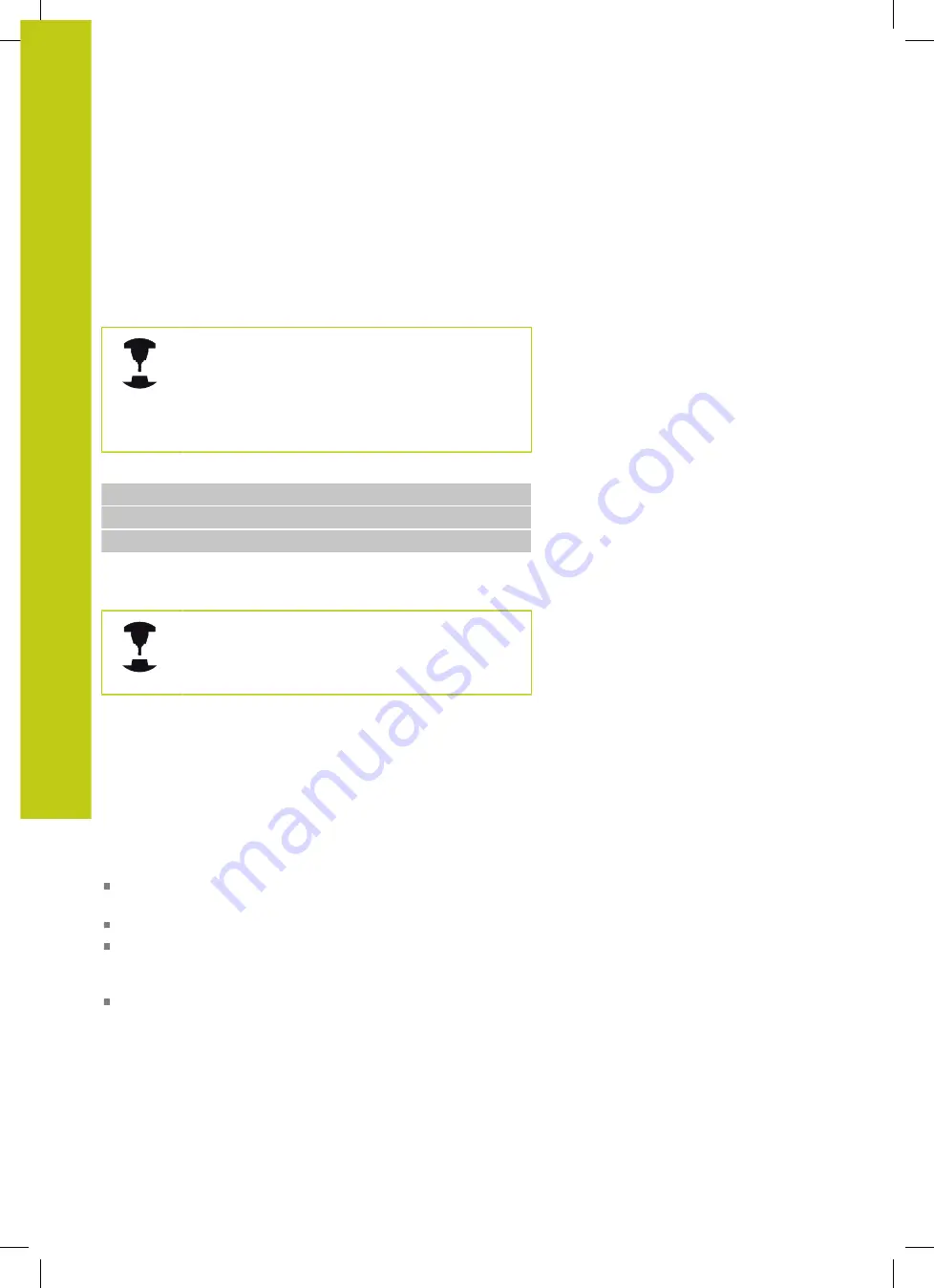
Multiple axismachining
12.6 Running CAM programs
12
474
HEIDENHAIN | TNC 620 | ISO Programming User's Manual | 9/2016
Possibilities for intervention on the control
Cycle 32
TOLERANCE
is available for the influencing of CAM
programs directly on the TNC. Also note the information in the
functional description for Cycle 32. Also note the interactions with
the chord error defined in the CAM system.
Further information:
Cycle Programing User's Manual
Refer to your machine manual.
Some machine tool builders provide an additional
cycle for adapting the behavior of the machine to
the respective machining operation, such as Cycle
332 Tuning. Cycle 332 can be used to modify filter
settings, acceleration settings, and jerk settings.
NC example blocks, Cycle 32
34 CYCL DEF 32.0 TOLERANCE
35 CYCL DEF 32.1 T0.05
36 CYCL DEF 32.2 HSC MODE:1 TA3
ADP motion control
Refer to your machine manual.
This feature must be enabled and adapted by the
machine tool builder.
An insufficient quality of data in NC programs created on CAM
systems frequently causes inferior surface quality of the milled
workpieces. The
ADP
(Advanced Dynamic Prediction) feature
expands the conventional look-ahead of the permissible maximum
feed rate profile and optimizes the motion control of the feed axes
during milling. This enables clean surfaces with short machining
times to be cut, even with a strongly fluctuating distribution
of points in adjacent tool paths. This significantly reduces or
eliminates the reworking complexity.
These are the most important benefits of ADP:
Symmetrical feed-rate behavior on forward and backward paths
with bidirectional milling
Uniform feed rate curves with adjacent cutter paths
Improved reaction to negative effects (e.g. short, step-like
stages, coarse chord tolerances, heavily rounded block end-
point coordinates) in NC programs generated by CAM system
Precise compliance to dynamic characteristics even in difficult
conditions
Summary of Contents for TNC 620 Programming Station
Page 4: ......
Page 5: ...Fundamentals ...
Page 28: ...Contents 28 HEIDENHAIN TNC 620 ISO Programming User s Manual 9 2016 ...
Page 57: ...1 First Steps with the TNC 620 ...
Page 77: ...2 Introduction ...
Page 110: ......
Page 111: ...3 Fundamentals file management ...
Page 166: ......
Page 167: ...4 Programming aids ...
Page 194: ......
Page 195: ...5 Tools ...
Page 234: ......
Page 235: ...6 Programming contours ...
Page 284: ......
Page 285: ...7 Data transfer from CAD files ...
Page 304: ......
Page 305: ...8 Subprograms and program section repeats ...
Page 323: ...9 Programming Q parameters ...
Page 384: ......
Page 385: ...10 Miscellaneous functions ...
Page 407: ...11 Special functions ...
Page 433: ...12 Multiple axis machining ...
Page 475: ...13 Pallet management ...
Page 480: ......
Page 481: ...14 Manual Operation and Setup ...
Page 549: ...15 Positioning with Manual Data Input ...
Page 554: ......
Page 555: ...16 Test Run and Program Run ...
Page 590: ......
Page 591: ...17 MOD Functions ...
Page 622: ......
Page 623: ...18 Tables and Overviews ...