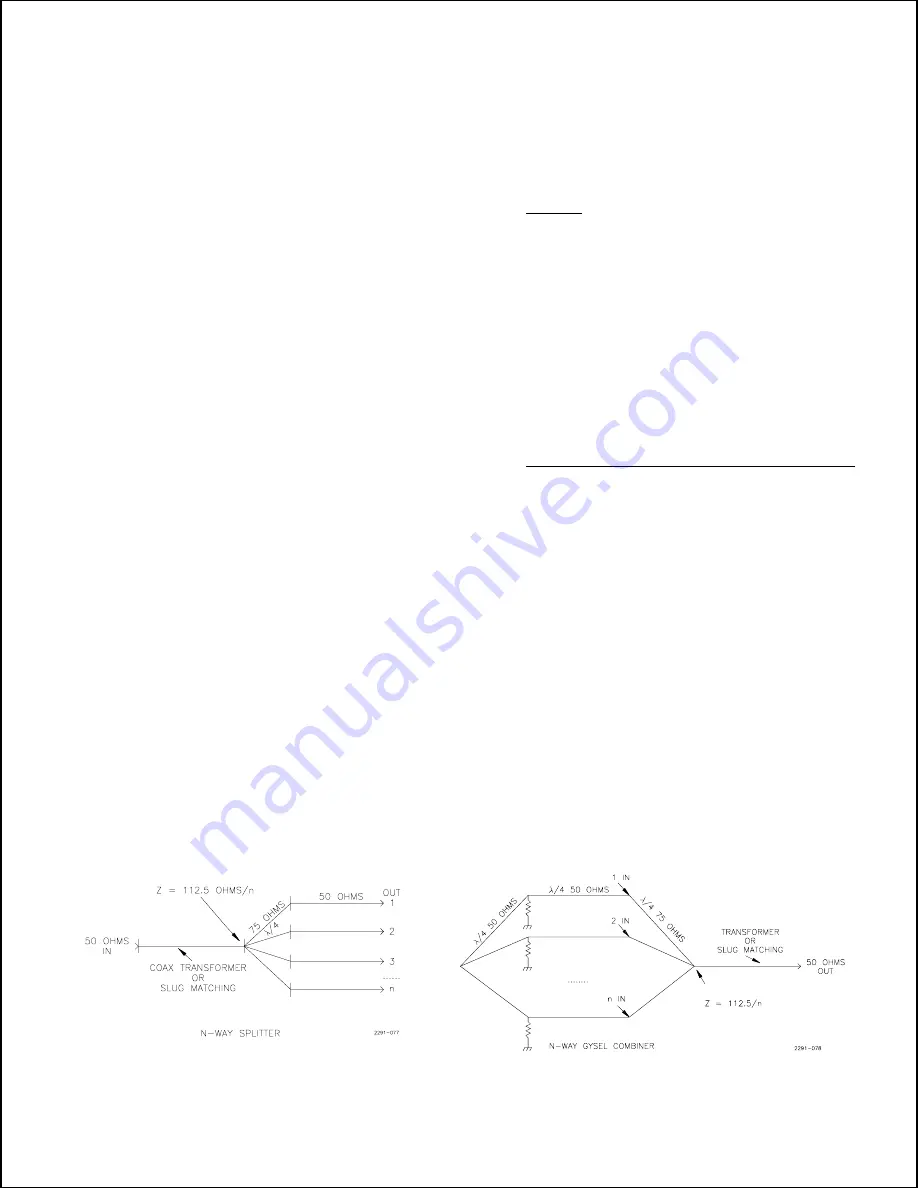
For example, if point A is at a logic “high,” current will flow
through CR3, which will become an RF short circuit to ground.
The hybrid port at U3 pin 2 will then see C4 as an RF impedance
to ground. If point A is low, CR3 will look like an open circuit,
and no RF current can flow through C4. The capacitance seen by
that hybrid port will be maximum when points A through F are
all at logic “high,” and minimum when points A-F are at logic
low.
The control logic ensures that the binary “word” sent through
points A-F to PIN diodes CR3 through CR8 is the same as the
binary “word” sent through points G-L to PIN diodes CR10
through CR15. Thus the impedances seen at pins 2 and 5 of
hybrid U3 will be the same, and all of the power reflected back
into the hybrid will pass to the output or “reject” port at pin 6,
with none of it being reflected back to the input at pin 1.
