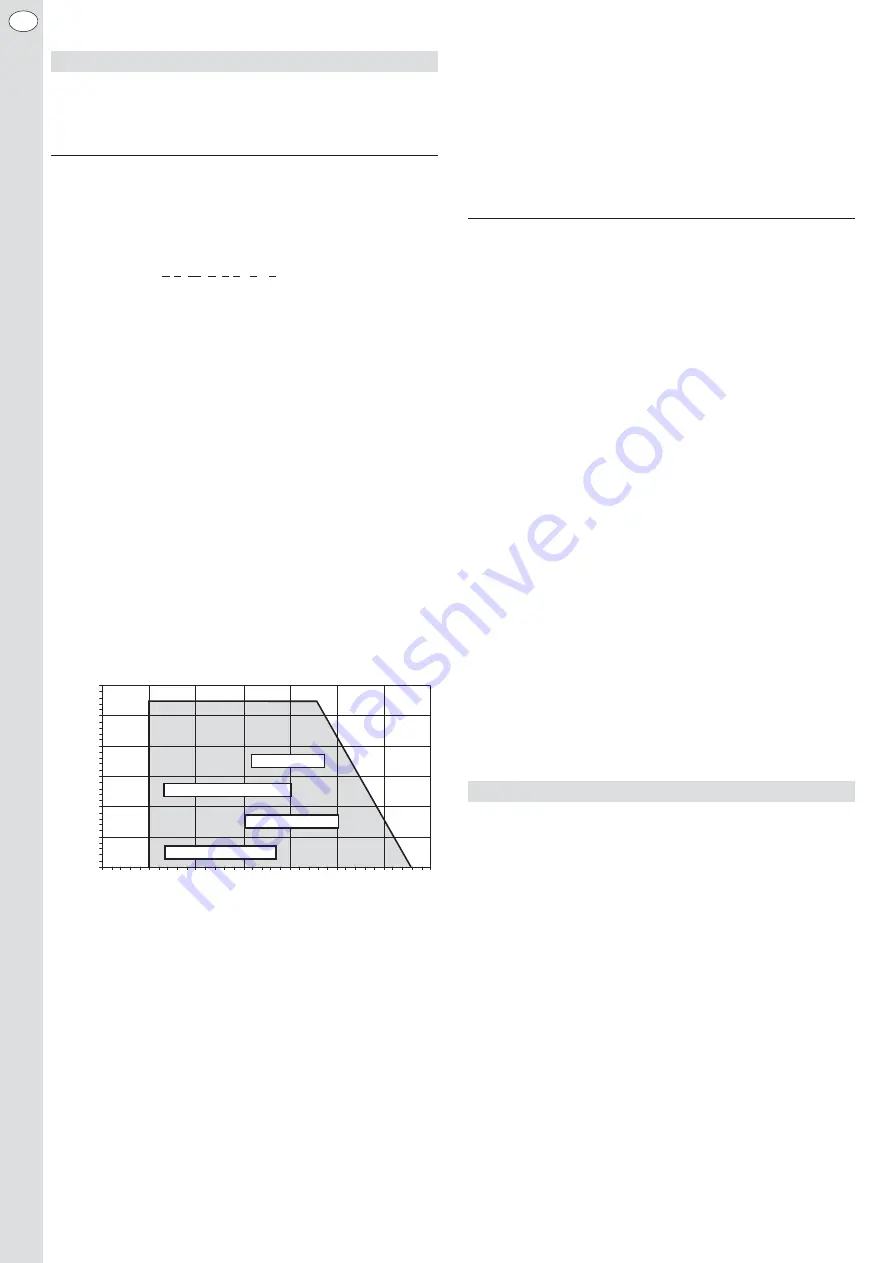
24
1.
Technical data
1.1 Range of models
Type
Oil nozzles
Oil
Combustion
throughput
capacity
m
in kg/h
Q
F
in kW
Class 2 emission limits according to DIN EN 267:1999-11
HL 60 ALV.2
0,40-1,00 Usgal/h 60°S 1,3 - 3,7
16-44
HL 60 BLV.2
0,85-1,35 Usgal/h 60°S 3,0 - 5,1
36-60
Class 3 emission limits according to DIN EN 267:1999-11
HL 60 ELV.2-S 0,40-1,10 Usgal/h 60°H 1,4 - 4,1
16-48
HL 60 FLV.2-S 0,85-1,25 Usgal/h 60°H 3,2 - 4,7
38-56
Type code:
H L 60 A L V . 2 - S
H
씮
Herrmann
L
씮
Light oil burner
60
씮
Series
A
씮
Mixing device (A - F)
L
씮
Air sealing
V
씮
Pre-heater
.2
씮
Blower wheel type
-S
씮
RAL-UZ9 special test
1.2 Certification
– DIN EN 267:1999-11: register number: 5G966/11
– Class 3 emission limits (only HL60 E/FLV.2-S)
– German ecolabel "Blue Angel" according to RAL-ZU 9: Contract no.
14415 (only HL60 E/FLV.2-S)
1.3 Operating range
The operating range of an oil burner describes the maximum combustion
chamber pressure depending on the oil mass flow. The operating ranges
were determined on a test boiler according to DIN EN 267:1999-11 and
refer to an altitude of 100m above sea level as well as to a room tempe-
rature of 20°C. The maximum achievable combustion capacity for devia-
ting marginal conditions depends on the start-up resistance of the furnace
which is influenced by the geometry of the combustion chamber, the heat
exchanger as well as the exhaust gas system.
