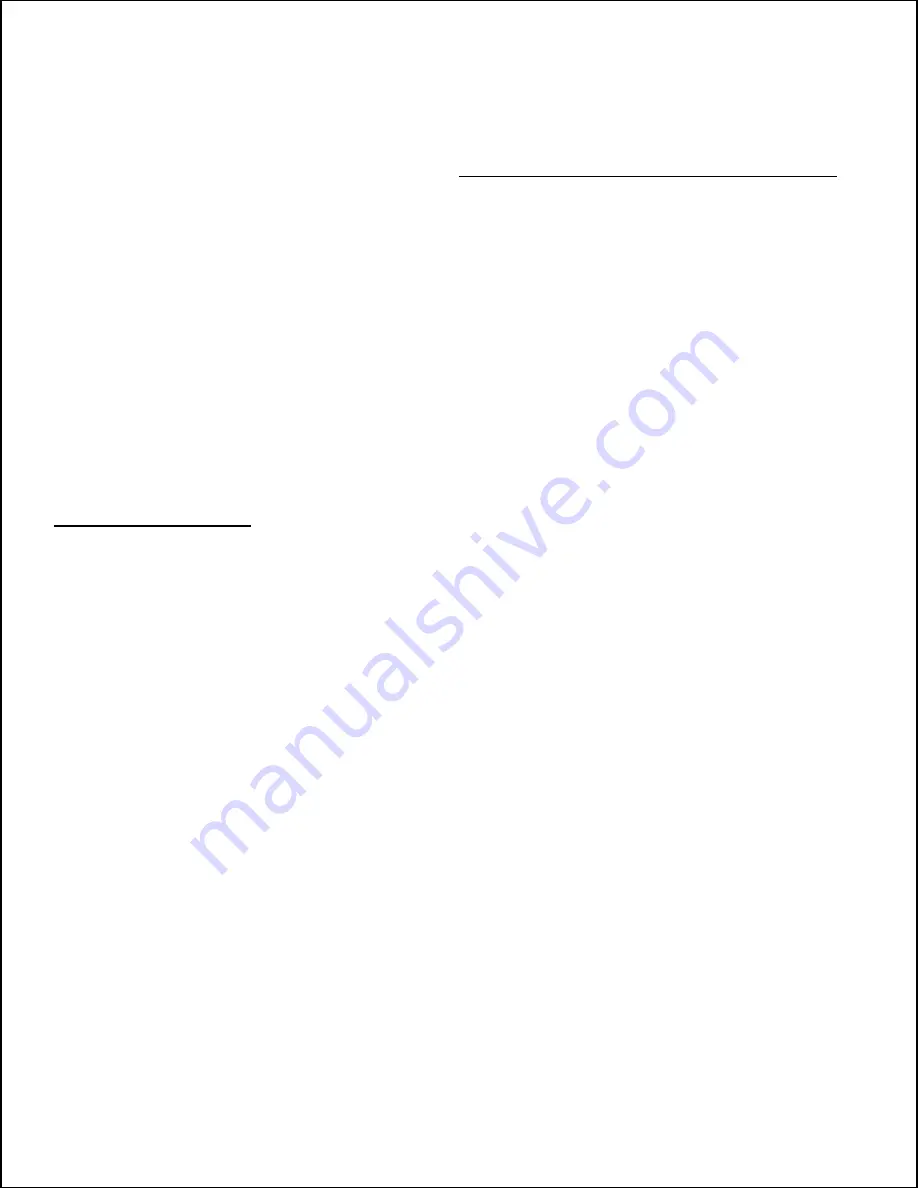
a PS OK signal to the controller, removing the PS faults and
turning off the fault indicators. All of these signals are supplied
to the monitoring system as status points.
4.2.8.9
Module Enable (sheet 8)
The module enable PAL circuit performs the required gating to
enable modules with PS-1&2 OK or STSET. The output of the
PAL is passed through U50, an inverting buffer, to the module
enable lines.
The logic for the PALs can be seen in Table 4-1 for the normal
conditions. Signals from the drive chain change-over logic alter
the gating of the PALs in the Aural/Driver PA cabinet. When the
parallel drive chain option is used, the PALs are programmed
differently.
4.2.8.10
Analog Channels (sheet 6)
The analog channels on the slave controller pass analog values
over the bus to the A/D converter on the monitor board, where
they are digitized and calibrated for display. The slave address
for a channel is sent from the monitor to the slave, where it is
latched in U9. This address selects the analog channel to be
returned on the bus to the monitor.