Hybrid U5, PIN diodes CR18 through CR29, capacitors C23
through C38, and points M through X form an identical phase
shift network for the lower RF path.
4.2.5.2
Control Logic and Hardware
The control hardware includes digital phase control, switch
debouncing, current buffering, and gain path balancing. An LED
(DS1) indicates when a phase setting beyond the range capability
is requested.
A phase count is maintained with two presettable four-bit bidi-
rectional counters (U7, U8). The preset inputs allow the 16
position rotary switch (S2) to act as non-volatile memory for the
phase setting on power-up.
When the module is in OPERATE mode, U6 generates a clock
frequency used by the counters. When the front panel switch (S1,
“Phase +/-”) is depressed, impulses at the clock frequency are
sent to the counters. The direction of count (up or down) is
logically steered from the same switch, and determines the
direction of the phase change.
The counter output is sent directly to one of the phase shifters.
Phase count lines for the second phase shifter are driven by a
ones-complement inversion (performed by U9 and U10), so that
as the phase through one phase shifter smoothly increases, the
phase shift through the other decreases, and vice versa.
Switch debouncing is performed with RC low-pass filters. Op-
amps configured as comparators (U15) are used sense when the
low-pass output voltage exceeds a transition level. A single
output transition is ensured by establishing a 33% comparator
hysteresis window.
Current buffering for the LED and PIN diodes is performed using
discrete Darlington transistors (Q1, Q2, Q3) and DIP transistor
arrays (U11 through U14).
4.2.6
Preamp
(Refer to Preamp schematic)
An RF preamp is used in some transmitter configurations to
compensate for multiple-way power division.
The preamp input is taken from the exciter or optional exciter
switcher. Its output feeds the aural or visual drive chain. The
preamp module can provide up to 1 watt of drive power. Gain is
adjustable from 4 to 24 dB, and its nominal setting depends on
the transmitter configuration.
Idle current is 700 mA or less at 24 volts DC. The supplies used
by the preamps are powered whenever AC is supplied to the
cabinet.
4.2.7
Cabinet-Level Splitter And Combiner Circuits
4.2.7.1
Visual Chain
In 15, 30, 45, and 60 kW systems, the visual drive is applied to
a power divider in each visual PA cabinet. Each divider splits the
signal 16 ways in a low band system, or 17 ways in a high band
system, and applies these signals to the visual PA modules.
The PA modules amplify the outputs of the divider by 18.5 dB
at low band, or 13.2 dB at high band.
The outputs are then combined by a 16- or 17-way Gysel Net-
work combiner to provide a combined output from each cabinet.
In systems at other power levels, the number of ports on the
combiner or divider vary. For example, in 10 kW and 20 kW
systems, 12-way dividers and combiners are used. 5 kW systems
have a 6-way divider and a 6-way combiner.
The combiner contains isolation resistors attached to a heat pipe.
These loads provide isolation between module ports, allowing
shut off and removal of any module without affecting the per-
formance of the remaining modules.
Under normal operation with all modules installed and operating,
these loads absorb minimal power. Should one or more of the
modules be disabled, shut off, disconnected from its power
Figure 4-1. N-Way Splitter
Figure 4-2. N-Way Gysel Combiner
Section IV - Theory of Operation
888-2365-001
4-3
WARNING: Disconnect primary power prior to servicing.
Summary of Contents for Platinum Series
Page 4: ......
Page 6: ......
Page 8: ...ii 888 2365 001 02 24 97 WARNING Disconnect primary power prior to servicing ...
Page 12: ...This page left blank intentionally ...
Page 22: ...1 10 888 2365 001 WARNING Disconnect primary power prior to servicing ...
Page 52: ...3 20 888 2365 001 Rev B 1 11 1999 WARNING Disconnect primary power prior to servicing ...
Page 62: ...4 10 888 2365 001 WARNING Disconnect primary power prior to servicing ...
Page 64: ...4 12 888 2365 001 WARNING Disconnect primary power prior to servicing ...
Page 66: ...4 14 888 2365 001 WARNING Disconnect primary power prior to servicing ...
Page 80: ...5 14 888 2365 001 Rev B 1 11 1999 WARNING Disconnect primary power prior to servicing ...