1.4 Standard scope of delivery
1
Oil burner (with or without cover hood, depending on the design)
1
Flange (unit or sliding flange, depending on the design)
1
Seal for the flange (unit or sliding flange, depending on the design)
2
Oil tubes (length: 1100mm) -
Oil connection over 3/8" spigot nut
4
Cylinder head screws with SW4 DIN 7984 hexagon socket
M8 x 30 incl. washers for mounting unit or sliding flanges
1
Hexagon key with a nominal width of 4mm
1
7-pole socket, part of Euro female connector in accordance with
DIN 4791:1985-09 installed in the burner (plug connectors for the
boiler are not included in the scope of delivery)
1
Oil nozzle (installed in the burner)
1
Assembly and operating instructions
1
Oil burner operating instructions (heating room panel)
1
Fixation steel pin for oil burner operating instructions
Combustion chamber pressure in mba
r
1,0
0
0
0,1
0,2
0,3
0,4
0,5
0,6
2,0
HL 60 ALV.2
HL 60 ELV.2-S
HL 60 FLV.2-S
HL 60 BLV.2
3,0
4,0
5,0
6,0
7,0
Oil mass flow in kg/h
1.5 Fuel
– Fuel oil EL according to DIN 51603-1
– Heating oil EL, low sulphur, according to DIN 51603-1
– Fuel oil EL A Bio 10 (bio fuel oil according to DIN SPEC 51603-6, fuel
oil EL, low sulphur, with up to 10% of FAME according to the quality
requirements of DIN 14214)
1.6 Components
Component
Manufacturer
Model designation
Motor
Hanning
O 1A095-030
Oil pump
Danfoss
BFP 21 L3
Danfoss
BFP 21 L3 LE
Oil pre-heater
Danfoss
FPHB 5
Danfoss
FPHB-LE
Ignition
Danfoss
EBI 4
Photo conductive cell
Danfoss
LDS (blue)
Danfoss
LDS (red)
Firing unit
Siemens
LOA24
Siemens
LMO14
Firing unit WLE
Siemens
LMO44
1.7 Electrical data
Nominal voltage
230 V ~50 Hz
Starting power
ca. 435 W
Operating power
ca. 135 – 235 W
Contact rating of thermostats and switch min. 6 A~
1.8 Acoustic emissions
The sound pressure level at maximum burner performance is 57 dB(A).
The measurements were carried out with an accuracy class 2 measuring
device according to IEC 60651 at a (horizontal) distance of 2m.
1.9 Packing
Individual packaging (carton), base x height: 370x350x485 [mm]
Individual weight of the burner without packaging:
up to 12.5kg, depending on burner design
Individual weight of the burner with packaging:
up to 14.5 kg, depending on burner design
Collective packaging (18 single cartons on a Euro pallet), base x height:
1200x800x1605 [mm]
Weight of the pallet: approx. 280 kg
2.
Functional description
Oil burners HL60 A/B/E/F are designed as atomising burners with nozzle
mixing for the operation with EL heating fuel. The burner motor operated
with constant speed drives the fuel pump and the combustion air blower.
The fuel pump is designed as a gear pump delivering a continuous fuel
mass flow from the suction side to the pressure side. From there, part of
the fuel flows through a magnetic valve which is integrated in the pump
housing to the injection nozzle. Another part of the fuel is returned
through a pressure control valve to the suction side of the pump. The
injected fuel mass flow is calculated from the size of the nozzle and the
injection pressure set at the pressure control valve (5 bar<pi<18 bar). A
throttle unit is provided for the adjustment of the air volume flow to the
injected fuel mass flow. During burner operation and prior to each burner
start-up, fuel is heated in an oil pre-heater to a temperature of approxi-
mately 70°C. Through this process, fluctuations of fuel viscosity due to
temperature and quality which have an effect on the spraying process
and the fuel flow rate are decreased. The fuel spray is ignited by an elect-
ric spark that is formed by the application of high voltage between two
igniting electrodes. The function of each sub-system will be explained in
detail in the next chapters.
2.1 Mixing device
A yellow flame burner mixing device is used to burn the mixture. The main
components of the mixing unit in the burner tube include the baffle plate
which is firmly connected with the axially adjustable nozzle block and the
oil pre-heater and the spray nozzle which are also screw-connected with
the nozzle block.
EN
Summary of Contents for HL 60 ALV.2
Page 15: ...15 DE 7 Explosionszeichnung mit Ersatzteilliste...
Page 20: ...20 DE 9 Brennerabmessungen HL 60 ALV 2 BLV 2 Schiebeflansch HL 60 ALV 2 BLV 2 Unitflansch...
Page 33: ...33 EN 7 Expanded view with spare parts list...
Page 38: ...38 EN 9 Burner dimensions HL 60 ALV 2 BLV 2 sliding flange HL 60 ALV 2 BLV 2 unit flange...
Page 51: ...51 FR 7 Vue clat e avec liste des pi ces de rechange...
Page 69: ...69 IT 7 Disegno esploso con elenco parti di ricambio...