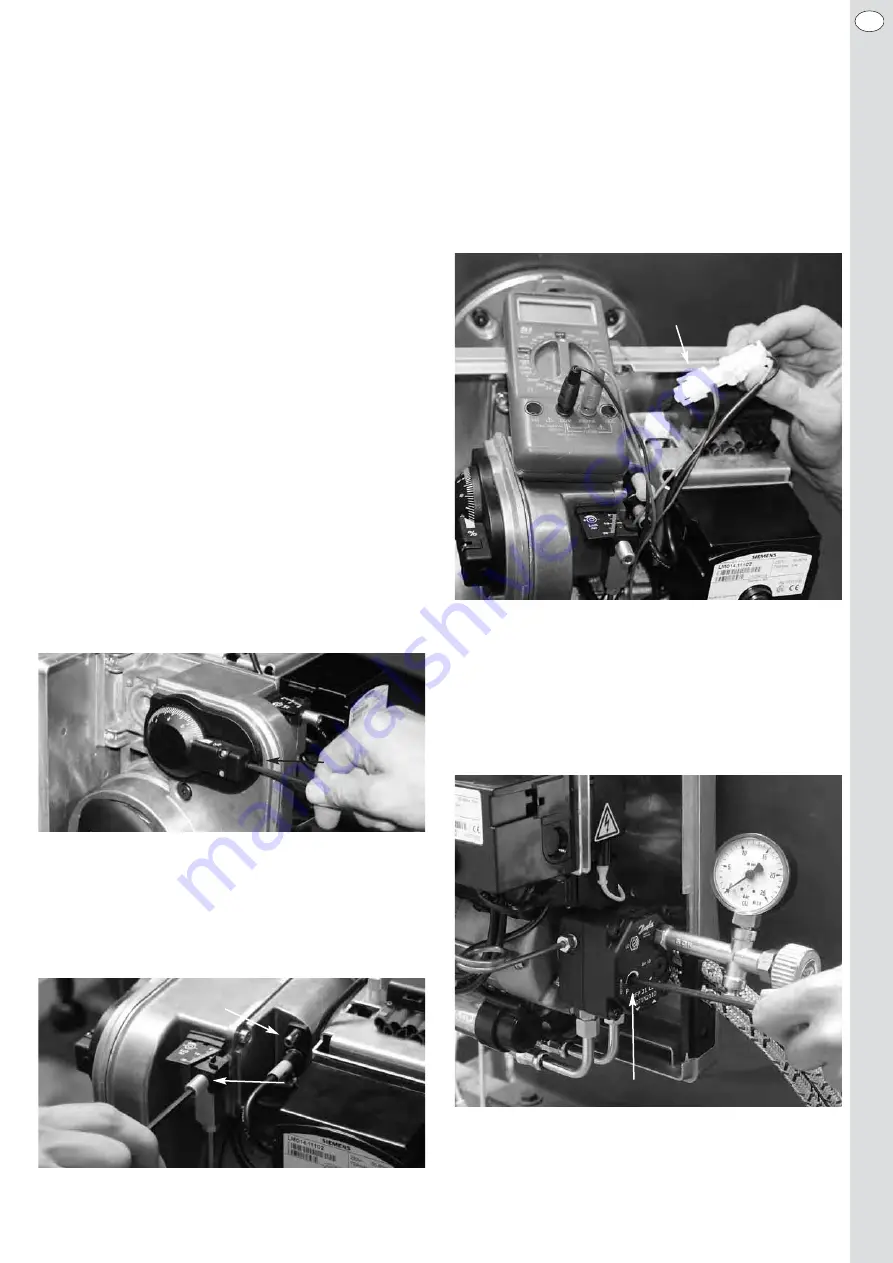
29
Distance between oil nozzle and baffle plate as well as position of
the baffle plate in the burner pipe
The distance between oil nozzle and baffle plate is 4mm for all combustion
capacities and versions of the mixing unit. This distance can be adjusted
by inserting the supplied hexagon socket screw (wrench size 4mm) bet-
ween the baffle plate and the oil nozzle. Alternatively to this adjustment
method, a distance washer with a thickness of 2.5mm is offered which
can be pushed onto the oil pre-heater serving as mechanical stop for the
baffle plate and thus ensuring the compliance with the distance of 4mm
between baffle plate and oil nozzles.
