, installation size)
(see chapter 4 and chapter 5)
9. Blower
Blower delivers not enough air
Blower wheel contaminated
Clean blower wheel
Blower wheel damaged
Replace blower wheel
Loud noise during blower operation
Blower wheel incorrectly positioned
Correctly position blower wheel
Blower wheel damaged
Replace blower wheel
Air flap incorrectly installed
Correctly install air flap
8.
Troubleshooting
Summary of Contents for HL 60 ALV.2
Page 15: ...15 DE 7 Explosionszeichnung mit Ersatzteilliste...
Page 20: ...20 DE 9 Brennerabmessungen HL 60 ALV 2 BLV 2 Schiebeflansch HL 60 ALV 2 BLV 2 Unitflansch...
Page 33: ...33 EN 7 Expanded view with spare parts list...
Page 38: ...38 EN 9 Burner dimensions HL 60 ALV 2 BLV 2 sliding flange HL 60 ALV 2 BLV 2 unit flange...
Page 51: ...51 FR 7 Vue clat e avec liste des pi ces de rechange...
Page 69: ...69 IT 7 Disegno esploso con elenco parti di ricambio...