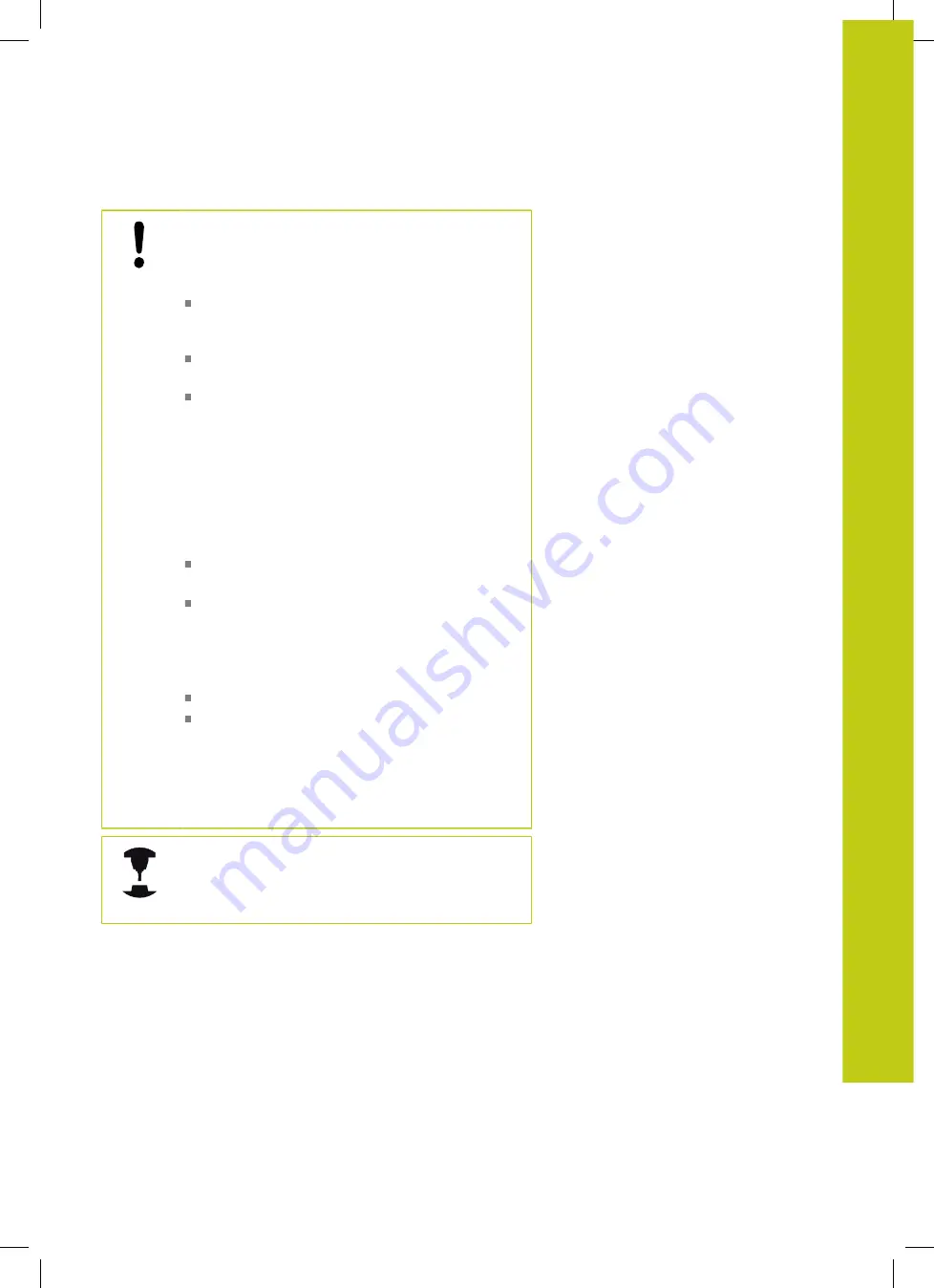
Test run 16.4
16
HEIDENHAIN | TNC 620 | ISO Programming User's Manual | 9/2016
569
Danger of collision!
The TNC cannot graphically simulate all traverse
motions actually performed by the machine. These
include
Traverse motions during tool change, if the
machine manufacturer defined them in a tool-
change macro or via the PLC
Positioning movements that the machine
manufacturer defined in an M-function macro
Positioning movements that the machine
manufacturer performs via the PLC
HEIDENHAIN therefore recommends proceeding
with caution for every new program, even when the
program test did not output any error message, and
no visible damage to the workpiece occurred.
With cuboid workpiece blanks, the TNC starts a
program test run after a tool call at the following
position:
In the working plane in the center of the defined
BLK FORM
In the tool axis, 1 mm above the
MAX
point
defined in the
BLK FORM
With rotationally symmetric workpiece blanks, the
TNC starts a program test run after a tool call at the
following position:
In the machining plane at the position X=0, Y=0
In the tool axis 1 mm above the defined
workpiece blank
In order to ensure unambiguous behavior during
program run, after a tool change you should always
move to a position from which the TNC can position
the tool for machining without causing a collision.
Your machine tool builder can also define a tool-
change macro for the
Test run
operating mode.
This macro will simulate the exact behavior of the
machine. Refer to your machine manual.
Summary of Contents for TNC 620 Programming Station
Page 4: ......
Page 5: ...Fundamentals ...
Page 28: ...Contents 28 HEIDENHAIN TNC 620 ISO Programming User s Manual 9 2016 ...
Page 57: ...1 First Steps with the TNC 620 ...
Page 77: ...2 Introduction ...
Page 110: ......
Page 111: ...3 Fundamentals file management ...
Page 166: ......
Page 167: ...4 Programming aids ...
Page 194: ......
Page 195: ...5 Tools ...
Page 234: ......
Page 235: ...6 Programming contours ...
Page 284: ......
Page 285: ...7 Data transfer from CAD files ...
Page 304: ......
Page 305: ...8 Subprograms and program section repeats ...
Page 323: ...9 Programming Q parameters ...
Page 384: ......
Page 385: ...10 Miscellaneous functions ...
Page 407: ...11 Special functions ...
Page 433: ...12 Multiple axis machining ...
Page 475: ...13 Pallet management ...
Page 480: ......
Page 481: ...14 Manual Operation and Setup ...
Page 549: ...15 Positioning with Manual Data Input ...
Page 554: ......
Page 555: ...16 Test Run and Program Run ...
Page 590: ......
Page 591: ...17 MOD Functions ...
Page 622: ......
Page 623: ...18 Tables and Overviews ...