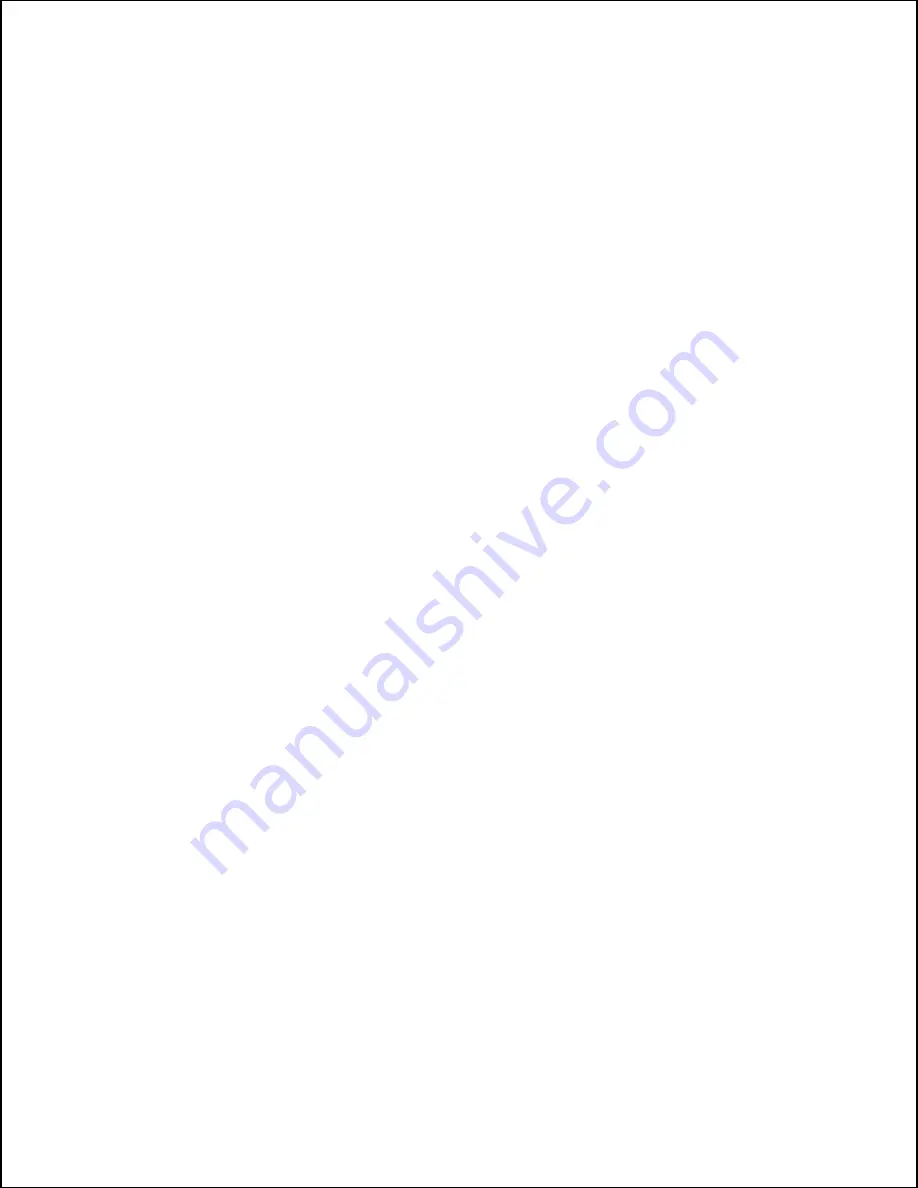
The output of U3 is supplied to the monitor and other on-board
logic.
4.2.8.2.4
Power Up Detector (sheet 1)
This logic is made up of U7, CR1, C3, and several resistors. The
power up/reset detector monitors the +5 volts applied to the
controller. If the +5 falls below about 4.35 volts, certain logic
functions are forced to a reset condition. When the +5 volts goes
above about 4.5 volts the reset line is released to its normally high
state. Capacitor C3 provides a time delay on power returns,
holding the reset line low for a short time.
4.2.8.2.5
VSWR Fold-back (sheet 2)
The detection and control circuits for both aural and visual
foldback are the same.
The VSWR Foldback works in conjunction with the exciter to
reduce the power output of the transmitter under varying VSWR
conditions. This circuit is normally set to become active around
1.2:1 visual VSWR, or 1.4:1 aural VSWR, but the exact value at
which fold-back starts will vary somewhat with the angle of the
reflection coefficient, the location of the reflected directional
coupler on the transmission line, and the amount of aural-visual
cross-coupling through the diplexer.
A reflected visual power RF sample is fed to J8 on the main
controller board (see sheet 6), where it is peak detected by CR21
and C31-C32-C33 and passed on to calibration pot R87. The arm
of R87 is connected to U36, a voltage follower, to buffer the DC
signal for distribution to the VSWR system and monitor. The bias
adjust pot R86 is set to compensate for the forward voltage drop
of CR21 with no RF signal applied, and is normally about 30 mV
at the cathode of CR21. The input trap, consisting of L5 and C52
in series, is set to shunt the 2nd harmonic away from the detector.
