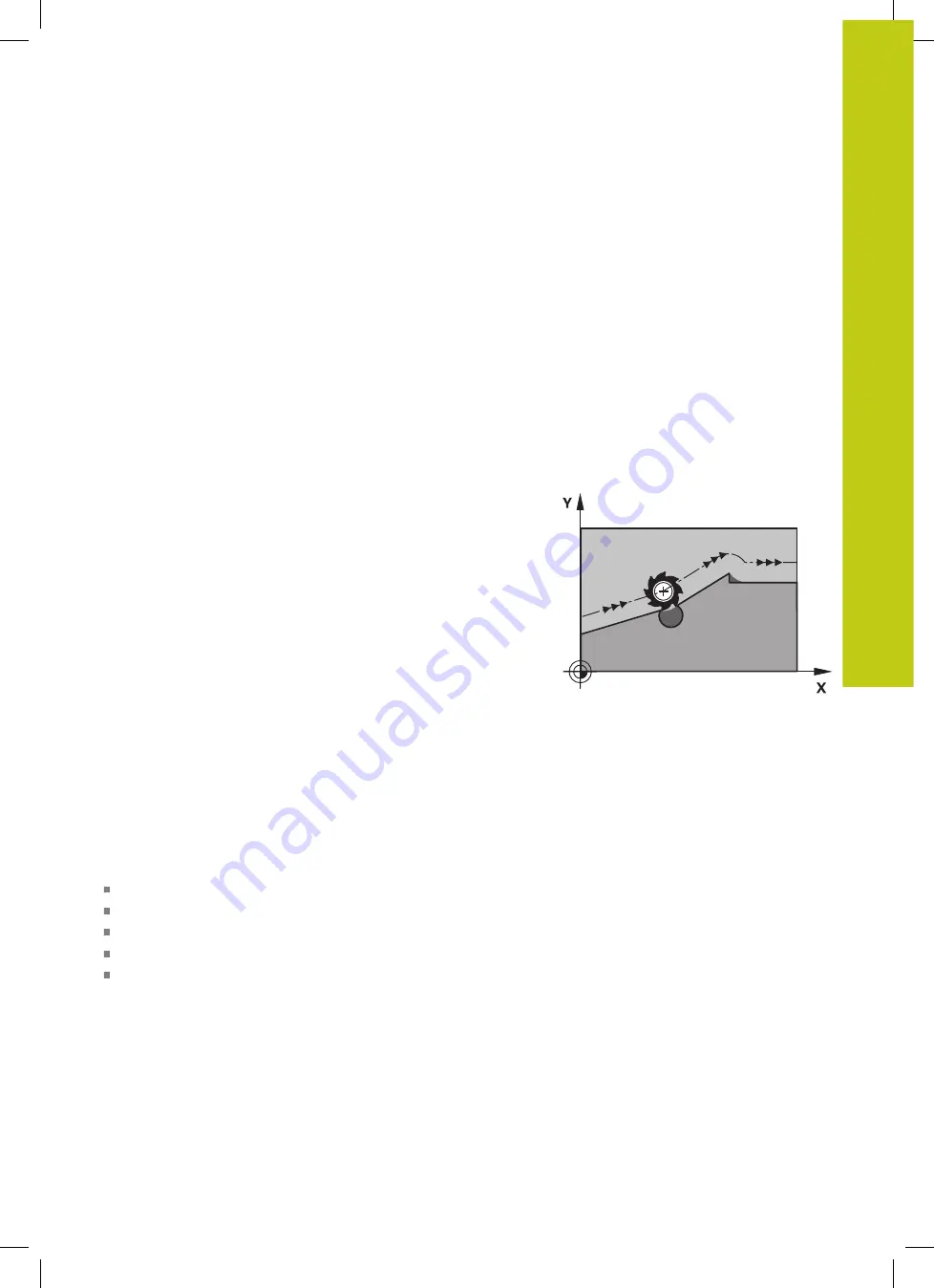
Miscellaneous functions for path behavior
10.4
10
HEIDENHAIN | TNC 620 | ISO Programming User's Manual | 9/2016
397
Calculating the radius-compensated path in advance
(LOOK AHEAD): M120 (Miscellaneous Functions
software option)
Standard behavior
If the tool radius is larger than the contour step that is to be
machined with radius compensation, the TNC interrupts program
run and generates an error message. M97” suppresses the error
message, but it results in dwell marks and will also move the
corner.
"Machining small contour steps: M97",
If the programmed contour contains undercut features, the tool
may damage the contour.
Behavior with M120
The TNC checks radius-compensated contours for undercuts and
tool path intersections, and calculates the tool path in advance from
the current block. Areas of the contour that might be damaged by
the tool are not machined (dark areas in figure). You can also use
M120 to calculate the tool radius compensation for digitized data or
data created on an external programming system. This means that
deviations from the theoretical tool radius can be compensated.
Use LA (
L
ook
A
head) behind M120 to define the number of blocks
(maximum: 99) that you want the TNC to calculate in advance.
Note that the larger the number of blocks you choose, the higher
the block processing time will be.
Input
If you enter M120 in a positioning block, the TNC continues the
dialog for this block by asking you the number of blocks LA that are
to be calculated in advance.
Effect
M120 must be located in an NC block that also contains radius
compensation
G41
or
G42
. M120 is then effective from this block
until
radius compensation is canceled with
G40
M120 LA0 is programmed, or
M120 is programmed without LA, or
another program is called with
%
the working plane is tilted with Cycle
G80
or the PLANE
function
M120 becomes effective at the start of the block.
Summary of Contents for TNC 620 Programming Station
Page 4: ......
Page 5: ...Fundamentals ...
Page 28: ...Contents 28 HEIDENHAIN TNC 620 ISO Programming User s Manual 9 2016 ...
Page 57: ...1 First Steps with the TNC 620 ...
Page 77: ...2 Introduction ...
Page 110: ......
Page 111: ...3 Fundamentals file management ...
Page 166: ......
Page 167: ...4 Programming aids ...
Page 194: ......
Page 195: ...5 Tools ...
Page 234: ......
Page 235: ...6 Programming contours ...
Page 284: ......
Page 285: ...7 Data transfer from CAD files ...
Page 304: ......
Page 305: ...8 Subprograms and program section repeats ...
Page 323: ...9 Programming Q parameters ...
Page 384: ......
Page 385: ...10 Miscellaneous functions ...
Page 407: ...11 Special functions ...
Page 433: ...12 Multiple axis machining ...
Page 475: ...13 Pallet management ...
Page 480: ......
Page 481: ...14 Manual Operation and Setup ...
Page 549: ...15 Positioning with Manual Data Input ...
Page 554: ......
Page 555: ...16 Test Run and Program Run ...
Page 590: ......
Page 591: ...17 MOD Functions ...
Page 622: ......
Page 623: ...18 Tables and Overviews ...