4.2.8.11
Analog Channel
CABINET ADRANALOG FUNCTION
00
RF 1 peak detector
01
RF 2 peak detector
02
RF 3 peak detector
03
RF 4 peak detector
04
RF 5 peak detector
05
RF 6 peak detector
06
Not used
07
Power supply 1 volts
17
Power supply 1 current
27
Power supply 2 volts
37
Power supply 2 current
47
Not used
57
Not used
67
Not used
77
Not used
Analog channels 07 through 77 have a trim adjustment to cali-
brate the power supply readings. Channels 00 through 05 have
calibration pots on each peak detector.
4.2.8.12
Status Ports (sheets 3 and 4)
The status ports enable the Monitor to read the fault status of the
modules and other functions of the cabinet controller over the
monitor bus. The fault lines are optocoupled to U28, U31 & U36
to U26 & U27. When the RD* select line is asserted low, the latch
will freeze the data at its input and place it on D0 -D7 bus to the
monitor bus drivers, which in turn place the data on the monitor
bus for the monitor to read.
In systems with parallel drive paths, data indicating aural and
visual changeover faults is latched in U33-U34 for aural faults,
and U42-U43 for visual faults. These latches are clocked by the
respective changeover logic. Once a driver faults, the slave must
be manually reset to restore the driver chain to the normal state.
The other status port, U35, is a tri-state buffer. It does not latch
the data on the input pins.
4.3
Basler 50 Volt DC Power Supply
(See 50 V power supply and control board schematics)
The Basler Electric 15 kW power supply operates from a three
phase AC line (208/240 volts AC), delivering 50 volts DC at a
rated current of 300 amps.
The three phase AC input can be connected for the following
voltages:
a. 208 Delta, 220 Delta, 240 Delta
b. 360/208 WYE, 381/220 WYE and 416/240 WYE
The primary of T1, T2, and the cooling fan are paralleled from
terminal block 1. Also connected in parallel to TB1 are power
factor correction circuits consisting of C38, C39, and C40 (model
100 and 101) and an additional inductor L2 (model 102 only).
The low voltage secondary of power transformer T1 is applied
to a six SCR bridge mounted on the heat sink assembly consisting
of power blocks 1, 2, and 3. Also at this point, the snubber PC
board, consisting of R1 to R9 and C1 to C9, is connected. The
snubber assembly protects the SCRs from noise and line tran-
sients, and limits the rate of change of voltage across the SCRs
to prevent breakdown.
The heat sink assembly also contains catch diode CR1 and
thermal cutout switch S1. The regulated DC output of the six
SCR bridge is filtered by inductor L1, and by an exteranl bank
of six parallel capacitors totalling 0.72 farad. The DC current is
sensed by R100, a 300 amp to 50 mV shunt.
Transformer T2 provides power for the electronics on the control
board assembly, as well as the synchronization for the firing
pulses to the SCR bridge. Power is provided by Q8, and its
associated circuitry supplies all the devices located on the control
board assembly. A 12 VDC signal applied to J1-2 (positive) and
J1-1 (return) energizes optocoupler U4. As U4 conducts, it turns
off Q16, Q17, and Q18 which turn off DS1 (overvoltage LED),
DS3 (overcurrent LED), and DS2 (overcurrent LED) respec-
tively. Also, Q7 turns off, which allows the 24V regulator to start,
thus beginning the power supply’s start-up sequence.
When the 24 VDC turns on, Vcc is applied to error amplifier U5,
and sequence synchronizing amplifiers: U1, U2, Q1 to Q6, Q10 to
Q15, and T1 to T6. Phase voltages provided by T2 secondaries are
filtered and rectified. This rectified signal is summed with a delay
angle balance adjust, R62 to R66, then applied to the sequence
synchronizing comparators. The sequence synchronizing compara-
tor’s other input is from the error amplifier and soft start circuit. The
error amplifier composed of U5, U3, and associated circuit compo-
nents senses the DC output of the SCR bridge. If the output voltage
sensed by the error amplifier is too low, the sequence synchronizing
amplifier will pulse the SCRs with the correct phase polarity in order
to increase the output voltage.
4-8
888-2365-001
WARNING: Disconnect primary power prior to servicing.
Summary of Contents for Platinum Series
Page 4: ......
Page 6: ......
Page 8: ...ii 888 2365 001 02 24 97 WARNING Disconnect primary power prior to servicing ...
Page 12: ...This page left blank intentionally ...
Page 22: ...1 10 888 2365 001 WARNING Disconnect primary power prior to servicing ...
Page 52: ...3 20 888 2365 001 Rev B 1 11 1999 WARNING Disconnect primary power prior to servicing ...
Page 62: ...4 10 888 2365 001 WARNING Disconnect primary power prior to servicing ...
Page 64: ...4 12 888 2365 001 WARNING Disconnect primary power prior to servicing ...
Page 66: ...4 14 888 2365 001 WARNING Disconnect primary power prior to servicing ...
Page 80: ...5 14 888 2365 001 Rev B 1 11 1999 WARNING Disconnect primary power prior to servicing ...