The position of the baffle plate in the burner pipe is defined by the distance
between the outlet edge of the burner pipe and the bottom of the baffle
plate. This distance can be measured with a depth gauge. For easy ad-
justment of the baffle plate position, an adjustment screw with appropriate
millimetre scale is provided at the rear side of the housing. The calibration
of the scale defines the distance between burner pipe and baffle plate at
the scale value 0.
Mixing units A/B:
Scale value 0
‰
15 mm of distance between burner pipe and baffle plate
Mixing units E/F:
Scale value 0
‰
17 mm of distance between burner pipe and baffle plate
All resulting scale values for the basic adjustment of the baffle plate
are provided as reference values in the basic adjustment table (see
chapter 5).
Adjustment of the combustion air flow
Provided that the correct mixing unit has been selected with regard to the
required combustion capacity and that the distance between oil nozzle
and baffle plate is also in compliance with the specifications, the
combustion air flow is adjusted with the air regulator and the baffle plate.
Adjustments should preferably be made with the set screw of the air
regulator. The scale values for the basic adjustment of the air regulator
and the baffle plate are provided as reference values in the basic adjust-
ment table (see chapter 5).
Air regulator
By turning the set screw for the air regulator counterclockwise, the air
flow from the blower is reduced and the blower pressure measured at
the pressure measuring nipple decreases, and the CO
2
content in the
exhaust air increases. Turning the set screw clockwise will open the
regulator and increase the blower pressure, thus reducing the CO
2
con-
tent in the exhaust air.
Baffle plate
By turning the set screw for the baffle plate clockwise, the ring gap bet-
ween burner pipe and baffle plate is reduced thus reducing the combus-
tion air volume with increasing blower pressure and increasing the CO
2
content of the exhaust air.
For reverse direction of rotation, the gap width and thus the combustion
air volume increases with decreasing blower pressure thus decreasing the
CO
2
content in the exhaust gas.
Blower pressure
A pressure measuring nipple is provided at the nozzle fitting cover for
measuring blower pressure. Reference values for blower pressure are pro-
vided in the basic adjustment table (see chapter 5). Make sure to observe
a blower pressure between 2.0 and 3.5mbar.
Photoelectric current
The photoelectric current must be measured in series with the photo
conductive cell (positive pole on terminal 12 with an internal resistance of
the measuring instrument of max 5k k
액
) using a DC micro amperemeter.
During operation, the photoelectric current must amount to 55 A and 100
μA at 230 V~. For this purpose, we recommend the measuring adapter
with order no. 10042.00010 which can be supplied as an accessory (see
chapter 10.1).
Adjustment of the oil mass flow
The injected oil mass flow is calculated from the size of the nozzle and
the injection pressure set at the pressure controller of the oil pump.
By turning the set screw clockwise, the oil pressure increases and thus
the injected oil mass flow increases, too. By turning the set screw
counterclockwise, the oil pressure is reduced. A pressure gauge
connection is provided at the pump for measuring the blower pressure.
The pump test kit shown in chapter 10.3 includes all pressure measuring
devices as well as connecting pieces. Reference values for nozzle size
and oil pressure are provided in the basic adjustment table (chapter 5).
EN
Set screw
Air regulator
Set screw
Baffle plate
Pressure
measuring nipple
Oil pressure set screw
Measuring
adapter
Summary of Contents for HL 60 ALV.2
Page 15: ...15 DE 7 Explosionszeichnung mit Ersatzteilliste...
Page 20: ...20 DE 9 Brennerabmessungen HL 60 ALV 2 BLV 2 Schiebeflansch HL 60 ALV 2 BLV 2 Unitflansch...
Page 33: ...33 EN 7 Expanded view with spare parts list...
Page 38: ...38 EN 9 Burner dimensions HL 60 ALV 2 BLV 2 sliding flange HL 60 ALV 2 BLV 2 unit flange...
Page 51: ...51 FR 7 Vue clat e avec liste des pi ces de rechange...
Page 69: ...69 IT 7 Disegno esploso con elenco parti di ricambio...