(This trap is deleted in later equipment.)
Returning to sheet 2, the Foldback Amp (U10A) provides gain
for the foldback control voltage to the exciter, and will try to
maintain the transmitter output at the threshold set by R20. R20
sets the threshold, keeping U10’s output in saturation until the
positive input is raised above the value of the inverting input. At
that point, the amplifier has a gain of 10.
Diode CR75 provides a diode drop to compensate for op-amp
input offset errors, which cause the output of U10A to rise above
ground as the threshold set point of U10A is increased. The
output of U10A is connected through R23 to the exciter, and
through R22 to the U10B, the Foldback Active detector. The
inverting (-) input to the active detector is biased to about 0.175
mV by CR71, R145, & R144, so that the hysteresis induced by
R22 and R24 will not keep the detector output on when the output
of U10A is at ground level.
The output of active detector U10B is connected to U53, a CMOS
buffer, which drives several ICs. The active detector output goes
high when the noninverting (+) input is raised about 175 mV
above the inverting (-) input. The output will swing to a logic
high level, causing U53 to drive the U13 and U12 inputs high.
This in turn will cause LED DS1 and the front panel FOLD-
BACK ACTIVE fault indicator to illuminate. This signal is also
passed to the VSWR overload logic to disable the forward power
memory detector, so that if foldback is active, a VSWR fault will
not be latched by O/L latch U24.
4.2.8.2.6
Fault Status Drivers (sheet 3)
The front panel indicators are driven by high-current buffers
which allow logic signals to control the indicator lamps on the
front panel. Test switch S3 is used to test the lamps by turning
on all indicators in the fault display.
4.2.8.2.7
VSWR Overload (sheet 4)
Both the aural and visual VSWR Overload (O/L) detectors are
the same.
The VSWR Overload logic works in conjunction with the mod-
ule VSWR protection circuits. When the reflected power is
greater than the O/L set point, comparator U23A will turn on,
clocking U22A, a one-shot with an output duration of three
seconds. This will cause the foldback output to the exciter to
reduce power to zero for about 100 mS, than ramp back up to
normal power level in 300 mS if the foldback is not active. If the
reflected power is still above the foldback set point, the power
will return to some lower power level controlled by the foldback
circuit, and the overload detection circuit will be disabled.
The module VSWR circuit will also turn off the module and a
module fault will be sent to the monitoring system and a module
summary fault will be indicated on the fault indicator.
If the foldback circuit has been disabled by jumpers J18-2 to 3
or J19, the exciter will not reduce the output level as above; it
will instead continue to produce output power. At the end of the
three second window established by U22A, U22B is fired, clock-
ing U24 to the state of its “D” input. With foldback disabled, the
former level of the forward power detector voltage sample is
stored on capacitor C17. If the voltage at the noninverting (+)
input to U23B is not above the stored sample voltage at the
inverting (-) input, a logic high is clocked into U24 indicating a
VSWR fault. However, if the noninverting input voltage is above
the inverting input voltage, the logic low clocked in to U24 will
indicate no VSWR fault condition. The VSWR O/L indicator will
have been active for three seconds, however, which allows a
remote control system to log the intermittent VSWR condition.
R51 is used to set the overload detection threshold to a given
VSWR.
4.2.8.2.8
Remote Control Inputs (sheet 5)
All of the remote control inputs from J14 are conditioned upon
the position of the LOCAL switch on the control cabinet front
panel. When the transmitter is in LOCAL mode, the yellow
indicator is lighted and all remote inputs are disabled.
The remote inputs are conditioned by optocouplers U30-U32,
inverted by U52 and applied to the inputs of U33, the remote
command buffer. The command buffer is a tri-state driver that
interfaces to the local command functions. When the LOCAL
switch is active, its signal inhibits outputs from U33, disabling
all of the remote command signals.
4.2.8.2.9
Peak Detectors (sheet 6)
RF peak detectors are used for power and VSWR measurement.
Section IV - Theory of Operation
888-2365-001
4-5
WARNING: Disconnect primary power prior to servicing.
Summary of Contents for Platinum Series
Page 4: ......
Page 6: ......
Page 8: ...ii 888 2365 001 02 24 97 WARNING Disconnect primary power prior to servicing ...
Page 12: ...This page left blank intentionally ...
Page 22: ...1 10 888 2365 001 WARNING Disconnect primary power prior to servicing ...
Page 52: ...3 20 888 2365 001 Rev B 1 11 1999 WARNING Disconnect primary power prior to servicing ...
Page 62: ...4 10 888 2365 001 WARNING Disconnect primary power prior to servicing ...
Page 64: ...4 12 888 2365 001 WARNING Disconnect primary power prior to servicing ...
Page 66: ...4 14 888 2365 001 WARNING Disconnect primary power prior to servicing ...
Page 80: ...5 14 888 2365 001 Rev B 1 11 1999 WARNING Disconnect primary power prior to servicing ...